工程分类
更多>>![]() |
|
![]() |
|
![]() |
|
![]() |
|
![]() |
|
![]() |
|
![]() |
|
![]() |
|
![]() |
|
![]() |
|
![]() |
|
![]() |
|
![]() |
|
![]() |
|
![]() |
|
![]() |
|
![]() |
|
![]() |
|
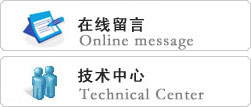
联系人:
电话:0511-88791451
手机:13951280541
邮箱:jfchen@ujs.edu.cn
地址:镇江市学府路80号
最新文章
您的位置:网站首页 > 最新文章供料道的电加热——用板状钼电极的电加热
1.板状与棒状钼电极加热供料道的比较
板状钼电极同棒状钼电极相比固然有许多优点,如受热面积大,加热较均匀,且板状钼电极无需用水冷却。但它仍存在局限性,较为突出的一点是应变性能差。当发生生产事故时,板状钼电极易暴露在空气中,因氧化而烧损掉。重新调换电极,须停产数日,严重影响生产。更为严重的是,若玻璃池窑中仅有一条供料道,就无法调换。因为闸断供料道内玻璃液流时,流液洞会发生堵塞。目前,在玻璃瓶罐生产中,棒状钼电极使用是很普遍的。增加棒电极的排列密度即增加电极对数来改善对玻璃供料道的加热程度。
如图16.3.1由于板状钼电极的电极板可镶嵌到供料道侧墙耐火材料中去,所以加热距离大,可以消除供料道两侧玻璃液与中心玻璃液的温差。同时电极板面与玻璃液接触面积大,电场分布均匀,电流密度小,其加热范围广,加热均匀,能很好地满足提高玻璃液热均匀性和热稳定性这两项重要的工艺要求。所以若从增强加热效果、提高玻璃液热均匀性和节省投资考虑,应全部使用板状钼电极。 2.板状电极的作用区域 对于供料道长度在2m以上的电加热供料道,设置一对电极是不够的。应放置多少对电极既能保证加热要求又能降低投资费用,即确定电极与电极之间的距离多长才合理,解决这个问题的实质就是找出一对电极的****作用区域以及电力线分布规律。 在供料道的设计过程中,单纯从加热的角度出发,电极对数多一些较好,这样加热区可以更加均匀些,电力线更趋向线性化,避免波浪式加热。但通过实践,电极对数过多,不仅投资大造成不必要的浪费,而且过多的电极在供料道结构上难以保证,同时也达不到预计的加热效果。供料道中多对电极之间的中心距离应选取在4-5倍的电极板宽的范围内。 3.变压器电工参数的确定由于初级回路中串有可控硅调压,变压器一次侧电压V1约340伏。变压器二次侧电压VN与供料道的分配功率PN有关,并且还与单条供料道变压器的台数有关,对于单台变压器三对电极的供料道其分配功率见图16.3.2。靠料盆处功率比例****占40%,即PI=0.4P。PⅡ=PⅢ=0.3P P=PⅠ+PⅡ+ PⅢ 因PⅡ=PⅢ,使用中可将其并联作为二次侧V2电压。考虑操作安全V2、V3≤65伏 为宜。 |
|
4.板状钼电极的启动与保护
板状钼电极容易氧化,不易安装的缺点限制了它的使用。由其T形结构特点决定了这种电极必须采用冷装方式。为了防止电板在烤窑过程中被氧化,对电极必须采取一系列的防护措施,诸如(1)用玻璃纤维布将电极包裹住。(2)在供料道内用碎玻璃复盖住,在烤窑过程中避免受火焰长时间的烘烤,必须保证在短时间内将玻璃液引过来,将电极全部浸没,只有这样才能保证电极不被氧化。供料道钼电极的保护应引起足够的重视。倘若处理得不好,电加热将无法使用,给生产带来不应有的损失。因此供料道电极保护是电加热技术关键之一。
电极孔砖用一枚粘土砖钻一直径为41mm的孔(配φ40mm刚玉管)。开孔位置既要符合供料道电极定位尺寸,又要保证电极板上沿低于料液面3-5cm。砌筑时,将电极孔挪后4 cm,留出凹槽(即为附壁式结构),可减少液流冲刷和阻力。
然后把处理过的钼电极放入电极孔中。放下后闸板砖,把供料道与工作池隔开,并封好料盆口。把捣碎的玻璃加入供料道和料盆,投到略高于料液面处为止,最后砌筑盖板砖。
当工作池料液接近液面线时(在放料前约10h),点燃柴油喷咀对供料道内的碎玻璃快速加温,使其熔化,同时根据下降的程度不断地补充碎玻璃,防止玻璃液下方的钼电极暴露在玻璃液外而氧化。当工作池玻璃液加至液面线时,先抽去后闸板,与工作池玻璃液接上。然后疏通料盆口开始放料并准备生产。此时电加热可通电工作,开始因温度不高,电流较小。温度上去后,电流趋于正常,再把恒流控制仪(HLK—2)调整到自动恒温控制,系统进入双闭环控制,电加热投入运行。
尽管如此,还不时发生因引料过慢而导致电极被氧化的事故发生。即使在安装时没被氧化。在生产过程中有时因供料道内玻璃液面下降太大也会被氧化。损坏后更换困难。
5.影响板状钼电极使用寿命的因素
供料道中板状钼电极的使用寿命,一般取决于电极的电流密度、玻璃液的流速和粘度、玻璃的化学组成。电流密度愈大,玻璃液流速愈快,粘度愈小,电极寿命愈短。为使钼电极有较长的寿命,必须对下列若干化学组份作如下规定:As2o3<0.1%, Sb2O30.4%, Fe2O3<1.5%, CuO<0.5%, Cr2O3、 MnO、CoO、F<1% 。
在使用钼电极加热时,有时发现玻璃液中带有小泡,这可能来自两方面的原因:①板状钼电极表面的电流密度过大;②玻璃料方中的组份超出上述规定。
当玻璃池窑放料后,取出钼电极时在钼板表面还能见到发泡现象,这主要是由于MoO5的蒸发引起的。
例1 生产药用小瓶的板状钼电极加热供料道
某厂主要产品是药用小瓶,由于产品的重量较轻(一般在50g-60g之间)、料滴小,故玻璃的成型温度要求较高约为1220-1230℃。在该供料道采用钼电极加热,料温稳定,料性均匀,调节方便,运行可靠,维护简单,环境干净,无噪声及节能。
1.供料道主要电工参数的计算
(1)数据准备:①根据池窑设计得出供料道平均出料量:9t/d;②玻璃液进入供料道温, , , , , , , , , , , , , , , , , , , , , , , , , , , , , , , , , , , , , , , , , , , 度1250℃(通过池底热电偶测出);③玻璃成型温度为1230℃(通过光学高温计直接测得);④钼电极板的几何尺寸:200×100×6mm。(根据生产单位的定型产品确定)。
(2)主要参数的计算:①求出玻璃液从1250℃降至1230℃所放出的热量,取供料道玻璃液平均温度。t均=1240℃,查有关资料得玻璃液的比热:C=0.1605+2×10-4×t=0.4085kcal/kg.0c,故玻璃液放出的热量Q1=m.c.△t=×0.4085×(1250-1230)=51.06(kcal/min)或3.5kw/hr。②供料道外壁的热损失量Q2。根据对供料道的热平衡数据可得供料道外壁的热损失为11.5kw/hr;③若考虑这两方面的热量损失,那么就需补充电功率为Q电= Q2- Q1=11.5-3.5=8 kw/hr,若以电的利用率为90%并考虑留有一定的余量,故选用电功率为10 kw。④电工参数:该厂玻璃的成分为:Na2O 15%、温度T=1513K, 根据钠、钙、硅玻璃电阻率计算公式可知该厂玻璃的电阻率r=5.025W.cm。玻璃液的电阻R=k.r.
。式中K=1;L=40;S=b.h;b为供料道导电区的有效宽度为30cm。h为玻璃液导电区的有效深度为20cm。
设计三对电极进行加温,则加在每对电极上的功率为3.3Kw。故此电极板上的电流强度:I=99A;U=34V;电极板上的电流密度为0.49A/cm2
2.钼电极的安装工艺
考虑到钼电极在600℃时,极易被氧化而损坏,在电极板上缠上玻璃纤维,铺上粒度较细的碎玻璃将电极板复盖严密,电极板全部沉浸在玻璃液中以隔绝空气,并在电极引出部分严格隔绝空气。电极板安装在凿有凹槽的供料道上,防止由于玻璃液的流动造成对电极板的磨损,延长电极板的使用寿命。
3.使用电加热供料道前后的技术经济分析 (1)节约能源:在供料道未采用电加热以前,根据热平衡测定其孔口溢流热散失比较大,占总热耗的9.11%;而采用了钼电极加热后,经测定其热损失只占总热耗的3%。 (2)提高了产品的质量;通过采用电加热,供料道玻璃液温度波动明显减少;如图16.3.3可知在未使用电加热时,其供料道玻璃液的****温差为38℃,而使用供料道电加热后其****温差仅为10℃。 采用电加热前后瓶重****误差的变化如表16.3.1。 |
![]() |
表16.3.1 瓶重****相差值G
供料道型式 |
品种 |
每隔一小时取样的平均数(g) |
G | ||||||
火焰加热 |
63cc瓶 |
90.0 |
88.7 |
94.0 |
86.0 |
97.5 |
86.0 |
81.0 |
16.5g |
电加热 |
心脉灵瓶 |
97.5 |
100.0 |
100.0 |
97.0 |
98.0 |
96.0 |
98.0 |
4.0g |
从表16.3.1中数据可知,使用钼电极加热后,瓶重的****偏差值从以前的16.5g降至4g,从而提高了产品的质量和产量。
(3)由于采用了供料道的电加热,使窑压从原来的3mmH2O柱降至现有的1-1.5 mmH2O柱,从而延长了窑炉的使用寿命。
(4)采用了电加热,克服了以前供料道正压过大的缺陷,避免了由于火焰较长而造成工作环境恶劣,供料机寿命降低,及冲头、转筒易被烧坏等缺点,从而缩短了停机时间,提高了生产率。
例2 生产茶色啤酒瓶的板状钼电极加热供料道
某厂生产茶色料啤酒瓶的供料道采用钼电极加热,经过半年多的实践,供料道料温稳定、料性均匀、调节方便、运行可靠、维护简单、环境干净、无噪声以及省电。
1.基本情况介绍
采用钼作电极的电加热供料道在生产茶色啤酒瓶的9、11、12号机的供料道投入实际生产使用。采用钼电极加热具有如下特点:①使用寿命长,不需特殊维护,实际使用的电流密度为0.5 A/cm2,采用6m/m厚的板状钼电极,寿命达1-2年。②电加热装置简单,电极引出部分以自然风冷却,不加水冷装置。隔离变压器的次级电压不超过60V,电极对地电压不超过80V,实测是17-25V之间,对人身是安全的。控制系统是以可控硅调压,元件参数选择合适、平时很少出故障。运行半年多,除了个别可控硅击穿、恒流仪触发信号不平衡而造成过电流、断保险丝的现象外,其他毛病很少,无需专人维护。③热效率高、省电、节约能耗。比用硅碳棒的辐射式电加热供料道要省电一半以上。表16.3.2是实际使用中测定的数据, 从表16.3.2中看出每条供料道实际消耗的总功率在11.19-13.11KW之间,比用硅碳棒加热供料道耗电28-40KW少了一半以上。
表16.3.2
机台 |
前区 |
后区 |
总功率 KW | ||||
电流A |
电压V |
功率KW |
电流A |
电压V |
功率KW | ||
9号机 |
70 |
100 |
88 |
150 |
55 |
8.25 |
11.19 |
11号机 |
42 |
29 |
49 |
200 |
45 |
9 |
11.9 |
12号机 |
2.94 |
2.9 |
4.312 |
166 |
55 |
8.798 |
13.11 |
④调节性能好,料温稳定:电加热供料道控制系统装有HLK-1型恒流控制仪,作为交流调压的恒流控制装置,使供料道的温度稳定在一定范围内。此外由于电流是沿玻璃液内部横向通过供料道而在玻璃液中产生热量的,故玻璃液的上下层温度较为均匀,料性变好,这点是制瓶工艺方面尤其是双滴料,多滴料特别需要的所谓“料性均匀”的特点,这在烧油或其他形式的表面加热供料道都难以具备的。所以有的烧气体燃料较好的供料道,调节段下部还装有电加热电极,目的在于使玻璃液温度均匀以提高料性。⑤电加热代替烧油,调节方便无噪声。供料道烧重油、原油或柴油时,除正常情况下温度均匀性不如电加热外,还经常出现喷咀堵塞,直接影响火焰,油温油压变化时火焰也受影响。烧油多为手工调节火焰,烧油系统难免会滴漏,使供料机周围油迹斑斑,烟雾滚滚,而且噪声又大,环境污染极大。而使用电加热就没有这些现象了。
2.供料道电加热与工艺配合
供料道的电加热必须与工艺密切配合才能收到好的效果。电加热供料道的发热量是有一定限度的,当电极的几何尺寸、数量、变压器总容量确定,****的发热量也就确定了。如果进入供料道玻璃液本身温度过低,仅仅靠电加热来补充是不可能的。如果玻璃液温度过高,用电加热只能升温而不能降温,因此必须采取其它措施来调节。某厂三条供料道几个参数的计算是①比热的确定:玻璃液的比热是随温度变化的,0-1200℃时玻璃液的比热变化如表16.3.3。供料道温度一般在1020-1070℃之间,因此按C=0.1605+1.1×10-1t式计算。热电偶实测出9、11、12号机的供料道温度分别为1070℃、1040℃和1040℃。因此它们的比热如表16.3.4。②电加热供料道每分钟发热量计算:按Q=0.24Iut,Q=0.24pt计算如表16.3.4。③每分钟流过供料道的玻璃液的量(出料量=机速×瓶重)即如表16.3.4。④电加热升温计算: 略去热损失,按电热转换计算,利用公式:Q=C.M.△t ,如表16.3.4。按上面计算的各种数据综合如表16.3.4。
表16.3.3
温度范围 |
比热算式 |
0-550℃ |
C=0.1792+0.632×10-4t |
550-750 |
C=0.1698+0.866×10-4t |
750-1200 |
C=0.1605+01.1×10-4t |
1200以上 |
C=0.1605+2×10-4t |
表16.3.4
机台 编号 |
机速 个/分 |
瓶重 Kg/个 |
供料道温度 ℃ |
比热 Kcal/Kg℃ |
出料量 Kg/min |
补充热量 Kcal/min |
升高温度 ℃ |
9 |
37 |
0.54 |
1070 |
0.2782 |
19.98 |
161.14 |
28.99 |
11 |
29 |
0.54 |
1040 |
0.2749 |
15.66 |
171.36 |
39.8 |
12 |
30 |
0.54. |
1040 |
0.2749 |
16.20 |
188.18 |
42.39 |
由表可见,在正常情况下三条供料道电加热升温的理论计算值与热电偶测定的基本接近,12号机消耗电功率较大,升温也较高,如果再调大电流则可升高到50℃,但再大就不可能了。因此在有限能量的情况下必须合理调整供料道本身的温度,然后再经过电加热调节,才能得到好的效果。所以必须做好如下几点:①由池窑流过来的玻璃液温度最好不要超出±25℃,波动太大电加热供料道无能为力,波动范围大则应增加电极对数和变压器容量,以提高加热功率。②供料道需设有闸板(挡砖)以防池窑火焰的影响。调整闸板开度可直接调整供料道冷却段的温度,冷却段的温度要比料滴温度低10-20℃,然后再由装在调节段的电加热升温到需要的成型温度。③供料道外侧必须有良好的保温,特别是调节段要加强保温以减少热损失,充分利用热能提高调节效力。④电流密度必须适当控制,密度过大易损耗电极并可能出现气泡,一般控制在0.5A/cm2以下。
3.供料道电加热设备 ①板状钼电极:主要由电极板、弯柄、螺铨、螺母以及护套等组成,除护套以外其它全用钼材料加工而成,其结构如图16.3.4所示。 ②电极在供料道中布置如图16.3.5。 电极埋设在供料道两侧玻璃液中,为防止玻璃液面波动时电极露在空气中,稍偏低中心线。如图16.3.5。 |
![]() |
③电气控制主线路如图16.3.7。变压器为单相15KVA ( 380/2×60V),输入电压为380V,输出 0-60V×2。恒流器HLK-1型。可控硅3CT-50A/1200V。
4.电加热供料道在实际应用中注意事项:
①隔绝池窑窑体升温时对供料道的影响,在供料道里设两道闸板将窑炉火焰隔绝,电极部位的温度不超出300-400℃,如发现温度太高马上吹冷却风降温以免电极损坏。 ②钼电极装好之后,在电极板、弯柄等暴露在空气中的部位包上8-10层玻璃纤维布,并逐层涂上水玻璃(硅酸钠),作为升温过程的过渡性保护。当高温玻璃液浸泡之后,玻璃纤维布和水玻璃均熔化分解了。 ③ 钼电极升温前先复盖碎玻璃(碎玻璃的大小与米粒相近),目的在于减少池窑过来的火焰对电极的影响,便于碎玻璃熔化形成保护层。同时对复盖于电极上部的碎玻璃快速加温,使碎玻璃熔化形成复盖面,当整条供料道玻璃液畅通后温度达1000℃时即可通电,并逐渐调节。 ④升温后放玻璃液要迅速,当供料道准备放料时,先将料盆中冲头放下、堵塞住滴料口(以防放料太快液面降低而露出电极)。 ⑤在正常生产中要注意玻璃组成的氧化物对电极的侵蚀,某些澄清剂如SO2-4、As2O 3等对电极侵蚀尤其明显,不过这些成份一般在熔化部的作用比较强烈、而在供料道中只有少量的游离SO2-4或As2O 3的氧化物成份。某厂的玻璃配方有0.56% Na2SO4,但在供料道玻璃分析中只偶然一次发现有少量游离状态的SO-4,因此没有发现对电极严重侵蚀的现象。 |
![]() |
5.存在的问题
①从某厂三对电极的电加热供料道运行情况来看,当窑炉温度正常,即波动不超过±20℃时。电加热恒流系统有能力调节,但波动较大就无能为力了,所以如能增加多对电极、增大调整能力对稳定温度更有好处。
②自动调节系统单靠恒流器调整可控硅,恒温性能有局限性。能再增加温度反馈系统,通过PID调节器控制可控硅,这样由电流信号及温度信号同时反馈的双闭环系统,估计恒流性能会更好些。
③一但板状电极损坏则难以更换(必须停产将供料道堵住放料才能更换),如改为圆形棒状电极,由供料道两旁插入,更换或维修就容易得多了。
例3 生产棕色啤酒瓶的板状钼电极加热供料道
池窑窑型为马蹄焰池窑,无工作池,烧油,熔化面积30m2,出料量45t/d,熔化部火焰辐射温度1580±20℃。
供料道玻璃液温度1200-1250℃,料滴温度通常为1140±10℃。采用钼电极加热代替柴油加热,使玻璃液上下温度差大大缩小,玻璃温度均匀性大大提高,电极配用恒温自动控制装置,玻璃料滴温度稳定,改善了玻璃制品的成型质量,提高了制品的合格率。
1.玻璃组成
应用钼电极的池窑生产硫碳着色的棕色啤酒瓶、农药瓶。玻璃组成如表16.3.5。用于玻璃着色和澄清的添加剂用量为煤粉约 0.22%、(NH4)Al(SO4)2 0.2%、NaCl 0.16%。
表16.3.5
氧化物 |
SiO2 |
Al2O3 |
CaO |
MgO |
K2O |
Na2O |
Fe2O3 |
其它 |
合计 |
组成% |
69.60 |
4.64 |
8.30 |
3.0 |
1.56 |
12.45 |
0.27 |
0.18 |
100 |
2.电极
钼电极板的设计尺寸为100×200mm2、厚度5mm,钼棒截面为16×16mm2,钼板与弯曲的钼棒用φ8mm钼螺丝固定。钼的化学组成见表16.3.6。
表16.3.6 钼板和钼棒试样的光谱分析与Mo含量
元素 |
Mo |
Fe |
Al |
Ca |
Si |
Zr |
Ni |
V |
Mg |
Cu |
C |
W |
P |
O2 |
Co |
Sr |
钼板含量% |
99.6 |
0.00001 |
0.00001 |
0.00001 |
0.1 |
0.1 |
0.1 |
0.1 |
0.1 |
0.01 | ||||||
钼棒含量% |
99.8 |
0.006 |
0.002 |
0.002 |
0.003 |
0.003 |
0.002 |
0.02 |
0.10 |
0.1 |
0.003 |
3.钼板试样侵蚀结果
钼板的原设计(侵蚀前)尺寸长×宽为:200×100mm2,经玻璃液侵蚀,电极板外形尺寸基本不变,电极板上部两角局部被氧化,不属玻璃侵蚀,而是炉子冷修放料时由于暴露于空气氧化所致。中下部因随放料温度下降,玻璃粘度增大,未暴露而完整保留。 选择上角氧化较为轻微的钼板,测量各个部位的厚度(图16.3.8),与应用前测定厚度进行比较见表16.3.7。 |
![]() |
电极经还原性配合料玻璃长期高温侵蚀后表面呈现现黑色,内部局部出现灰褐色。与钼板连接的钼棒原规格尺寸为16×16mm2、侵蚀的情况主要是菱角稍为变钝,基本尺寸变化不大。钼棒中段不锈钢保护管内端离钼板距离约50-60mm,接触的玻璃温度较低,侵蚀不明显,钼棒外端保持原状。钼电极是脆性金属材料,在黄料玻璃液中高温1200-1250℃长期侵蚀后材料强度经落地冲击试验,脆性并未显著变化。
表16.3.7
位置 |
1 |
2 |
3 |
4 |
5 |
6 |
7 |
8 |
9 |
10 |
平均 |
原钼板厚度mm |
5.8 |
5.7 |
6.1 |
6.2 |
5.9 |
5.9 |
6.0 |
5.9 |
5.9 |
6.0 |
5.94 |
侵蚀后的钼板厚度mm |
5.5 |
5.4 |
5.0 |
5.3 |
5.2 |
5.3 |
5.3 |
5.5 |
5.1 |
5.3 |
5.29 |
4.电工参数
两对钼电极并联连接,电极距离450mm、纵向间隔中心距550mm,通过电极的总电流0-180A,电极电压为0-60V,电极之间玻璃液总电阻约0.36-0.4Ω,电极使用周期三年,与窑龄同步。
5.使用效果
(1)钼电极在硫炭着色的黄料玻璃供料道中的侵蚀速度较慢。
(2)尺寸为200×100×5mm、负载功率为0-9KW的板状钼电极在黄料玻璃中的侵蚀情况来看,增大负载功率和增加电流密度是可行的。
(3)在黄料玻璃供料道中使用的板状钼电极其结构可以简化。由于钼棒和钼板联接处侵蚀较少,因此可以考虑不必打弯头连接,钼棒头部可直接加工成螺纹用钼螺帽与钼板固定。钼棒的尺寸也可以缩小,离钼板6-7cm外的钼棒可以考虑用不锈钢管代替,节省钼棒材料,但焊接必须牢固、并保持原有的保护结构。
例4 制瓶厂板状钼电极加热供料道的应用情况
供料道砖采用绝缘性能良好的合成莫来石和硅线石。钼板设计尺寸可取250×100×7mm,每组电极之间距以800-900 mm为宜。在电气设计中,要有接地装置,否则供料机剪刀在剪料时,会引起放电,加速剪刀的损坏。
钠钙硅玻璃中的高钙玻璃,一般易于产生析晶现象。这是由于落料温度十分接近析晶温度区域所致。因此,保持温度稳定很重要。若在供料道中完全依靠电加热来控制玻璃液温度,析晶问题尤其突出。电加热电极置于玻璃液中,上层空间无加热手段,玻璃液中部温度较高,上层温度较低。料盆中若没有加热措施,在均料筒四周易析晶。特别是深料盆结构,更要引起重视。较理想的办法是在供料道中同时采用煤气和电两种加热措施。这样,能更正确地控制玻璃液温度,防止玻璃液表面析晶。
例5 供料道电加热技术的试验与应用
某厂在一座10m2燃油池窑的供料道上应用埋入式无水冷板状钼电极加热技术,效果良好。
1.产品料别与玻璃成分:见表16.3.8。
表16.3.8
产品料别 |
供料道流量 (T/d) |
玻 璃 组 成 (%) | ||||||
SiO2 |
AlO3 |
CaO |
MgO |
R2O |
B2O3 |
澄清剂 | ||
大口保温瓶(青白料) |
7.5 |
74.72 |
2.12 |
4.56 |
2.27 |
15.78 |
/ |
Sb2O3<.3% |
500ml盐水瓶中性料 |
8.3 |
74.39 |
4.47 |
5.59 |
微 |
12.73 |
2.2 |
Sb2O3<.3% |
2.电极结构:考虑易于排除耐火材料等异物,采取埋入式无水冷T型板状钼电极,并联连接,以附壁式安装,电力线与玻璃液流方向垂直。这样布置,加热面积大,加热效果明显,横向、垂直温差较小,有利于供料道内玻璃液温度分布趋向合理。 3.供料道结构、温度的调节和控制:仍保持原C型供料道的结构,仅供料道宽度、深度与空间高度的尺寸作了适应于柴油加热与电加热两种方式的考虑。采取比较简单的恒流控制方式,使用HLK—1型恒流控制仪。供料道结构、电极布置和控制方式见图16.3.9。 |
![]() |
4.耗电情况:见表16.3.9。
表16.3.9
产品 |
出料量(kg/h) |
料滴温度℃ |
平均电耗(Kwh/h) |
吨玻璃液 耗电(Kwh) |
4磅大口瓶内胆 |
2312.5 |
1140 |
6-8 |
19.2-25.6 |
500ml盐水瓶 |
345.8 |
1190 |
8-10 |
23~28.9 |
5.有关工艺参数:见表16.3.10。
表16.3.10
序号 |
名称 |
单位 |
指 标 |
1 |
工作池面积 |
m2 |
1.36 |
2 |
工作池池深 |
m |
0.6 |
3 |
火焰分隔情况 |
供料道与工作池全分隔 | |
4 |
供料道宽 |
mm |
500 |
5 |
供料道玻璃液深 |
mm |
160 |
6 |
供料道空间高度 |
mm |
255 |
7 |
产品 |
4磅大口瓶、500ml盐水瓶 | |
8 |
料滴温度 |
℃ |
1144(4磅大口瓶), 1190(500ml盐水瓶) |
9 |
成型设备:BB-12吹泡机一台,供料机机速, 内胆为13只/分钟(4磅大口瓶)。手工机两台、 供料机机速为17只/分钟(500ml盐水瓶) | ||
10 |
供料道玻璃液电阻 |
Ω |
实测为0.368欧姆(4磅大口瓶)。 |
未测(500ml盐水瓶) |
6.试验材料设备:见表16.3.11。
表16.3.11
序号 |
材料设备名称 |
规格型号 |
数量 |
1 |
钼板 |
厚5mm |
2.5kg |
2 |
钼棒 |
φ22mm |
12.5kg |
3 |
变压器 |
22KVA 380V/80V 220A |
1台 |
4 |
不锈钢管 |
φ38 mm、壁厚3 mm、长度220mm |
4根 |
7.使用效果
(1)埋入式无水冷钼电极加热供料道较好地解决了供料道内玻璃液温度的均匀性和稳定性这两个技术关键,提高了料滴质量,料形稳定,料重变化小。瓶子的光洁度好,瓶壁厚薄均匀,大口保温瓶瓶坯合格率提高8-10%,其外观质量和内在质量亦有显著提高。
(2)料滴温度调节方便、平稳、灵敏。在池窑熔制工艺参数(温度、压力、液面)稳定的情况下,电加热的温度一般保持不变,无需经常调节,甚至在一个班生产时间里不去调节。即使需要调节温度也很方便,只要调整电极两端的电压,在十分钟左右时间内就可见效,非常灵敏。
(3)泥筒使用周期提高了一倍,料盆使用12个月仍未更换,使用寿命也延长了,节省了因更换而造成的停产时间。
8.技术经济分析
①能源使用合理,节能效果明显。
埋入式电加热供料道的玻璃液,没有燃烧产物(废气)排出,热利用率高。以生产大口瓶瓶坯为例,平均电耗每小时7Kw(按等价热量3000Kcal/ Kw.h, 折算合21000Kcal);而用柴油加热,热效率低,平均油耗5Kg/h(按等价热量11000Kcal/Kg,折算合55000Kcal)。因此,电加热供料道比油加热供料道节约能源消耗约一倍。能源使用合理。
生产大口瓶瓶坯的供料道用柴油, 燃烧加热玻璃液,需要雾化介质—压缩空气,按平均油耗5Kg/h计算,每分钟约耗压缩空气1m3,雾化空气所需风冷空压机动力消耗7.5 Kw,这与电加热的电耗相抵消,则不需增加耗电指标,又节省了柴油,节能效果是明显的。
②由于一条大口瓶供料道电加热一年可节约柴油43.8T。这样也就可节约能源费用17958元,降低了生产成本,增加了利润。
例6 生产棕色药瓶和啤酒瓶的双滴料板状钼电极加热供料道
在生产100cc棕色药瓶温度较高的双滴料供料道中进行电加热应用,电极布置采用“丁字”形附壁式,在供料道铁壳中前后放两对,在料盆中放一对。采取烤窑前予埋冷装。升温过程中,采取了严密的防护措施。在比较顺利通过了升温关后,连续运行了18个月,达到了预期的技术经济效果。
1.供料道电加热技术经济分析:
(1)电加热后料盆中玻璃液温度稳定。恒流控制温度达±5℃。在瓶子耐压强度方面,按部颁标准进行检验(部颁标准耐压1分钟大于12kg/cm2)。电加热的瓶壁厚薄较为均匀,瓶子耐压强度明显提高,最高曾达到27 kg/cm2,说明了料滴温度均匀,为减轻啤酒瓶重量创造了条件。
(2)泥筒使用周期可达到20-30天以上,提高了一倍,同时泥筒的机械传动构件使用也大为好转。
(3)延长料盆寿命。电加热后,同质量的料盆,可使用一年以上,因此,使用寿命提高一倍以上,同时少浪费了(每换一次料盆)半天生产时间。
(4)每条供料道设备投资如下:单相隔离变压器1台,TDK—2恒流控制仪1台, 钼电极2对。
2. 供料道电加热的设计和使用:
(1)钼板的电流密度在棕色料中使用0.7 A/cm2左右,5mm厚钼板使用了二年,供料道温度在1150℃左右。
(2)防止氧化:电极加工组装好后,先用玻璃质材料把钼电极保护好。在池窑烤窑前放入供料道中,并用玻璃将钼电极复盖,在升温过程中始终用风冷却,不使供料道温度上升600℃以上(此时玻璃也尚未熔),待到升温结束,料加满以后,用柴油加热,把复盖的玻璃熔化(料加满不会倒流了),这样电极就始终被埋在玻璃液中。
(3)换料盆:某厂使用的是一般粘土质的料盆,在使用一年后调换料盆,将工作池与供料道空间隔绝,将料液面降低约2cm(不能将电极暴露在空气中),封住出料口,然后将料盆中的玻璃液往供料道中推进少许,因供料道中有电极,要小心绝不许碰撞。因此,不能为了要减少料盆中的玻璃,拼命把玻璃液往内推,而将电极碰断,料盆中有比较多的玻璃液体存在,在调换中还是顺利的。
料盆调毕,应注意不能一下放大料,由于放料时,供料道中玻璃液仍处在不流动状态,因供料道前后玻璃液温度不一致,易造成后部玻璃粘度大,流速慢,补充不了料盆部分放料量,而造成料液面下降,将部分电极暴露。某厂曾因放料量过大,造成料浅使电极暴露约2cm,很快被氧化侵蚀的情况。
(4)电极结构和加工:用钼板作电极,电极放在玻璃液深中部,某厂电极是自己加工和组装的,钼材是用粉末冶金热轧成型的,比较脆,但它可用一般白金加工方法进行切、车、钻等加工。
(5)钼电极对玻璃液不会沾污:某厂使用的钼材料,纯度达99.95%以上,在使用过程中,没有发现钼对玻璃沾污的现象,某厂玻璃成分中含有0.3%以下的氧化铁,沾污现象不明显。钼能使Fe3O4还原成氧化亚铁。可使玻璃显黄色,这点对青白料的产品应引起注意,某厂由于都是色料(翠绿与棕色),因此也无法发现显色现象。
(6)变压器的电压比选择:某厂使用的电极间距为400mm左右,含R2O14.5%,玻璃液温度在1150℃左右(玻璃液电阻率可根据经验公式计算)。实际上影响电阻因素较复杂,棕色药瓶通道中实际测得的玻璃液电阻见表16.3.12。
表16.3.12
玻璃液温度 |
1150℃ |
1120℃ |
1150℃ |
电极距离360 mm时的电阻 |
0.48Ω |
0.35Ω |
0.30Ω |
电极距离700 mm时的电阻 |
0.64Ω |
0.47Ω |
根据计算选用的变压器电压比为360V-380V/65-70V。在生产过程中基本满足要求。
3.应用供料道电加热以后对小型蓄热式马蹄焰池窑结构和熔制工艺的要求 某厂啤酒瓶供料道空间与马蹄焰池窑没有分隔,使料温变化很大,后来采取了全分隔,供料道温度不受池窑火焰影响,采用电加热时料滴温度大为稳定。 另外,池窑熔制温度和玻璃成分也要相对稳定。某厂池窑属自动控制,比较稳定,玻璃成分变化在正常生产时波动较小,这对采用调压恒流控制的电加热供料道,创造了较好的条件。但池窑温度和玻璃成分有时也有失控。特别当进入供料道的玻璃液温度降低后,电加热功率就需增加,这样使电极区玻璃液温差增大,玻璃液到了料盆还未能均化,致使料形变坏,并易引起气泡,因此,不考虑一定的生产条件,单纯的想完全依靠电加热来达到强制加热玻璃液的目的是不可取的。 |
![]() |
例7 生产玻璃器皿的板状钼电极加热供料道
1.供料道热工估算
在热工测试的基础上,供料道的热工估算见表16.3.13。
表16.3.13
热量 收入 Kcal/h |
玻璃液降温余热 |
3637 |
电极供给热量 |
8659 | |
合计 |
12296 | |
热量 支出 Kcal/h |
供料道壁散热 |
9679 |
煤气口辐射热损失 |
538 | |
料盆散热 |
2079 | |
匀料筒溢流热损失及其它热损失 |
* | |
合计 |
12296 |
*考虑供料道存有一定空间,出料量少时,玻璃液表面散热相对较多,为防止产生料皮,适当加些煤气(稳压),亦可弥补料筒散热,故未计入。
根据焦耳定律及供料道热平衡方程式:Q=0.24I2RT,计算得到:Q≈10KW,因用埋入式电极加热,其热利用率为90%,故定电极输入功率为:Q=11.2KW。
2.电工参数估算:
①玻璃的电阻率:根据计算Na、Ca、Mg、Al、Si玻璃电阻率方程式, 计算得到x=0.1938 (Ω-1.cm-1),则:r=5.16(Ωcm)。该厂的器皿玻璃中Na2O重量百分含量为15%,进入供料道的玻璃液的平均温度为1523K。
②玻璃液电阻:根据板状电极布置的电阻计算公式得到:R=0.2068(Ω)。电极板几何距离37cm,供料道导电区的有效宽度38cm,玻璃液深度25cm。
③变压器的二次特性:供料道采取二台变压器控制,各以5.6KVA的功率单相供电,根据电热平衡方程式: Q=V.I=I2R,次级电流和次级电压分别为:I=165A、V=34V。
为了适应器皿产品出料量变动频繁的需要以及节省升温时间,设计次级电压值分别为45V,60V,这样各段输入功率即可达10KVA。
3.供料道结构
供料道的基本特点是,该厂为C型供料道,宽度400mm 。供料道长度的确定与出料量有直接关系。在保证料质、节约能源、减少投资、工艺布置合理的前提下,尽可能缩短供料道长度,使其显示出****的经济效果。从使用情况看,当日出料量在5-9T时,供料道长度以3-3.5m为宜;日出料量低于5T时,长度应相应缩短。
供料道空间尽可能低些以减少液面散热损失,但由于玻璃在低温时,不具有导电特性,供料道通电前需有一预加热过程,同时若安全供电不很可靠时,亦需有可靠的煤气燃烧空间。将原供料道空间高度由220mm降至150 mm。
为减少工作池温度对供料道温度的影响,使供料道的玻璃液温度趋于稳定,供料道与工作池空间应预全分隔。
4.电极
钼电极表面电流密度:电流密度大时,玻璃液温度升高,玻璃液内气体分压增大,致使二次气泡产生,玻璃液质量下降。钼板电极电流密度值为0.4-0.7A/cm2及0.63 A/cm2。
作为埋入式供料道电加热的电极,为提高玻璃液断面温度的均匀性,减少因电极损耗后局部电流密度过大所造成的二次气泡以及减少设备投资,采用了板状钼电极。
为了防止钼电极高温氧化,钼电极采用无水冷保护法,同时,针对板状电极在供料道运行期间不易更换这一弱点,采取了必要的措施。
由于电极周围耐火材料较其它部位侵蚀速度快,器皿玻璃料质量要求高,所以对电极砖的质量要求就较高。选用烧结较为致密的AZS砖。在此砖上打孔,电极砖孔与保护套间隙适中,使电极具有较高的可靠性。
5.供料道的保温
采用了加厚保温层以及表面铺设高铝纤维棉的方法对供料道进行保温,供料道表面平均温度由116℃降至74℃。
6.供电调节 为达到供料道内玻璃液温度稳定和料滴温度恒定的目的,对供料道中的冷却段和调节段分别进行控制,以独立的单相可控硅电压调整器控制隔离变压器。对冷却段安装的一对电极,实行手控,使玻璃液温度达到成型所需的平均温度。对调节段安装的一对电极,实行自控。在靠近料盆部位的玻璃液中插入WRLB热电偶,由热电偶产生的直流信号输入到动圈式温度指示调节仪XCT—191显示温度。确定所需的料滴成型****温度值输入调节仪表,经仪表比例、积分、微积分运算后输出0-10mA电流信号控制移向脉冲,至可控硅电压调整,经变压器向钼电极供电。玻璃液温度的变化,再由热电偶WRLB的信号反馈至调节仪表,这样温度微有变化,钼电极至玻璃液的电流就随之增加或减少,使料滴温度达到理想的恒定值。其恒温温差在±1.0℃(电路控制见图16.3.11) W—热电偶WRLB,X—动圈式温度指示调节仪,T—可控硅电压调整器,B1B2—单相隔离变压器10KVA,次级电压分别为220V/150V,220V/60V,MO—板状钼电极。 7.电极布置、电流分布 电极布置的合理与否,影响玻璃液质量及耐火材料寿命。主要从供料道热量需要的部位、电工学因素、电极周围玻璃液流变化等方面考虑。兼顾在保证料质的前提下,节省投资。供料道内安装了两对电极,电极安装于玻璃液面下约20 mm处。 |
![]() |
电极的安装位置确定以后,必须慎重考虑供电及电流的分布,这不仅关系到耐火材料和钼电极的寿命,还关系到用电量的节约与浪费,以及玻璃液温度的均匀分布。
图16.3.12 所示为长方形单相供电电流交叉分布,由于A+1 —A-1的单相供电交叉在A+ —A- 之间,使玻璃液温度不易控制。
图16.3.13所示为长方形单相供电电流平行分布(沿供料道壁),由于A+1 —A-1及A+ —A-供电均在供料道侧壁附近,使电极板侧面间电流过大,造成电极和耐火材料寿命缩短,玻璃液内产生气泡较多。
图16.3.14为长方形两相供电电流分布,由于采用两相电压控制,温度控制有所提高,但两电极侧面间电流当然很大,两侧耐火材料及电极寿命就短,玻璃液内产生气泡也较多。
经过认真筛选,选择了图16.3.15所示的长方体形单相供电电流平行分布的方案。
8.供料道运行效果
通过对供料道半年来运行情况的观察,电加热恒温自控较煤气集中火焰加热优点甚多。
(1)料滴合格率保持在93%以上。以电作热源,改善了供料道中玻璃液的热分布,消除了因煤气不完全燃烧造成的脏料现象,加之对供料道实行合理保温,减少了玻璃液的垂直与横向温差。原煤气“侧烧”,往往因局部耐火材料蚀损致使玻璃液污染。电加热供料道的电极砖选用优质耐火材料,降低了耐火材料的蚀损速度,减少了污染。改善了玻璃液质量。
(2)能耗降低:用电直接加热供料道内的玻璃液比用煤气加热能耗低。以同一长度供料道,同一出料量情况作一比较:原供料道用煤气量平均为19m3/h(压缩空气耗电未计入),现用电量8-13Kw(夏、冬季不等),节省热量70632-66327Kcal/h(煤气热值以4080Kcal/m3,电热值以861Kcal/Kwh计算)。
(3)提高玻璃液利用率:由于电控、温度调节方便,灵敏,使更换产品时的停机时间缩短。
例8 某制瓶生产线的板状电极电加热供料道
某厂1982年开始采用埋入式钼电极加热方式来控制供料道温度,一直是人工手动恒流控制,比用油枪控制的效果大有好转。1991年10月,该厂在2号窑6组双滴行列机配套的电加热供料道上,控制方式有了改进,温度的稳定性和料液的均匀度都有提高。
图16.3.16是该厂为6组双滴行列机配套的电加热供料道系统。该供料道长6926m m、宽1170m m,纵向设置了6对板状钼电极,分别作为Ⅰ、Ⅱ、Ⅲ区的加热调节段;靠近工作池的1210m m段为基温调节段;在料盆两侧设有两支U型硅碳棒作为恒温区。整个供料道沿纵向设置了5个温度控制区,且控制方式分别为风量控制、功率控制和恒温控制。
1.瓶罐玻璃的化学成分
表7.3.14 瓶罐玻璃的化学成分(重量%)
料别 |
SiO2 |
Al2O3 |
Fe2O3 |
CaO |
MgO |
Na2O\K2O |
青白料 |
70.12 |
5.82 |
6.33 |
8.31 |
1.75 |
15.19 |
高白料 |
74.30 |
1.41 |
6.16 |
7.93 |
1.65 |
14.45 |
普白料 |
60.50 |
5.59 |
6.36 |
8.33 |
2.19 |
14.13 |
翠绿料 |
70.73 |
5.04 |
6.15 |
7.35 |
2.14 |
14.26 |
2.供料道结构
供料道宽度考虑与各种不同的供料机相匹配,且考虑不同规格标准的供料道砖。主供料道内宽为660mm。
供料道的长度应满足双滴料的工艺条件,进入供料道的玻璃液有较长的停留时间,以及满足多变化产品的需要,且留有宽裕的调节余量和达到高精度的温度控制。参考已成熟的6组单滴、长5500mm的电加热供料道的工艺参数,结合现场条件,确定长为6920mm。
由于供料道砖和挡砖直接与玻璃液接触,选用高温强度大、热稳定性高、抗侵蚀性强、膨胀和导热系数小、热态电阻大的硅线石材料。火焰空间砖和盖板砖采用普通粘土质材料。
3.电气及控制系统
该供料道的控制系统如图16.3.17。从基区到尾区都分别采用单闭环调节系统。根据其它供料道的电工参数(即通入玻璃液的电流、电压、温度)和参考表16.3.14中K2O、Na2O的百分含量,并结合电极板面积和供料道通电宽度,选择容量为35KVA电压比为380V/60V、70V隔离变压器供电。
该厂曾使用过ZK-1型可控硅调节器、HLK-2、HLK-3型恒流恒温控制仪,一直未能满意。上述仪表均系可控硅调压方式。通过可控硅加到主变压器初级的电压波形为不完整正弦波,且波形的“缺角”大小与控制仪表的触发角α直接对应,这种波形很不适应变压器这种大电感负载的使用。因此,即使只有一个加热区的供料道,也难以达到自动调节作用,当使用在两个加热区以上的供料道,就是手动调节也较难操作,原因是电感负载的电流滞后和自感电动势的随机叠加产生直流分量和波形畸变,使变压器运行于短路状态而频繁地烧断快熔。
另外,在电力配备上,直接造成三相不平衡状态,在投入较大功率时,必须加大零线面积,以保证人身、设备的安全。
4.调功器的选用
该厂经过一段时期的探索研究,决定选用调功器,经过前两条供料道一年多使用来看,从未烧过一次快熔,也没有其它故障发生。
5.温度检测
在任何一个自动调节系统中,检测点的设置和检测元件的性能都是至关重要的,在很大程度上影响控制精度。
温度测点位置设计如图1。基区检测是在供料道盖板上方留一个φ80通孔,将在线式红外测温镜头架在通孔上方的300mm处,镜头带有冷却套。该镜头直接测得所处玻璃液面的温度高低,响应时间小于0.15s,因此基温区很容易将高温玻璃液通过调速风机的风量调节,稳定于给定值。
Ⅰ、Ⅱ、Ⅲ区的检测点,分别在每个加热段“后边缘”的料液面下30mm处,用WRR热电偶从供料道侧墙斜插入玻璃液内,热电偶不可暴露在供料道空间,以延长使用寿命和提高控制精度。插入方式如图16.3.18。
6.控制系统的整定 自动控制系统的控制质量取决于对象特性、控制方案、干扰形式与幅值以及调节器参数的整定。当一个控制系统组成安装后,调节仪表控制对象、干扰形式等也都基本固定下来,这时的控制质量主要取决于调节器参数的设置。当然,如果系统设计不合理,对象特性不好或仪表安装不当,想通过调节器的参数整定来获得良好的控制质量,也是不可能的。 如图16.3.17取供料道中温度受控最灵敏点作为控制对象;五个控制区的设置客观上就使温度的稳定性得到提高;调节器选用XMTS温度数字调节仪。该仪表采用微机技术,性能价格比较高,分辨率较高;PID设定范围是P:2-500%;I:1-2400S,D:0-1200S,微分增值KD:8。系统的整定采用一般的经验法。 |
|
7.钼电极
采用了带高温防氧化涂层的5mm厚的板状钼电极,经三年半的使用后变成3mm厚,电极的面积和四个角均无变化。供料道共用了6对带高温防氧化涂层的钼电极。
电极板及与其连接用的过渡钼棒均要求用高纯钼粉以粉末冶金法经挤压、锻打等工序加工形成。其纯度要求为:M0>99.9%,C<50ppm,Fe<50ppm,与过渡钼棒连接的“引电棒”,用1Cr18iN9Ti外螺纹。
如图16.3.18将钼电极安装于凹槽内,这样即可避免较大尺寸的电极板对连接钼棒的剪切力而造成电极断掉,又可防止在供料道内机械操作而损坏电极,并且有利于保护电极“上边缘”不至于偶然掉料面而加速氧化和减小玻璃液的直接冲刷。
例9 某厂引进的供料道电加热技术简介
1983年某厂学习国内外先进技术采用耐用高温金属钼(Mo)作供料道电极,采用200×100×6mm的钼板作电极,每条供料道靠近调节段安装三对或四对电极,电极埋设在供料道内两侧的玻璃液中,利用高温熔融玻璃液导电性能,电流在玻璃液中自身加热,经过380/60伏变压器使电流在玻璃液中横向通过,加热玻璃液,对均匀玻璃液温度起较好的调节作用。自动控制系统是由HLK—1型或HLK—2型恒流控制仪作为交流调压装置恒流控制,使供料道的温度得到自动调整,这种加热的温度调节一般可以稳定在±5℃左右,对于单滴料制瓶机来说基本可以取代燃油加热,每台供料道耗电功率约为10—15Kw,使用安全可靠,只是钼电极在600℃以上时容易氧化,因此在安装、升温、放料过程中要采取各种保护措施,以保证电极的完好无损。
上述电加热方式是辅助加热,热能量有限,对于产量大的双滴料制瓶机要求料温更加稳定的情况就难以满足了。
此页网址为:
相关文章