工程分类
更多>>![]() |
|
![]() |
|
![]() |
|
![]() |
|
![]() |
|
![]() |
|
![]() |
|
![]() |
|
![]() |
|
![]() |
|
![]() |
|
![]() |
|
![]() |
|
![]() |
|
![]() |
|
![]() |
|
![]() |
|
![]() |
|
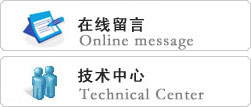
联系人:
电话:0511-88791451
手机:13951280541
邮箱:jfchen@ujs.edu.cn
地址:镇江市学府路80号
最新文章
您的位置:网站首页 > 最新文章火焰池窑的电助熔——电助熔池窑的实例
12.1生产硼硅酸盐玻璃的电助熔池窑
例1生产安瓿玻璃的电助熔池窑
在采用玻璃电助熔技术之前,某厂的玻璃池窑都是以天然气作燃料来熔化玻璃液的,因为天然气自身的黑度小,(明焰时ε=0.6,暗焰时ε=0.2),火焰中含碳量少,所以只能靠窑墙吸收热能后的反射能和很少一部分火焰的辐射能来熔化玻璃。另外天然气的燃烧速度慢,使窑内的温度不好控制,以及天然气的重度小(r=0.79-0.82Kg/Bm3),则又导致燃烧火焰易于发飘,不易贴近玻璃液面,从而大大削弱了火焰对玻璃液的热量传递,使熔化速度减慢。为了弥补因天然气燃烧给玻璃熔化带来的不足、提高玻璃液质量,在玻璃熔窑上采用了电助熔加热技术,经过几年来的实践证明,效果是非常好的。
1.玻璃的高温电阻率
该厂生产的安瓿玻璃,属中性硼硅酸盐玻璃,由于硼氧四面体的形成,及一价的金属阳离子量少,再加之在玻璃原料中又是引用的钾长石(K+的离子半径大于Na+的离子半径)。从而使安瓿玻璃的高温电阻率比普通钠钙硅酸盐玻璃的高温电阻率要大些。
2.玻璃液的电阻、电压、电流的关系
用欧姆定律直接算出各种温度状态下玻璃液的电阻(见附表12.1.1)
表12.1.1
玻璃液温度 |
加在电极上的电压 |
通入玻璃中电流 |
玻璃液电阻 |
1200℃ |
260V |
300A |
0.87 |
1300℃ |
195V |
100A |
0.49 |
1400℃ |
173V |
450A |
0.38 |
1500℃ |
142V |
550A |
0.26 |
1550℃ |
130V |
600A |
0.217 |
3.电极电流密度
钼电极的电流密度一般不超过1A/cm2。该厂使用φ50mm的钼电极,电流密度J=0.309A/cm2。
4.变压器的选择
变压器的功率为180KVA,V1=380V单相,V2=150V/ 130V/ 110V/ 90V。I1=474A,I2=1200A。
5.控制方案的选择 采取恒流控制。
6.电极的选择 选用的φ50×1200mm,比重为10.1的高纯钼棒作电极,经多年的使用,效果是非常好的。钼电极的保护如图12.1.1所示。钼电极在未顶入玻璃料池前应用白泡石塞子将电极孔塞住水套则相应通水。当玻璃液的深度高过电极孔后,将电极逐步顶入玻璃内。待玻璃液达到液面线要求后,从加料口将浮起的塞子掏出。当钼电极顶入玻璃液中,可以通过观察电流的大小来判断钼电极的氧化程度,用恒流控制仪测定的数据来判断。根据电流和电压的变化随时对电极顶入的长度进行调整。如电压升高20%则电极应顶入5mm(因电流是恒流,只能用电压调整)另外电极每使用2个月后,应顶入100mm,即可保证电极的使用效果。使用的钼电极,其化学不纯物如下 C:20—50PPm; Al:1PPm; Si:5PPm; O2:7.9PPm; W:2.1PPm; N1:0.5PPm; Fe:10PPm。玻璃的澄清剂只能用Na2SO4和NaC1,最好是氧化铈,而不能用白砒和锑粉。电极的布置如图12.1.2。
|
![]() |
7.供电方式如图12.1.3和图12.1.4
8.主要技术经济指标
表12.1.2
图12.1.4工作池供电方式
8.主要技术经济指标
表12.1.2
窑炉的运转周期: |
52个月(中途检修过一次) | |
熔 化 池 |
面积m2 |
16.8 |
池深m |
1.2 | |
温度℃ |
1570±5 | |
工 作 池 |
面积m2 |
2.2 |
池深m |
0.9 | |
温度℃ |
1300℃±5 | |
日产量(t): |
13 (日产合格率玻管8—9T) | |
熔化率 kg/m2d |
900 (纯天然气时500—650kg/m2d) | |
能耗 |
天然气5200m3/d 电功率400Kw | |
熔 化 池 |
初级电压V |
390—410 |
初级电流A |
125—180 | |
次级电压V |
140—165 | |
次级电流A |
350—150 | |
工 作 池 |
初级电压V |
385 |
初级电流A |
40 | |
次级电压V |
130 | |
次级电流A |
140 | |
玻璃窑炉单耗 |
3900Kcal/Kg玻璃液 纯天然气为5000Kcal/Kg玻璃) |
9.电助熔的使用效果
(1)电助熔促进了玻璃液澄清,大大降低了玻璃制品的条纹、结石、气泡等缺陷。
(2)硼硅酸盐玻璃在熔制时,硼的挥发要占整个原料引入量的15%左右。采用了电助熔后,火焰空间的温度相应地降低,减少了玻璃液表面的挥发,同时也减轻挥发份和火焰对窑体的侵蚀和冲刷,大大提高了窑炉的使用寿命。
(3)硼硅酸盐玻璃由于硬化速度快,结晶倾向大,在窑炉的底部最易形成一层不动层,在玻璃液的表面又会形成一层变质层(因易挥发份的挥发)。形成的不动层和变质层导致玻璃的析晶。当采用电助熔后,热能直接作用于玻璃内部,使玻璃液内部温度升高,对流加快,从而降低了析晶的倾向、使玻璃液质量提高。
(4)电助熔窑炉,只要控制好进出料量,电压、电流等工艺参数,就可以达到****熔制工艺状态。电助熔窑炉,熔制工艺稳定,控制简便可靠,调节灵敏,玻璃液质量好。
例2 生产高硼硅仪器玻璃的电助熔池窑
某厂建成一条生产高硼硅玻璃烧器的电助熔池窑。两年多的运行证明,窑炉的运行可靠,产品质量优良,达到了预定的设计指标。保证了向成型机提供高质量的玻璃液。满足了机械化、自动化大批量生产的需求。
采用电助熔可以利用原有的发生炉煤气。在设计过程中,主要考虑电极材料、电极保护、电流平衡、电极布置、绝缘保护等一系列问题。
电极布置如图12.1.5。根据测定,窑炉采用电助熔工艺后,碹顶温度比未用前降低了近100℃,火焰空间热负荷值只是原来的36%,为76×103KCal/h。池底温度升高了近70℃。产品中结石、条纹缺陷大大下降,出料量从过去的****6t/d提高到现在的15t/d,电能几乎全部转变为热能(约1.5×106KCal/h)被玻璃液所吸收。熔化热效率从改造前的7.9%提高到了38%,单位能耗从10833KCal/kg玻璃降低到了2263KCal/Kg玻璃。熔化率从0.25t/m2·d提高到了0.765t/m2·d。高硼硅仪器玻璃的熔化率及单位能耗均达到了较高的水平。
1.池窑的结构 窑熔化池长5200mm,宽3700mm,长宽比为1.405,池深900mm,池底厚550mm,池壁厚200mm,火焰空间高1075mm,胸墙高600mm,熔化面积19.6m2。工作池长3000mm,宽1150mm,深525mm,火焰空间高550mm。 (1)熔化池池深 窑池深900mm,超出经验数值300mm以上,电助熔技术应用后,炉底温度有较大幅度的提高,底层玻璃液的粘度也变小,熔化池的容量得到相应的增加。 (2)池底结构 由于电极是采用池底垂直插入的方式,池底14个电极孔要求池底结构绝对安全。池底的侵蚀主要是玻璃液的渗透和金属液的钻蚀。池底结构,仿照法国西普公司五层池底结构,最上层为厚75mm的ER—1681RT铺面砖,铺面砖层下面是两层锆刚玉捣打层(ERSOL),第一层为厚5mm层(ERSOL—06L),第二层为厚65mm层(ERSOL—50V),捣打层下是厚200mm的粘土砖,再下层是厚185mm的保温层及厚20mm的绝缘层。这种结构整体性强,防渗透、防侵蚀性能好,施工简便快速。经过两年多的使用,池底状况一直良好。没有出现任何异常情况。
(3)放料、溢料 高硼硅仪器玻璃易分层和组分中B2O3易挥发,池窑共设有4个放料孔和3个溢料口,其中熔化池有一个池底放料孔,工作池有一个池底放料孔和一个溢料口,放料孔用于定期将池底变质玻璃液排出,溢料口则有单独的加热喷枪,用于排除玻璃表面因B2O3的挥发所产生的浮渣,避免其混入成型流而形成透明疙瘩或结石等缺陷。垂直引下拉管料道上设置了一个放料孔和两个溢料口,吹泡机料道上设置了一个放料孔和一个溢料口。料道的溢料口除具有与工作池溢料口相同的作用外,还具有调节玻璃液面高低,稳定液流的作用。
2.耐火材料的选用
在一些关键部位选用了法国西普(SEPR)公司的电熔锆刚玉砖及其捣打料,而其余部分一律用国产耐火材料。
①熔化池及工作池底:最上层为无缩孔ER—1681RT铺面砖,下面是直径≤0.6mm的电熔AZS捣打层(ERSOL—06L),它具有很好的可塑性,用少量水搅和后并不凝结,作为池底衬砖的底衬,可以使池底衬砖在升温过程中自由地膨胀,再下面是一层ERSOL—50V捣打层,它的颗粒直径≤50mm,遇水后能够迅速硬结,用来作为池底粘土砖之上的基层。烤炉升温过程中,当温度超过1200℃后,由于捣打层层中所含的陶瓷粘结剂的作用,这两种捣打层开始逐渐进行陶瓷化,并融合成一体,整个池底衬砖形成了一整块可靠的中间隔层,从而可以有效地阻止玻璃液的渗透和金属液的向下钻蚀。
②熔化池电极砖 在以电极为中心半径为30cm的范围内,电极所释放的能量将占它所释放的总能量的60%左右,电极附近释放能量很大,玻璃液温度高,粘度小,加之剧烈的液流,耐火材料所受到的侵蚀相当厉害,在这一部位,选用了比ER1681—RT砖抗侵蚀性能更好的无缩孔ER—1711RT砖,厚度300mm,在电极砖和池底其余部分相接触的部位做了特殊的处理。经过两年的使用没有发生任何问题。
③熔化池池壁砖 使用电助熔技术后,池深方向的垂直液流更加激烈。熔化池池壁砖全部选了西普公司生产的电熔锆刚玉砖;其中加料口拐角采用了ER—1711RT砖,其余部分采用了ER—1681RT砖,全部为一块立砌,铸口向外放在底部。
④工作池池壁砖 工作池池壁选用了ER1681—RN砖。
⑤流液洞 液流洞这一关键部位选用了抗侵蚀性能良好的ER1711—RT砖。
⑥熔化池、工作池上部空间 熔化池、工作池上部火焰空间结构,选用国产硅砖。
3.池窑的保温
①熔化池 熔化池池底采用185mm厚的轻质粘土砖为保温层,中间夹砌粘土砖承重。电极砖下为200mm厚的粘土大砖,不另作保温。熔化池池壁采用100mm厚轻质粘土砖作为保温层,考虑到电助熔使池壁附近玻璃粘度下降,流动激烈,会加剧对砖缝的渗透作用,池壁砖全部留砖缝不保温。液面线部位也不保温。由于熔化高硼硅玻璃时所需温度高,火焰空间热负荷强度比较大,为保护大碹不致过早蚀损,对于大碹未加保温。
②工作池 工作池池底温度较低,需要较好的保温。在厚200mm在厚的粘土砖下砌130mm轻质粘土砖来进行保温。池壁采用113mm厚粘土砖保温。由于工作池玻璃液粘度较大,并且没有电加热,故池壁保温不留砖缝。工作池碹顶也采取了保温措施,在碹顶上,先为一层厚5mm的石英砖,其上为厚度为113mm的轻质硅砖,。
在熔化池和工作池底的放料孔和电极孔处都采用ER1711—RT砖加粘土大砖的结构,未加特殊的保温。
4.池窑的加热方式
(1)熔化池 熔化池采用电助熔的加热方式。电极功率分区控制,将上部火焰的温度与下部电极所产生的温度配合起来,从而控制窑内的玻璃液流,稳定玻璃液的流动。对于熔化不同玻璃品种时,可以改变电极插入的深度以调节池底温度的范围。
(2)工作池 工作池燃烧系统为多喷嘴加热,能够方便地调节工作池内温度分布,有利于排除玻璃液表面硼挥发引起的浮渣等。经两年多来的使用,运转良好,炉内温度可达1550℃,完全可以满足生产上的需要。在工作池加热系统中,对于助燃空气的预热采用了辐射式金属换热器。空气预热后再与煤气混合喷入窑内燃烧,其预热温度可达350℃。解决了高温烟气的利用问题。工作池每公斤玻璃热能比原4#窑降低了67%,从原来的1520KCal/kg玻璃液降到现在的506Kcal/kg玻璃液。
5.其它
采用推入式加料机,液面自动控制,电极水温报警。产品合格率从过去的平均60%以下而上升为92%以上。单耗从原来的30t标煤/t成品降至3.6t标煤/t成品。
此页网址为:
相关文章