工程分类
更多>>![]() |
|
![]() |
|
![]() |
|
![]() |
|
![]() |
|
![]() |
|
![]() |
|
![]() |
|
![]() |
|
![]() |
|
![]() |
|
![]() |
|
![]() |
|
![]() |
|
![]() |
|
![]() |
|
![]() |
|
![]() |
|
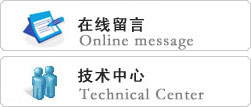
联系人:
电话:0511-88791451
手机:13951280541
邮箱:jfchen@ujs.edu.cn
地址:镇江市学府路80号
最新文章
您的位置:网站首页 > 最新文章熔制瓷釉的全电熔窑
目前,我国搪瓷行业熔制瓷釉的窑炉都采用煤、柴油、煤气或天然气等燃料。窑炉结构有坩埚窑、池窑和机械回转窑。这些窑炉都存在热效率低的缺陷,而坩埚窑则劳动强度很大,池窑及回转窑又存在原料挥发损失大、瓷釉质量不易控制等问题;燃料的烟气、炉渣及噪声对环境造成严重污染
瓷釉电熔技术是近年来国际上发展起来的一项新技术。用电熔法制瓷釉越来越引起搪瓷行业的注意。
瓷釉在常温下是绝缘体。而在高温时,熔融瓷釉是一种良好导体。熔化瓷釉的热量是通过瓷釉中的碱性金属离子往复运动所产生的。而碱性金属离子的迁移能力通常随着温度的升高而增大。在熔化瓷釉的电熔窑中插入电极,加上50Hz的交流电,利用电流的焦耳效应提供热能。电能的热效率达90%以上。
瓷釉的导电率与温度及成分呈函数关系。瓷釉的电阻率基本上随Na2O的含量而变化,取决于瓷釉的化学配方。配方一定,导电率主要取决于其温度的高低。
在定量分析计算时,瓷釉的电阻率计算不易得到精确的结果。一些资料介绍的计算公式不简便,规定使用范围狭小,而搪瓷配方的组成变动较大。在设计过程中采用实测方法,测出的结果作为设计依据。
电极的作用是将交流电流馈入熔融的瓷釉中。它是电熔瓷釉中的关键部件。电极应有足够的耐热性,以经受瓷釉液高温,并且要耐侵蚀、不污染瓷釉使其着色。
能够作电极材料的有:钼、钨、铂和石墨等。根据国外及国内玻璃行业的情况,采用钼电极较多,使用也比较成功。钼电极在瓷釉中不着色,耐侵蚀。
1.熔制瓷釉电熔窑概述
起初瓷釉电熔窑仿效玻璃电熔窑的结构,结果都不成功。分析原因在于二者的熔制工艺有所不同。玻璃熔制要经过硅酸盐形成阶段、玻璃形成阶段、澄清阶段和均化阶段,而瓷釉的熔制仅有两个阶段,不需要澄清和均化,故此电熔窑结构应有所不同,只要三个区域即可。
瓷釉电熔窑的设计要求:
(1)计算出反应热及瓷釉带走的热量,保证有足够的熔融温度和尽可能长的置换时间。
(2)炉膛的体积及布局,电极的对数、位置等必须保证足够的熔化能力和流量。
(3)窑内温度分布均匀、稳定,出料正常。
(4)保证瓷釉的理化性能。
(5)炉壁和电极腐蚀率小,适当选用耐火材料及电极板材料。
(6)供电方式要便于电流电压的控制和尽可能小的电功率。
瓷釉电熔窑的优点:
(1)传统用燃料燃烧的方式熔融瓷釉,不但大量排出烟气,同时带走瓷釉中的挥发物,严重污染环境。冷顶电熔窑几乎为密封系统,可大大减少某些组分的挥发,而且排出的废气极少,也没有噪音。
(2)能实现瓷釉熔融自动化。电熔窑温度易控制、连续加料出瓷、实现自动化生产。
(3)热效率高。电熔窑热交换在窑体内进行,温度最高部位在电极附近,窑顶、侧壁、窑底温度较低。因而向周围介质散失的热量极少。根据计算,热效率为30~40%.
(4)可以获得稳定、均匀和高质量的瓷釉。
2. 熔制瓷釉电熔窑的设计和应用
(1)电熔窑的结构:该电熔窑的结构如图9.8.1。电熔窑中部温度控制在1300℃~1340℃,上部液面温度达1150℃~1200℃。池底温度为1100℃~1150℃。
在电熔窑的出料口处,利用低电压、大电流产生的热量,使瓷釉达到一定的出料粘度(相应温度为950℃~1000℃)后,从漏板中流出,漏板用来控制瓷釉出窑的速度。若电流大,电压高,则漏板温度高,瓷釉粘度小,瓷釉流出速度增加,反之瓷釉流出速度减小。通过调节电流和电压的大小,来控制瓷釉在窑内的置换系数,停留时间、温度等工艺参数。
加料系统由料仓、电磁振动加料机、加料口、铂针、信号放大器和控制仪组成,形成一个自动控制加料系统。
(2)电熔窑设计:电熔窑为深层熔化。电熔窑采用隔离变压器供电。一次电压采用可控硅恒温、恒压(或恒流)控制仪控制,变压器二次侧通过电极向熔体供电。某厂熔块耗电量为1.6~2.5Kwh/Kg。
用作电熔的电极材料种类较多,实践证明以钼为佳。经多年实践验证,它能保证瓷釉质量,成本较低,钼电极电流密度不宜超过1A/cm2。
某厂曾使用过板状和棒状两种钼电极。板状钼电极的表面电流密度分布较均匀,因而瓷釉中电流也分布较均匀,可避免瓷釉和电极板的局部过热。电极一般在窑体升温前按装,其缺点是,不能调节电极板之间距离。棒状电极,它可以在升温结束后插入,电极间距也可以调节,并可更换。但它表面电流密度不均匀,对瓷釉熔制不利。
电极的排列形式多种多样。该使用的是电极板从侧壁横向插入窑中,电流方向和窑长方向一致,电极对是平行的。实践证明,电流、温度的分布都比较合理。
(3)电熔窑与坩埚窑熔制瓷釉的性能比较。(a)实验证明,电熔窑熔制的瓷釉质量比较高,理化指标均达到国家规定标准,而且耐酸、耐碱比坩埚窑熔制的有显著提高(见表9.8.1)。经多次用原子吸收光谱作全分析,结果表明,电熔窑熔制的瓷釉化学成分非常稳定,与标准配方基本相同(见表9.8.2)。(b)节约能源。用坩埚窑熔化瓷釉1kg,使用柴油2.6kg,折合标准煤4.1kg;电熔窑熔化1kg,用电2.5度,折合标准煤1kg,因而比柴油熔化瓷釉节约能源3倍。
表9.8.1 耐酸耐碱性能的比较 (单位:mg/cm2)
项目 |
耐酸 |
耐碱 |
坩埚窑 |
0.12-0.15 |
0.2-0.25 |
电熔窑 |
0.06-0.08 |
0.16-0.2 |
表9.8.2 瓷釉全分析情况比较
组分 |
SiO2 |
Al2O3 |
Na2O |
K2O |
B2O3 |
ZrO2 |
TiO2 |
MnO2 |
CoO |
CaO | |
配方 |
65 |
1.6 |
19.1 |
0.84 |
2.4 |
1 |
4.5 |
1.5 |
1 |
1.2 | |
分 析 次 数 |
1 |
65.2 |
2.3 |
21 |
0.7 |
2.7 |
0.8 |
4.5 |
1.5 |
1 |
1.4 |
2 |
63.9 |
2.3 |
20.6 |
0.8 |
2.5 |
0.9 |
4.5 |
1.4 |
1 |
1.1 | |
3 |
64.7 |
2.6 |
20.2 |
0.7 |
2.7 |
0.9 |
4.3 |
1.9 |
1.1 |
1.1 | |
4 |
64.3 |
1.5 |
20.5 |
0.6 |
2.7 |
0.9 |
4.3 |
1.8 |
1.1 |
1.1 | |
5 |
64.5 |
1.6 |
20.4 |
0.5 |
2.7 |
0.9 |
4.3 |
1.7 |
1.1 |
0.8 |
(4)存在问题:(a)耐火材料的腐蚀十分严重。某厂使用过粘土砖、刚玉砖、镁砖、高铝砖等,除高铝砖的窑龄在60天左右外,其余均在30~40天。(b)热电偶保护管的腐蚀问题。刚玉管既不耐腐蚀,又不耐热冲击。钢管虽耐热冲击,但不耐腐蚀,仅作定期测温用。
例1 日产1~1.5T钛白粉搪瓷瓷釉电熔窑
某厂生产2-2钛白粉搪瓷瓷釉电熔窑由配电、控制、变压器、窑体、加料机、出瓷车等组成。熔化池面积0.3m2,日熔化瓷釉量1~1.5T/d。
该厂初次试验时采用钼电极。采用循环水冷却,保证电极引出位置温度不高于600℃。由于钼电极价格高、加工焊接难度大、制作不锈钢冷却水套技术条件要求高,作为小型电熔窑若采用冷却系统就增加了热损失。为此,该厂又选用石墨做电极熔制搪瓷釉,结果石墨没使瓷釉着色。为了降低电耗,加强了保温,取消了水冷却系统,减少了电极数量,在流液洞不设铺助电极,扩大流液洞宽度,保持出料口的温度不降低。
三相交流电380V供电,变压器容量50~80KVA,二次电压50/100V两档,可控硅调节,供电系统如图9.8.2。平均电耗1400Kwh,单耗1.3Kwh/Kg瓷釉,连续加料,连续出料。
釉料品种2—2#钛白粉,用于小面盆、汤盆、口杯等搪瓷产品。物理化学指标全部达到或超过国家及部颁标准。
1.自控系统
(1)恒温自控 :采用XCT—191动圈式温度指示调节仪,用铂—铑铂热电偶作检测元件,插入电熔窑靠出料口位置。热电偶产生的直流电势信号输入XCT—191仪表,再控制ZK—1可控硅电压调整器,达到恒温自控。
(2) 恒流自控 :利用瓷釉电阻率与温度的关系曲线,在配方一定、电熔窑尺寸一定的情况下,控制电极的电流即能控制窑炉的温度。根据瓷釉的导电特性,使其二次电流恒定,达到恒温的目的。恒流在可控硅交流调压装置中较易实现,而且灵敏度高、稳定性好。如图9.8.3
(3)液面控制:采用螺旋推进器作加料机,以出料来控制加料。采用电子液面控制器控制加料速度,使之稳定液面、稳定加料及出料速度。加料速度控制框图如图9.8.4。
2.设计参数
经过实测和计算,该厂瓷釉工艺的两个温度1100℃时导电率为4Ω·cm,1250℃时导电率为3.5Ω·cm。瓷釉平均电阻率ρ=RS/KL(Ω·cm) 式中R—瓷釉的电阻(Ω); S—瓷釉导电截面积(cm2);K—经验系数,钼电极取1.3,石墨电极取1.2;L—电极间距离(cm)。
3.面盆、口杯电熔釉与坩埚釉产品理化指标对比见表9.8.3和表9.8.4
表9.8.3 面盆电熔釉与坩埚釉产品理化指标对比
指标 |
实 测 |
国标GB2629-81 | |
电瓷釉 |
坩埚釉 | ||
白度 |
82.2 |
91 |
不低于72% |
光泽 |
106.3 |
98 |
不低于95% |
密着 |
合格 |
合格 |
不得呈块状 |
耐碱 |
合格 |
合格 |
不失原有光泽 |
表9.8.4 口杯电熔釉与坩埚釉产品理化指标对比
指 标 |
实 测 |
国标GB2632-81 | |
电熔釉 |
坩埚釉 | ||
密着性能 |
丝状 |
丝状 |
不得呈块状 |
耐热骤变 |
不裂 |
不裂 |
232℃激冷水20℃不得掉瓷 |
耐酸 |
0.098 |
0.1 |
侵蚀量≤0.2mg/ml |
含锑 |
无 |
无 |
Sb≤0.7mg/l |
含铅 |
无 |
无 |
Pb≤1.0mg/l |
含镉 |
Cd≤0.5mg/l |
4.电熔窑与火焰窑的能耗对比
表9.8.5 电熔窑与火焰窑的能耗对比
项目 |
电熔窑 |
煤坩埚窑 |
柴油池窑 |
煤气池窑 |
单耗 |
1.3Kwh/Kg瓷釉 |
2Kg煤/Kg瓷釉 |
0.5 Kg油/Kg瓷釉 |
1.8m3/Kg瓷釉 |
折算标煤 Kg |
0.58 |
1.7 |
0.706 |
0.972 |
例2 熔制搪玻璃底釉和面釉的电熔窑
某厂是生产搪玻璃釉的专业厂,采用电熔窑熔制搪玻璃底釉和面釉,产品供应搪玻璃设备生产厂。
1.电熔窑的基本结构
电熔窑分熔化区和澄清区,熔化区有三组板状电极组成,使配合料熔化、生成硅酸盐熔体,然后熔体流入澄清区完成玻璃体均化作用,达到熔制目的。澄清区有两组板状电极。
配合料从熔化区第一对电极中间加入,玻璃体从澄清区流出,全过程是连续进行的。根据配合料及熔体性质以控制电极板间的电压、电流,就可以控制电熔窑内各部分熔制工艺所要求的温度、物料的熔化速度和出料速度。每小时电耗约50Kw,每小时产量为20—25Kg搪玻璃熔块。用可控硅控制变压器调整电极间的电压与电流。
电熔窑池墙砖采用锆刚玉质,经三个月连续生产到拆窑,腐蚀形状如图9.8.5(熔化区)和图9.8.6(澄清区)所示。实线为腐蚀后的形状,虚线为腐蚀前的现状。
经过测算,熔化区****腐蚀速度1.2mm/d,平均腐蚀速度为0.8mm/d,澄清区平均腐蚀速度为0.23mm/d,平均每日腐蚀砖重1.06Kg,日产量为400Kg,则釉料中Al2O3增加0.16%,SiO2增加0.09%。配方中SiO2理论值为65%,实测为64.75%、64.27%、65.02%。就是说,耐火材料成份引入搪玻璃熔块中的量是不大的,对搪玻璃釉的性能是没有影响的。
2.熔制工艺的稳定性
表9.8.6火焰池窑和全电熔窑对易挥发物质挥发量的对比图
氟化物 |
氧化铅 |
氧化硼 |
氧化硒/氧化镉 | |
火焰池窑% |
55 |
8 |
7 |
90 |
全电熔窑% |
1 |
0.5 |
1 |
0.5 |
图9.8.7 在不同气氛下,搪玻璃釉的红外线透过率
由于“料毯”的作用,一些易挥发物质的挥发量显著减少。表9.8.6为火焰池窑和电熔窑对易挥发物质挥发量的对比。电熔窑不仅保证了搪玻璃配方的稳定性,而且也减少了环境污染。从表中看出,火焰窑中氟的挥发量高达55%,硼的挥发量为7%,而电熔窑中氟、硼的挥发量则为1%。
电熔窑中含有最低量的氢氧根离子(搪玻璃釉中的氢氧根离子是产生瓷层缺陷的根源之一),这是由于在电极间存在直流分量,氢氧根离子在电极附近进行氧化还原反应,(即不断得、失电子)而形成气体,由熔融液相中析出,从而降低了玻璃液相中氢氧根离子的浓度。氢氧根离子浓度的降低,实际上减少了搪玻璃釉的碱度。由于釉浆中碱度降低,干燥粉层透气性增加,烧成过程的胀裂现象降低,釉面色泽一致,减少了花脸现象及爆瓷。图9.8.7为在不同窑炉气氛下,搪玻璃釉的红外线透过率,曲线1为电熔窑熔化,曲线2为一般电熔窑熔化,曲线3为燃油、燃气窑熔化。从曲线可看出,电熔窑熔化的搪玻璃釉的质量最为稳定。
3.电熔窑的其它优点:
电熔窑是自动控制,工人劳动强度低,生产条件优越,只要不经常停电就能做到均衡生产。图9.8.8为电熔窑内的温度曲线。实线为正常生产时熔化区电极间截面温度分布。虚线为停电一小时后熔化区电极间截面温度分布。
此页网址为:
相关文章