工程分类
更多>>![]() |
|
![]() |
|
![]() |
|
![]() |
|
![]() |
|
![]() |
|
![]() |
|
![]() |
|
![]() |
|
![]() |
|
![]() |
|
![]() |
|
![]() |
|
![]() |
|
![]() |
|
![]() |
|
![]() |
|
![]() |
|
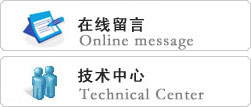
联系人:
电话:0511-88791451
手机:13951280541
邮箱:jfchen@ujs.edu.cn
地址:镇江市学府路80号
最新文章
您的位置:网站首页 > 最新文章全电熔窑的烤窑和运行——电熔窑的运行实例
例1 小型玻璃电熔窑的运行实践
某厂的小型电熔窑运转了两年三个月,进行了第一次冷修,现将其运转状况总结如下。该厂的产品为医用玻璃,玻璃料别为钠钙料和硬质料(透明玻璃的膨胀系数α=47×10-7,茶色玻璃的膨胀系数α=70×10-7),电熔窑的日产量为750—850Kg,换料困难。
1.概况
电熔窑的长宽高为2500×1600mm×2000mm,出料量1500kg/d,窑内玻璃容量约1000Kg。配合料每小时由熔化池上部加入,窑体分为熔化池和工作池,两者由流液洞连接。与玻璃液接触的部分全部使用电熔锆刚玉砖。熔化池安装有一对带水套的棒状钼电极。工作池由硅钼棒发热体加热,自动控制温度。在电熔砖外侧为耐火砖、保温砖和陶瓷纤维棉的保温结构,用有网眼铁皮包住,由拉索和拉杆紧固。电熔窑的操作工人对电窑炉完全没有经验。
2.供电和控制
电熔窑的钼电极和硅钼棒都使用单相供电。考虑工厂内其它用电设备的供电,使电源的三相平衡。
控制柜内设有变压器、可控硅单元、控制单元等,外部设有电压表、电流表、温度调节指示计等。控制柜长宽高1000mm×1000mm×2000mm。熔化池功率40Kw(60~100V,450~670A),工作池的功率60 Kw(30~120V,100~300A)。
3.电熔窑烤窑
⑴窑炉砌筑完后,用吸尘器将窑内的砖渣吸净,再用湿抹布擦净。⑵在熔化池放入200公斤碎玻璃。⑶升温由工作池设置硅钼棒加热,不用其它热源。由此,需要一定的时间,但对电熔砖来说这种方法比较好。⑷预先制成升温曲线,根据这个曲线调整硅钼棒的电功率。 ⑸窑内碎玻璃软化后开始继续加碎玻璃,玻璃液面达到电极位置以上时,插入电极并通电。⑹从硅钼棒通电到钼电极插入通电需要10天左右,到开始出料还需要两天左右。⑺虽然对窑内进行了很好的清扫,砖渣等也不可避免,开始流的玻璃全是碎玻璃,窑炉的情况也不好掌握,所以这时玻璃液质量往往达不到要求。要逐渐取出玻璃液,加入新原料,这样反复操作,以获得合格的玻璃液。⑻窑内玻璃液和外壳要接地,操作工人的工作部位要敷设橡胶垫,窑和控制柜周围应注意不要撒水。⑼为防止电极冷却水中断,一般不直接使用自来水,设置容量一吨左右的贮水池。使用循环泵供水。⑽每小时记录一次电压、电流、温度、配合料加入量、玻璃液取出量等,便于进行研究讨论,掌握好这些数据与玻璃质量的关系。因为是新设备,整理这些记录是一项重要的工作。
4.电熔窑的运行
⑴7月23日硅钼棒发热体开始通电升温,7月30日钼电极通电,至8月3日开始出料。
⑵最初的一个月,由于对窑炉和玻璃的关系掌握不好,出现了一些差错,产生了少量气泡、条纹和结石等,以后便比较稳定了。
⑶窑炉后期因耐火材料结石增加。于两年后的10月18日停止使用,对熔化池进行冷修后,于10月25日重新使用,10月25日硅钼棒通电,11月1日开始出料。
⑷熔化池上面覆盖着一层配合料(冷料层),这个冷料层有一定厚度。有时配合料层和玻璃间会造成空壳。配合料随玻璃液取出同步下降是非常重要的。采用小锹每隔一定时间均匀加料一次。
⑸与一般的大型池窑不同,电熔窑的保温很好。考虑窑炉的寿命为两年,即两年仅对熔化池进行冷修。工作池预计使用四年。
⑹如果碎玻璃块度过大,将会扰乱冷料层。应经常注意碎玻璃的块度。
⑺钼电极的尺寸φ32mm×1000mm(一面有凹螺纹),电流密度为1.7A/cm2。电极的冷却水绝对不能断。每支电极的冷却水用量相当于10—20升/小时,出水温度为40—60℃,温度过高容易使水套结水垢。在出水处设置热电偶,也可按装报警装置。
电极的电流相同,电极间电压上升,可以判断电极的消耗。这时将预备的电极部分向里推。根据概算两年三个月电极长度消耗约50cm,相对于一公斤玻璃消耗约0.04克钼熔入玻璃中。
⑻熔化池温度根据实测最高为1370—1400℃,根据玻璃液面的高低有一定温度变化。
⑼工作池由硅钼棒发热体加热,自动控制工作温度。下午成型完后,温度可以下降,降温程度约100℃左右,这时只需白天用电量的二分之一就可以维持这个温度。为达到次日早晨八点的成型温度,在早晨六点左右开始升温。制作大的制品时,工作池挑料口开的时间长,可以使用气动门等自动启闭,抑制散热。
⑽窑墙外表面温度,根据部位不同在60—110℃左右,窑上部温度150—200℃。
⑾冷料毯吸收了挥发性原料的挥发成分,减少了挥发性原料的用量。
⑿用坩埚窑时,坩埚底部玻璃液几乎不能使用,而电熔窑是一边取料一边加料,所以成型时间内能够使用全部正常的玻璃液。
⒀上、下午玻璃液面高度没有很大差异,所以挑料人员在取料时铁杆的握法也无大变化,可提高工作效率。
⒁用坩埚窑时每天要刮四次料,而电熔窑几乎不用刮料。
⒂如果事前采取的措施得当可以取得好效果。例如,下午因生产大制品,需要增加出料量,可在上午适当增加电力,增加原料投入量。增加的用电量大小和增加的投料量多少,根据玻璃质量和制品大小不同而定。
⒃可以加班成型,如每天加班两个小时,可连续一个月。
⒄电熔窑占地面积小,在较小的场地也能有效使用。当然也不需要换坩埚,这是很大的优点。
⒅根据玻璃组成和产品质量要求制定操作说明,但在玻璃厂一般难于遵守,有时产生一些问题。另外,小规模的玻璃厂出料量不定,不能长时期制作同一品种的制品。因此,每公斤玻璃出料量相对应的用电量有一定变化。
⒆电熔窑也可更换玻璃液,但由于其结构、形状使换料不方便,所以没有进行。
⒇熔化池、工作部的电压、电流和其它数值列于表8.4.1。
表8.4.1
日期 |
熔化池 |
工作部 |
出料 量Kg |
电耗 Kw/Kg | ||||||||||
电压 V |
电流 A |
电量 Kw |
电 阻 Ω |
温 度 ℃ |
电压V |
电流A |
电量 Kw |
温度℃ | ||||||
白天 |
晚上 |
白天 |
晚上 |
白天 |
晚上 | |||||||||
81.9.17 |
50 |
500 |
600 |
0.10 |
1110 |
103 |
60 |
285 |
190 |
488 |
1170 |
1070 |
460 |
2.36 |
81.9.23 |
52 |
484 |
604 |
0.11 |
1020 |
80 |
55 |
270 |
185 |
381 |
1010 |
1000 |
260 |
3.73 |
81.1023 |
53 |
524 |
667 |
0.10 |
1110 |
90 |
65 |
285 |
220 |
477 |
1150 |
1080 |
440 |
2.60 |
82.1.28 |
60 |
490 |
706 |
0.12 |
1110 |
104 |
60 |
285 |
210 |
506 |
1150 |
1080 |
360 |
3.36 |
82.3.10 |
61 |
470 |
686 |
0.13 |
1140 |
105 |
75 |
285 |
220 |
556 |
1150 |
1080 |
440 |
2.80 |
例2 小型硼硅酸盐玻璃电熔窑操作和换料经验总结
某厂开发了一种熔化硼硅酸盐玻璃的冷顶的全电熔窑。
1.电熔窑的参数
图8.4.1是电熔窑的立面图。池窑包括熔化池、流液洞、上升道和料道。熔化池、流液洞和上升道是由电流通电加热的,料道是通过硅碳棒辐射加热的。电熔窑的参数汇总在表8.4.2中。
表8.4.2 电熔窑的参数
玻璃品种: |
硼硅酸盐玻璃 | |
玻璃日产量t/d |
1 | |
料毯厚度 |
5—15mm | |
碎玻璃量 |
10-75% | |
电极寿命 |
半年--一年 | |
玻璃比重g/cm3 |
2.28 | |
玻璃管的直径 |
2—25mm | |
加料方式 |
每20分钟人工加料一次 | |
料毯温度℃ |
20—600 | |
温控方式 |
可控硅调节 | |
电极规格 |
4支长450mm直径F20mm。 5支长690mm直径F20mm。 5支长800mm直径F32mm | |
熔 化 池 |
面积(m2) |
0.48 |
容积(m3) |
0.53 | |
玻璃容量(t) |
1.2 | |
流 液 洞 |
面积(m2) |
0.26 |
容积(m3) |
0.052 | |
玻璃容量(t) |
0.12 | |
上 升 道 |
面积(m2) |
0.10 |
容积(m3) |
0.11 | |
玻璃容量(t) |
0.25 | |
料 道 |
面积(m2) |
0.55 |
容积(m3) |
0.17 | |
玻璃容量(t) |
0.38 | |
长度mm |
4300 |
2.电熔窑的运转
熔化池的能耗为2Kwh/Kg玻璃;流液洞和上升道为0.6 Kwh/Kg玻璃,而料道为0.3 Kwh/Kg玻璃。料道是辐射加热。熔化池部分的能耗占75%。熔化温度为1450—1600℃。熔化池和上升道的温度是用热电偶来测量的,插入深度为70cm,温度分布如图8.4.2。电极的消耗与电阻变化如图8.4.3。
在电熔窑中,换料大约持续5天到10天(根据质量要求)。图8.4.4是换料过程与电阻变化的关系,电阻****值是由于暂时的温度下降造成的。第一个电极对在两天后,第二个电极对在2.5天后,第三个电极对在3天后电阻值不再变化。图8.4.5表示的是软质硼硅酸盐玻璃(与钼熔接的玻璃,含有ZnO)转换成硬质硼硅酸盐玻璃(与钨熔接的玻璃,含有BaO)的过程中,ZnO、BaO含量的变化与电极间电压变化的关系。玻璃组成大约要在5—10天后才能达到最终值。旧玻璃的痕迹要延续15天。与火焰窑熔化硼硅酸盐玻璃相比,电熔仅出现微小的玻璃缺陷,可达到较大的产量,可以达到较好的澄清。关于玻璃的质量和产量可从表8.4.3数据得出:
表8.4.3
火焰窑 |
电熔窑 | |
气泡(个/Kg玻璃) |
2000 |
20—100 |
图8.4.4 换料时最初三对电极的电阻变化
图8.4.5换料时电压的变化情况
成品率 |
70% |
90% |
例3 某大型玻璃电熔窑的运行情况
某厂一座生产器皿玻璃的冷顶电熔窑停产检修以观察耐火材料和电极的侵蚀情况。下面总结的是该电熔窑第一个窑期的运行情况,包括玻璃的质量、成品率、电熔窑的热效率、耐火材料和电极的寿命等,并涉及某些设计参数。
1.电熔窑的运行情况
该窑运行了1133天。该窑设计的生产能力是141T/d,在整个窑期内熔化钠—钙无色玻璃,制造日用器皿,该窑期的数据综合如下:生产玻璃总量 142406吨,电能总消耗量123548081Kwh,平均每吨玻璃电能消耗量867 Kwh /吨(80%粉料和20%碎玻璃),玻璃理论耗热量1.11 Kwh /公斤,熔化热效率 78%,最小出料量117.1T/d,****出料量150.5T/d,全窑期平均出料量125.7T/d,第六个月平均出料量134.3T/d,平均电耗838.1 Kwh /吨。第三十五个月平均出料量132.6T/d,平均电耗883.1 Kwh /T。整个窑期内玻璃质量比工厂中其它火焰窑显著提高,有代表性的气泡数每公斤只有170~180个,成品率为90%,而厂里其它窑生产类似产品时成品率只能达到85%。
熔化池呈矩形,产量可达250吨/日,熔化面积58米2。玻璃液深度为1.5米。在每个角布置六支水平电极,由于各排电极间几何因素不同,因此底排电极引入负荷的37.5%,而上面两排分别引入31%和31.5%。在37个月的窑期内,电极的侵蚀是轻微的,与垂直安装电极所预料的侵蚀情况相似。
在这座窑投产的早期,取这座窑中生产的玻璃试样进行钼含量的测试,结果MoO3含量为10ppm。在整个窑期内,通过每根电极的电流和电极之间电流的平衡都没有显著的变化。为了确保电极的侵蚀均匀,每两个月把电极旋转180°。
在37个月中,两次把电极向窑内推进150mm。窑末期放玻璃水后留在窑内的底插电极,整根电极没有弯曲,水平插入的电极从池壁到电极端部,其直径是均匀的。
2.料层
整个液面上料层的厚度基本上是均匀的,料层像毯子一样浮在液面上,在窑中心部分的料层厚度比池壁附近的料层厚度大,靠近侧墙处厚度为150—200毫米,在窑中心处为600—750毫米,厚度与出料量有关。
生料的密度大约只有熔融玻璃密度的一半,而且靠近电极的周围是能量释放的****区域,能量的释放向着窑中心区域逐渐衰减。这两种现象,是造成料层厚度变化的主要原因。但是,上述厚度差对下层玻璃液的澄清没有什么有害的影响,较大部分的功率是由澄清池下部的电极引入的。
3.耐火材料侵蚀
37个月后窑内放出了玻璃水,检查窑内耐火材料的侵蚀情况。侧墙的侵蚀与火焰窑是一致的,液面线附近侵蚀****,而且在熔化池整个深度上侵蚀是均匀的。熔化池侧墙的剩余厚度在100到150mm之间变化,在整个窑期内原来300mm厚的耐火材料被侵蚀掉150到200mm。
在熔化池,除流液洞盖板砖是用含铬的ACZS砖外,其余均用300mm厚的含ZrO241%的耐火材料。通常,这些部位的耐火材料侵蚀是最严重的,但在这座窑上只有75~100mm被侵蚀掉,还剩余200~225mm。这些砖突出于毗连的锆英石砖,情况良好,而且砖缝处也只有轻微的侵蚀。
研究玻璃液中铬含量,是不是流液洞处的耐火材料带到玻璃中的。分析了该厂没有含铬耐火材料的烧天然气火焰窑中的玻璃成分。结果是出人意料,燃气火焰窑中的玻璃含有30ppm的铬,而电熔窑的玻璃却只含有22ppm的铬。可能这种差别是分析过程本身引起的。也可能是硅砂中的固有微量元素,也可能是由绿色碎玻璃带入的。总之,不管玻璃中的铬来自何方,总不会造成玻璃的着色问题。
4.电缆线与电器
电熔窑由一台三相到两相的负荷为5800KVA的 斯柯特(Scott)变压器供电,加料机如图7.2.2所示。电缆线、电器、变压器、加料机都完好。在第二窑期不需要进行任何更换。
5.冷修
在电熔窑冷却后的十二天内完成了拆窑和再建的工作。每天10小时一班作业,从放玻璃水到再生产瓶子的时间是25天。
例4 T型电熔窑的运行
某厂一座铅晶质玻璃电熔窑,每天熔制3.5~6.0T中铅晶质玻璃,熔化池由两个长方形池组成,熔化面积2.3m2的熔化池直接位于较小的澄清池以上,结构呈T型。熔化池两侧台阶上安装氧化锡电极,每排电极均由位于同一水平面的电极组成,称为主电极。主电极由单相调压变压器供电。熔化率为2.6T/m2·d,单耗为0.95Kwh/kg玻璃。电熔窑设计熔化能力为3.5~6T/d。
氧化锡电极寿命为2年,窑炉寿命为4年,在电熔窑运行周期内更换一次氧化锡电极。若电熔窑在运行中停电次数多,造成电极砖孔爆裂变形,则无法更换主电极。
若将圆柱形电极改为砖型(如195×195×95mm)电极,安装在熔化池两侧池墙上,不仅可保持电极电流在使用周期内基本不变,还便于电极更换。
若熔化量较大,熔化池宜改为六角形以解决单相供电造成的电网负荷不平衡问题。
1.操作过程中发现的问题和解决措施。
电熔窑运行伊始,决定采用全自动控制。由于在电熔窑中较难实行恒温控制,所以滞后现象非常严重,系统中各部位的参数波动太大,输入功率在190~240kW间波动,电阻在0.190~0.209Ω之间波动,温度控制器(玻璃熔化池高温计GBP)显示值在1330~1374℃之间波动。这样不仅增加能耗,还使玻璃液质量不够稳定。所以某厂决定改用手动调节来操作。方法是根据GBP显示的温度来调节控制输入功率的大小。从实际运行情况来看,用手动调节来操作不仅可以保证玻璃质量,而且可以加强操作工人的责任心,同时减少了耗电量。
2.玻璃熔化池高温计问题
玻璃熔化池高温计(GBP)直接水平插入玻璃中,用于测量熔化池中玻璃液的温度,同时可利用它输出的信号,进行熔化池输入功率的自动控制。由于窑体渗漏玻璃液的原因,致使GBP高温计在电熔窑运行一年后就被折断。玻璃液侵蚀到GBP高温计的中心,与热电偶丝接触,GBP失灵。既不能用其显示温度,更不能用其进行自动控制。且GBP高温计是水平直接插在玻璃液中,如果更换,必须放掉一部分玻璃液,必然影响生产。根据以往的操作经验和热平衡原理,决定采用熔化池输入功率控制,并辅以耗电量、电阻值、流液洞温度和电极电流等数据做参考,使系统得以正常运行。这样,在GBP高温计损坏以后,虽然不知道熔化池中玻璃液的温度,由于采用了上述方法,耗电量和玻璃液质量均与以前大致相同,保证了正常生产。
用不同控制方法操作时,一些主要数据变化情况见表8.4.4。
表8.4.4 不同控制方法操作参数的变化
控制方式 指标 |
自动控制 |
根据GBP显示 手动控制 |
功率控制 |
功率(Kw) |
190-240 |
200-220 |
200-220 |
GBP显示(℃) |
1330-1374 |
1330-1350 |
无显示 |
电阻(Ω) |
0.190-0.209 |
0.195-0.205 |
0.250-0.295* |
耗电量(Kwh/d) |
5380-5550 |
4800-5280 |
5130-5240 |
流液洞温度(℃) |
1102-1125 |
1084-1132 |
1110-1160 |
上升道温度(℃) |
938-989 |
856-961 |
920-970 |
* 采用功率控制时,电熔窑已运行一年半,氧化锡电极已受到很大的侵蚀,致使被测出的电阻值由开始运行时的0.190Ω增加到当时的0.290Ω。
3.加料问题
按工艺要求,配合料和一定颗粒度的碎玻璃必须是平坦而均匀地撒布在熔化池内的冷料毯上。但开始提供的KTGM41型加料机根本达不到此项工艺要求,只能将配合料呈两条带状分布到熔化池表面。这样,熔化池表面就不完全是冷料层,而是暴露出部分灼热的玻璃液,使得上部空间变热。不仅增加了能耗,还可能烧坏加料机。更严重的是配合料和碎玻璃过于集中,使得熔化池上面局部生料层过厚,在后续配合料的推动下,一些尚未熔化好的配合料就会随生产流很快通过高温区,使玻璃液质量变坏。同时造成电流分布不均,不利于熔化。为了保住冷顶,防止加料机烧坏,不得不多加料,造成不必要的浪费。
为了实现均匀加料,采用的是人工辅助加料方法。
此页网址为:
相关文章