工程分类
更多>>![]() |
|
![]() |
|
![]() |
|
![]() |
|
![]() |
|
![]() |
|
![]() |
|
![]() |
|
![]() |
|
![]() |
|
![]() |
|
![]() |
|
![]() |
|
![]() |
|
![]() |
|
![]() |
|
![]() |
|
![]() |
|
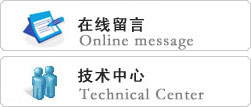
联系人:
电话:0511-88791451
手机:13951280541
邮箱:jfchen@ujs.edu.cn
地址:镇江市学府路80号
最新文章
您的位置:网站首页 > 最新文章全电熔窑的烤窑和运行——电熔窑的操作
电熔窑的操作事实上并不比火焰池窑操作困难。要求操作人员必须能够读取仪表的记录,并进行控制装置的调节。需要加以监控的因素有:功率输入、玻璃温度、配合料的均匀加料、冷却水的温度、以及电极状况。如有需要,电熔窑可以实现全自动控制,不用操作人员,只要偶而进行检查就行了。
每周一次核查电极的状况,必要时加以调整,一般检查电熔窑大砖、水冷却系统、配合料输送设备、热电偶及其它电气设备。
在采用电熔窑时,务必采取安全措施。大多数电熔窑上的接地电压必须小于90伏。在调整电极时,通常应断电,若在玻璃液中应用金属质的装置,它们的柄应加以绝缘,操作人员应戴绝缘手套,并站立在绝缘的操作台上(例如铺有石棉水泥板或木板的操作台)。一项附加的安全措施是:将一柔性铜缆的一端连接于上述金属质装置,将其另一端连接于建筑物的钢架。
8.2.1 熔化温度和输入功率。
电熔窑熔制玻璃时,熔化率达2.4~3T/m2·d,是火焰池窑的5~6倍。电熔窑的电流通过玻璃液本身发热,温度最高区在玻璃液内部,玻璃熔制过程进行得比较快,玻璃液对流强烈。电熔窑熔化池深度一般在1.6m以上,玻璃液有充裕的时间进行澄清均化。
在电熔窑生产中,熔化温度、操作功率及玻璃液电阻三者间密切相关,且均是控制电熔窑运行的主要参数。
要获得优质的玻璃,熔化温度以1400~1480℃为宜。温度过高,缩短了耐火材料和电极的寿命;温度太低,玻璃质量下降。在实际生产中,由于各电熔窑结构、热电偶安装位置及插入深度不同,仪表所显示的温度与实际温度有误差,所以各电熔窑的熔制温度是不尽相同的。
电熔窑温度是通过操作功率来调节的。只装置一层电极的电熔窑,炉温最高点位于电极区间,沿池深方向的温度曲线靠电极输入功率和玻璃液流量来调节。装置多层(如三层)电极的电熔窑,其各层电极由独立的变压器供电,改变各层的输入功率可调节电熔窑内温度分布。通常上层电极为熔化提供热量,下层电极调整进入流液洞的玻璃液温度。各层电极功率分配应遵循以下原则:熔化量大时,最上层电极输入的能量最多;熔化量小时,第二层和第三层电极输入较多的能量。这样有助于使配合料层厚度和流液洞温度保持稳定。
玻璃的温度与电极间电阻存在着一定的关系,尽管到目前为止仍不能实现电阻控制,但某些电熔窑以电极间玻璃液的瞬时电阻值作为反映熔融玻璃内部状况的一种趋向指标。例如温度的微小增量则反映为电阻值的微小减量。当电阻值没有变化,而温度却发生某种变化,则表明测温系统有误差;当温度没有变化,电阻值有变化时则表明电极或配合料成分方面存在问题。
8.2.2 熔化量(翻转限Turn—Down Limit)。
火焰窑一般只有****熔化量的限制,而电熔窑既有****熔化量限制,又有最小熔化量限制(称为翻转限Turn—Down Limit)。
玻璃熔化温度取决于玻璃化学组成和熔化率。在正常熔化温度下,配合料熔制速度和电熔窑的熔化量保持平衡时,配合料覆盖层厚度是稳定的。熔化量减少,输入功率降低时,玻璃温度随之有所下降。当玻璃温度下降到维持澄清所需的最低限度时,即到达了“翻转下限量”。大多数玻璃的翻转下限量约为电熔窑熔化能力的50%。若玻璃质量有较严格要求,“翻转下限量”比****熔化量低20%。若对玻璃质量要求不太高,电熔窑的“翻转下限量”可比****熔化量低60%。
当电熔窑熔化量降到下限以下而又要保持澄清所需温度时,必然出现输入功率大于熔化所需功率现象。这时玻璃液温度升高,配合料层逐渐熔化,上部空间温度将升高数百度,导冷顶被破坏。
另一方面,熔化量过小,通过流液洞狭小通道的玻璃液带入的热量很少,流液洞、上升道电极提供的热量不足以维持正常的温度,该区温度下降,玻璃电阻增大,电流下降,使玻璃温度进一步降低。若这种趋势不能及时制止,可能引起流液洞、上升道的玻璃液凝固,使电熔窑被迫停炉。因此,在任何情况下都应让流液洞、上升道保持最低限度的流量。(即时停电时也要保证玻璃液的流动)。
8.2.3 配合料覆盖层
配合料料毯的厚度是电熔窑生产中的一个重要工艺参数。配合料料毯厚度一般为200~300mm。图6.5.1是某电熔窑配合料料毯内温度分布曲线。随着配合料深度的增加,配合料温度有所上升,当达到某一特定深度时,温度急剧升高到1200℃左右。
配合料覆盖层不仅能促使低温液相形成,加速玻璃熔化,还能阻挡易挥发成分外逸并起隔热作用。
如果配合料料毯太薄或者熔透,熔化池主电极的输入功率就不足以维持熔化所需的温度。
如果配合料料毯过厚,出料量大时料毯层与电极间的距离缩短,最上层电极间玻璃温度下降,电阻增大,输入功率下降,熔化温度随之降低,熔化速度进一步下降,熔化时放出的气体外逸受阻,电熔窑运行状况恶化。如果不及时减少出料量,生产将受到严重影响。
如果配合料料毯厚度分布不匀,较薄部位会发红,熔化放出的气体在这里聚集,形成缓慢上升而又连续不断的“大泡”,泡径可达200~300mm。随着“大泡”翻上来的熔融玻璃液除了影响加料机工作外,还可能引起“短路”。因此加料机应均匀地覆盖配合料,使池墙周边的料层较薄、呈红热状态,以防配合料层结拱。
8.2.4 电极插入深度
电极插入深度与电极性质、数量、电流密度、电熔窑结构等因素有关。如圆柱形氧化锡电极采取垂直安装方式,插入深度约为250mm,在电熔窑运行期间电极不能推进。如棒状钼电极水平安装,插入深度为300~600mm。随着钼电极逐渐消耗,电极间玻璃电阻不断增加,变压器电压不断升高(使电流保持恒定)。当变压器电压调到极限,应推进钼电极,电流、功率诸参数才能恢复正常。
8.2.5 玻璃组成及配合料
电熔窑的玻璃成分与火焰池窑基本相似,两者的主要区别在于电熔窑的配合料中As2O3及Sb2O3含量应小于0.25%。碱性氧化物和易挥发份的量补充得少一些,玻璃的熔化和澄清几乎在同一温度下进行,为保证熔化工艺的稳定,玻璃液上部必须保持一定厚度的料毯层,才能使玻璃液中的气体溢出。这是熔化工艺中选择电功率、配合料组份,澄清剂用量的关键问题之一。
1.如电熔窑熔化铅晶质玻璃配合料中的挥发量仅为0.2%左右,配方几乎不需计算增补量。氧化铅不必用硅酸铅引入,红丹(Pb3O4)或黄丹(PbO)都可使用。铅晶质玻璃配合料中用硝酸钾和碳酸钾引入氧化钾(加入适量的硝酸钾对于熔制极为重要)。某些工厂因硝酸钾价格低,不吸潮,便于配合料制备和贮运,所以组成中的氧化钾全部用硝酸钾引入。但多数工厂是以碳酸钾为主。硝酸钾用量过大时,配合料气体比大,不利澄清,且加剧了对耐火材料的侵蚀,还可能形成“硝水”,严重腐蚀窑体。电熔窑配合料其用量为2.5~3kg硝酸钾/100kg石英砂。火焰池窑的铅晶质玻璃化学成分和配料方案不能保证电熔窑熔化工艺的稳定和玻璃液的质量。适合于电熔窑的铅晶质玻璃的化学组成及配料如表8.2.1。
表8.2.1
配料组成 |
100kg配合料玻璃中的成分 |
氧化物 |
玻璃中氧化物重量 | ||
火焰池窑 |
电熔窑 |
火焰窑 |
电熔窑 | ||
石英砂 |
58.32 |
58.32 |
SiO2 |
58.0 |
58.0 |
纯碱 |
3.6 |
3.4 |
Na2O |
2.0 |
2.0 |
碳酸钾 |
22.3 |
25.12 |
K2O |
15.0 |
15.0 |
硝酸钾 |
6.9 |
1.1 | |||
白砒 |
0.47 |
0.16 |
As2O3 |
0.47 |
0.16 |
氧化锌 |
1.0 |
1.0 |
ZnO |
1.0 |
1.0 |
氧化铅 |
25.86 |
25.0 |
PbO |
24.0 |
24.0 |
2.澄清剂引入量:电熔窑配合料中澄清剂引入量为0.34~0.43kgSb2O3或As2O3/100kg石英砂。对于钼电极电熔窑,由于上述澄清剂对电极有明显的腐蚀作用,澄清剂用量宜小于0.025kgAs2O3或Sb2O3/100kg石英砂。最好选择CeO2作澄清剂。
3.碎玻璃比例:电熔窑正常运行时,碎玻璃量控制在30%左右。碎玻璃应经过挑选、清洗后破碎成20mm左右的小块。碎玻璃比例过大,使玻璃含铁量增加,影响玻璃质量。同时,对电熔窑而言,虽能在大致正常的状态下运行,但此时的熔化能力下限将大大提高,若要使电熔窑在其设计熔化能力下限运行,应使碎玻璃加入量减少到20%以下。
8.2.6 由于澄清区温度高,可使溶解在玻璃中的气体减少,同时气泡也易于排除。在垂直电熔窑中,由于气泡排除的方向和玻璃的液流方向相反,操作中取料的液流速度应小于气泡上升的速度,以免气泡被带到工作池中。
8.2.7停电问题
电熔窑在停电2小时以内,能够完全控制而无需采取其它措施。停电期间电熔窑各部位的温度均下降。来电后即可将各处电极通电,使各处温度恢复正常。停电时间在2~8小时之内,就必须放下熔化池的炉门,点燃煤气喷嘴,用火焰加热,使原先的冷顶变为热顶,并用备用发电机对流液洞、上升道、料道和工作池等部位进行电加热。
停电最多不能超过8小时,若超过8小时,电熔窑的某些部位的玻璃液将会凝固。因为火焰加热只能加热熔化池表层玻璃液,发电机所供电能也只能加热流液洞至工作池的某些区域,所以存在着一些既不能用火焰加热、也不能用电加热的区域。仅靠邻近玻璃传导的热量是无法阻止这些区域的玻璃液温度下降,最终导致凝固的。
电熔窑在运行过程中停电超过9小时。可采用以下方法解决。
1.首先从工作池挑料,向熔化池加料,促使整个系统产生工作流,使熔化池上层的热玻璃液流入流液洞和上升道,将流液洞和上升道内的冷玻璃排放出去。
2.打乱原来的电极间配对关系,使流液洞和上升道这段区域内的每个电极间都可导通,消除了无法进行电加热的区域,同时将熔化池下部的起动电极也接上发电机电源,对熔化池下部进行加热。流液洞和上升道区域内电极电流逐步升高,恢复供电后电熔窑也恢复正常生产,用这种方法解决长时间停电问题。
8.2.8电极和电极冷却水套
电熔窑使用氧化锡电极。这种电极在一定温度下,遇到还原性气体就会被还原。因此在烤窑过程中要保证每个电极的周围必须是氧化性气氛。烤窑时就要选好测点并经常检测窑内气体的含氧量。
当氧化锡电极被还原时,会冒出白烟,严重时会有金属锡淌下。此时应立即加大风量,做好电极周围通风,使之恢复氧化性气氛。然后检查。将可能被还原的电极全部拆下,严重还原的必须换新的,还原不严重的经修复后可再使用。
与电极直接相连的冷却水套。由于频繁停电,造成冷却水套多次断水。有时停电时间较长,使水套温度急剧升高。再上水时,若水流过大,会使灼热的水套受到急冷,造成冷却水套焊缝处产生裂纹,致使电极水套漏水。电极水套漏水后是无法进行焊接的。所以操作中尽量避免冷却水套断水。一旦停电,就应立即用备用发电机将冷却水送上,或接通自来水。如果冷却水套断水已有较长时间,上水时应先把每个水套的控制阀关上,待水过来后,再把控制阀慢慢打开,让水缓慢流入水套,再将控制阀开到一定程度。严禁大水流输入,造成灼热的冷却水套急冷。当冷却水套出现漏水现象时,要将冷却水的输入量控制在不发生汽化现象的最小程度上,以减小冷却水的压力,避免渗漏过多,流淌到耐火材料上造成炸裂。
8.2.9 更换电极
安装氧化锡电极的电熔窑运行两年后,因主电极受到玻璃液的严重侵蚀,通常需要更换,否则将影响玻璃液的熔制质量。
1.热换法:更换电极时,首先要放料。开始放料时如速度很慢,说明放料孔堵塞了,应疏通以加快放料。主电极完全暴露出来后即停止放料。拆卸电极时先把与电极相连的冷却水套取下、修补,更换银棒。上面的电极用千斤顶顶到熔化池内,用特制的夹子把顶出的电极从加料口取出,再换上新电极,重新加料、恢复生产。
2.冷换法:也可将窑内玻璃液全部放光,停炉,待窑体冷却后换上新电极,再重新点火、生产。
此页网址为:
相关文章