工程分类
更多>>![]() |
|
![]() |
|
![]() |
|
![]() |
|
![]() |
|
![]() |
|
![]() |
|
![]() |
|
![]() |
|
![]() |
|
![]() |
|
![]() |
|
![]() |
|
![]() |
|
![]() |
|
![]() |
|
![]() |
|
![]() |
|
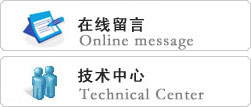
联系人:
电话:0511-88791451
手机:13951280541
邮箱:jfchen@ujs.edu.cn
地址:镇江市学府路80号
最新文章
您的位置:网站首页 > 最新文章全电熔窑的烤窑和运行——电熔窑的运行
8.3.1热顶电熔窑的运行
1.熔化特性
配合料如在火焰池窑中那样浮在玻璃液面上向前漂去。当然,希望熔化池液面上完全被配合料层所复盖,借此创造出一个如冷顶电熔窑的熔制条件,这可获得在单位熔化面积上输入最少的能量却得到****的热效率。但事实上这种状态难于实现,除非该熔化池处于它的****出料状态上。一般的情况是,在熔化池靠流液洞一端将暴露出一个面积变化着的半熔态的液面,如图6.2.2所示。这同电熔化的基本原理有关,也与保障质量而制定的熔制制度、熔制条件有关。
这些为保障质量而提出的基本要求如下:⑴原料的质量控制包括杂质含量、各批号的稳定、配料时的精确称量;⑵配合料混合的均匀性;⑶熔制条件的均匀一致,即每份配合料均获得等时等热的熔制过程;⑷玻璃必须达到最低的澄清温度。上述唯有(1)项与电熔窑的设计无关,而(2)(3)(4)三项都会受到熔窑设计与操作运行的影响。⑵项通常被认为只是一个与配合料的混合和输送系统有关的函数,但就电熔窑而言,并不是这样,如果电熔窑结构设计不合理,在熔化过程中会造成配合料的新的不均匀(见图6.2.2)。当配合料在玻璃液面上向前漂浮时,熔化过程也就开始了,但熔化过程只发生在配合料料层和玻璃液相接触的交界面处。当采用定位式加料机时,料堆在窑池内移动过程中,一旦某部分配合料发生沉降,将不会有新的配合料补充到该处。由于配合料是多种矿物原料及化工原料混合而成,而且它们只是物理掺合,并非化学结合,它们不可能同时全部熔化和结合成玻璃,只能是在不同温度下的熔化和化合。当配合料离开电熔窑的加料口后,低熔点反应物首先变为液相离开料层,随着热量的向上穿透,处于料层上部的低熔物亦成液相填塞到下部,而难熔物则维持到更高温度才熔化。这样,配合料与熔体的均匀度不断地遭到破坏。这种不均匀的熔体总是处在向下的对流中,因而常常引起灰泡、气泡、结石和硅氧质条纹。这说明了在这种型式的电熔窑内需要有强烈的对流以达到混合和均化玻璃的目的。
2.运行
操作运行同熔化特性一样重要,它同样会产生电熔窑控制和玻璃成型过程中的某些问题。当某熔化池完全为料层所复盖时,电熔窑的热损失在其整个运行范围内理论上均维持不变(图8.3.1A),料层各部分的单位面积热损失亦是均一的。事实上由于料毯厚度和玻璃温度的变动,热损失有变化,只是变化不大罢了。这些热损失在任一给定时间内都不是恒定的。
对于半冷顶电熔窑操作,输入功率的稍微偏高或偏低会造成料毯在熔化池内复盖率的变化,反之亦然(图8.3.1B)。料毯复盖状态的变化将显著地改变电熔窑的热损失和热平衡。譬如说,料层复盖率下降,会使玻璃液出现新的暴露表面,从而增加了玻璃液向炉顶的的热辐射。
如果要使玻璃熔制状态维持不变,那末增加了的能量损耗必然要通过增加输入能量来补充。否则,尽管整个熔化池内料毯缩小的面积是有限的,不确定的,但随着配合料熔化的增加(能量损耗随之增加),玻璃液本身被局部地冷却了,一旦在靠近流液洞的前部分出现玻璃液温度的下降,紧跟着在制品中会出现条纹、灰泡。所有这一切要求电熔窑操作者仔细和频繁地调节控制,要求电熔窑长期保持在极为稳定的产量上。
当电熔窑运行发生了上述情况时,正确操作却是同想像的相反。一般而论,能量损耗增多应增加输入能量来补偿。但增加的输入能量不可能局限在所需要的地方,而是整个熔化池的能量都要增加,这就导致料毯的进一步缩小、玻璃液面的进一步裸露、开始了恶性循环。正确的操作应减少能量的输入,降低玻璃液的温度,减缓熔化速率,重新建立适宜的料毯复盖层。
只有在很小的电熔窑内,用电阻的自动调节来操作,才能成功地应付上述情况,但这是以大幅度的功率输入和高的功率消耗为代价的。
3.调节
上述保障质量的第4项要求“玻璃必须达到最低澄清温度”。意味着操作人员为了维持料层处于某高复盖率水平时,不能无限制地减少能量输入、降低熔化温度。若要使复盖层稳定,半冷顶电熔窑事实上与冷顶电熔窑一样,调节是有限度的。若允许敞开液面调节平衡,那末100%的调节幅度也会是可能的。这种情况则要消耗极高功率。并且裸露的液面上存在着氧化还原反应,这就要求对应于不同的出料量应有不同的配合料组成。
8.3.2冷顶电熔窑的运行
这种类型的电熔窑几乎总是采用对称型的电源设计,图7.3.1、图7.3.2、图7.3.5是这些对称型的电源,它们可以是单相的也可以是两相或三相的。它们的形状可以是正方形的,也可以是长方形、园形或六角形的,以适应所用电源的类型。
对称型系统的选择,期望产生均匀的料层,以使整个熔化池玻璃液面上有一个尽可能均匀熔化的状况,使配合料在整个熔化池表面均匀地熔沉下去。如图7.2.3所示加料机具有如图8.3.2所示的配合料复盖图样、是一种三角形交迭的、不重合的加料方式。实际的加料要比图8.3.2图样宽,加料机在熔化池液面上“铺”的图案要复杂得多。
1.熔化特性
冷顶的电熔窑正如前面已经定义了的,其每一部分的配合料均在相应地方熔化,在熔化池的表面不发生水平移动,配合料的熔化是垂直进行的。冷顶炉与半冷顶炉间存在着明显的区别。冷顶炉熔化过程中配合料不断地、恒定地加入炉内,一层压着一层、一个部分压着一个部分。亦即总是由新加入的配合料去替代下面已熔化了的部分。依靠这种方式,在整个电熔窑表面达到一个熔化平衡状态,一个均匀一致的熔化过程。一旦建立上述熔化条件,电熔窑内的对流混合已不需要也不期望了。对于电熔窑的水平方向和垂直方向,可以设计出非常均匀的温度条件,图8.3.3是一台熔制钠钙玻璃的装有底插电极的冷顶炉实际温度分布图。这种均匀的温度状态是依赖于每根电极棒以及电极棒表面的低电流密度来实现的。当实现了这些均匀的温度状态时,接着就有垂直液流(Plag flow)出现,几乎不存在对流混合。
图8.3.4是一座日产300多吨、熔化面积27.9m2电熔窑运行时的“换料”情况。冷顶电熔窑的理论换料时间为42小时。在更换配合料41小时后,玻璃的组成开始变化,在其后的12小时内发生主要的变化,在最后的8小时内发生90%的变化。
2.运行
熔化池极深的冷顶电熔窑,其垂直方向的能量分布已分了区段,在较低的区段上出现了较高的温度后,不希望的对流将会发生;在低区段有较低的温度,可通过调节玻璃深度、电极高度、隔热条件等较好地实现,不存在增加输入能量的要求。对称的单区段的操作具有供电系统对称、平衡、冷料毯复盖等特点,控制极为简单。供电系统的任何一相都可代表其整体。玻璃液的电阻亦可很容易、很精确地测算。玻璃液的温度就可以重复地自由地调节。
对于自动电阻控制,操作者只须调节一下设定值掌握好料毯状况就可以了。当料毯厚度发生了变化,因热损失同时亦发生了某些相应的变化而获得所谓的“自补偿”,故出料量极少需要加以调节。
3.调节
为维持澄清所需的最低温度(前述保障玻璃质量四项基本要求之⑷项,限定了一座冷顶电熔窑的调节范围(调低程度)。欲使熔化池内料毯稳定,料毯的熔化速率与电熔窑的出料量之间必须精确地处于平衡状态。玻璃的最低澄清温度是冷顶电熔窑的调节极限(即8.2节中讲的翻转限turn-down limit)。电熔窑设计者可通过变更熔化池的尺寸来达到,玻璃工艺师可以通过调整料方来达到,电熔窑操作者则事实上对此无能为力。
此页网址为:
相关文章