工程分类
更多>>![]() |
|
![]() |
|
![]() |
|
![]() |
|
![]() |
|
![]() |
|
![]() |
|
![]() |
|
![]() |
|
![]() |
|
![]() |
|
![]() |
|
![]() |
|
![]() |
|
![]() |
|
![]() |
|
![]() |
|
![]() |
|
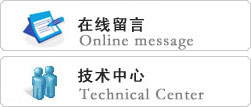
联系人:
电话:0511-88791451
手机:13951280541
邮箱:jfchen@ujs.edu.cn
地址:镇江市学府路80号
最新文章
您的位置:网站首页 > 最新文章全电熔窑的典型实例
9.1使用硅钼棒间接加热的电热坩埚窑
例1.双坩埚室的电热坩埚窑
在坩埚周围垂直按装硅钼棒发热体。该窑分为两个坩埚室,在一个室内放一个坩埚(容量225Kg),独立操作,温度分别自动控制。在窑下部设置玻璃液流出孔。窑炉的长宽高为2630mm×1530mm×1920mm。两室用电量:60Kw(200V×300A),控制柜长宽高为1500mm×1000mm×2000mm。开始时使用动断式控制方式,后来改为可控硅控制。筑炉后与坩埚窑一样先放入坩埚。按预定曲线开始升温。六日后开始出料。日常操作与坩埚窑无多大变化。因是相对独立的,相邻的坩埚状态无需考虑。坩锅窑的出料量650—750Kg/d,熔制用量较少和品种变动较多的透明和茶色硬玻璃
最初,因温度调节有误,造成了坩埚破损。坩埚预热使用另一侧不用的窑,使其温度下降后放入坩埚。即轮换使用,坩埚寿命和原来差不多。
玻璃质量和坩埚窑一样,但改善了操作环境,使操作容易进行了。因为是间接加热,每公斤玻璃液耗电量比直接通电的电熔窑多。
表9.1.1所示的数据,由于加料时间、玻璃料别不同,成型时的数据有一定差异。
表9.1.1
日期 |
玻璃品种 |
温度℃ |
电压V |
电流A |
功率Kw |
电耗Kw/Kg |
81.11.25 |
茶色硬玻璃 |
1310-1450 |
110-170 |
203-280 |
22.3-47.6 |
4.5 |
82.9.3 |
硬玻璃 |
1370-1490 |
120-170 |
215-280 |
32.2-47.6 |
6.0 |
82.9.21 |
普玻 |
1200-1480 |
135-175 |
225-280 |
31.1-49.3 |
4.0 |
例2 熔制铅晶质玻璃的电热坩埚窑
根据坩埚窑条件不同,开口坩埚直径在500—1300mm范围内,高度在600~750mm范围内。由于多坩埚窑内各坩埚间存在温差(15℃左右),致使玻璃液质量受到影响,所以西德现已淘汰了多坩埚窑。单坩埚窑(如图9.1.1所示)和双坩埚窑内温度较易控制,玻璃液质量相对也高一些,故仍用于生产特种玻璃。标准开口坩埚直径为1200mm,高度为650mm,容积为350升。以玻璃液比重2.8g/cm3计算,则一缸玻璃液重980Kg,实际可生产780Kg的玻璃制品。
考虑到熔制过程中PbO的挥发量,原料配方一般要求含PbO量为26~28%,熟料加入量为40%左右。根据窑炉及原料的具体情况在上述范围内调整,以保证成品含PbO量为24%。
9.2 熔制钠钙玻璃的全电熔窑
例1 日产6吨钠钙玻璃全电熔窑
(1)玻璃的组成
SiO273.74 Al2O31.25 B2O31.1 CaO4.71 Na2O15.65 K2O0.15 MgO3.17
(2)膨胀系数(0—300℃)87.3*10-7/℃
(3)软化点 683 ℃
(4)电熔窑的结构如图9.2.1,1—水套;2—电极;3—加料口;4—喷嘴;5—排烟气;6—喷嘴;7—电热元件;8—热电偶;9—测温孔;10—电极;11—熔化池;12—水套;13—工作池;14—电极;15—料道。
表9.2.1 电熔窑的技术经济指标
熔 化 池 |
面积 m2 |
1.2 |
深度 m |
1.2 | |
熔化率 t/m2.d |
3.0-5.0 | |
输入功率 Kw |
160-180 | |
熔化玻璃单耗Kwh/Kg璃液 |
1.19-1.44 | |
空间温度 ℃ |
160-200 | |
玻璃液温度 ℃ |
1450 | |
工 作 池 |
面积 m2 |
0.36 |
输入功率 Kw |
28.0 | |
单耗 Kwh/Kg璃液 |
0.23 | |
空间温度℃ |
1200 |
(5)该窑炉的热效率44%.
(6)该电熔窑结构简单,砌炉仅用10天,烤窑仅用6天。
例2 日产0.5T白料眼镜玻璃的小型电熔窑
1.电熔窑的结构
该窑采用立式结构,窑炉由熔化池、流液洞、上升道及料道组成。熔化池采用上下两对钼电极,分两层加热。上升道采用一对钼电极,料道采用硅钼棒辐射加热,其结构见图9.2.2。
在熔化池顶部装有两个煤气喷嘴,供电熔窑启动时加热用,以保证电熔窑在1000℃左右时电极可以顺利通电。熔化池和上升道均采用电熔锆刚玉砖(含ZrO233%),砌筑时电熔砖的浇铸口向外。料道采用烧结锆刚玉砖,炉顶采用高铝砖。池墙顶部采用2cm厚的陶瓷纤维棉进行保温,池底不保温。
2.技术指标见表9.2.2
表9.2.2
出料量t/d |
0.5 | |
****出料量t/d |
0.84 | |
熔化率t/m2·d |
1 | |
玻璃品种 |
钠钙玻璃(白料眼镜片) | |
玻璃比重t/m3 |
2.5 | |
能耗(包括料道) Kwh/Kg玻璃 |
3.2 | |
面 积 (m2) |
熔化池, |
0.49 |
流液洞 |
0.045 | |
上升道 |
0.09 | |
供料道 |
0.2757 | |
玻璃液流经长度m |
3.705 | |
钼电极 |
φ37mm×1000mm |
四根 |
φ32mm×800mm |
二根 | |
电流调节 |
手动 | |
电极间电压V |
80 | |
加料 |
加料次数 |
每20分钟人工加料一次 |
碎玻璃 |
30% | |
料毯层厚度 |
~10cm | |
加料空 间温度 |
冷炉顶 |
300℃<T℃<400℃ |
热炉顶 |
1150℃<T℃<1300℃ |
3.供电
每对电极采用100kw单相电源调压变压器进行调节控制。次级侧有两组线圈。并联接法时电压100V,电流为1000A。串联接法时电压200V,电流为500A。料道采用50Kw调压变压器进行控制(见图9.2.3)。供电分四组、熔化池上下两层为2组,上升道为一组,料道为一组。
4.电极和电极水套
使用国产钼作为电极,其化学成份如下:Mo>99.9% C< 0.004% Fe0.003% Cr<0.003% Al<0.003% Mg<0.003% Si<0.001% Ca<0.01% N2<0.0026% O2 0.015% 。
整个电熔窑共六根钼棒,总重量为58.3公斤。熔化池4根钼电极损耗量为31.9g/d,上升道二根钼电极损耗为4.0g/d,电极顶部的蚀损较根部大,整个电极外表面损耗程度较均匀(见图9.2.4和表9.2.3)。
表9.2.3 钼电极在熔化池及上升道重量损失测定
电极位置 |
使用时间 |
使用前的 重量(Kg) |
使用后的 重量(Kg) |
消耗的 重量(Kg) |
平均每天消耗 的重量(Kg) |
熔化池 |
47天 |
10.84 |
10.45 |
0.39 |
0.0796 |
上升道 |
6.30 |
6.20 |
0.10 |
0.002 |
水套采用1Cr18Ni9Ti不锈钢,其结构见图2.2.28 。顶端为电极塞头,未端有进水管通冷却水冷却电极。电极水套盖内采用“O”型密封圈,在电极安装好后,将盖用螺纹上紧,使冷却水密封不致渗出。
电极冷却水使用软化水冷却电极。电极水冷却套在电熔窑炉墙安装位置,见图9.2.5。电极塞头距池墙砖内表面60~100mm。由熔炉内取出钼电极观察,电极根部被玻璃密封良好。钼电极的冷却热损失,和冷却水耗用量数据见表9.2.4。
表9.2.4 钼电极水冷套的热损失和用水量
部位 |
电极冷却水带走的热量(Kw/h) |
冷却水量(Kg/h) |
熔化池 |
2.7-2.85 |
100-120 |
上升道 |
2.2-2.35 |
100-120 |
5.电熔窑的烤窑
利用窑顶的煤气喷嘴升温8天,至1300℃左右开始加碎玻璃。当玻璃料液面升至下层电极位置时,将电极插入。当玻璃液将电极盖没时通电;此时玻璃液温度较低,电压相当高,可以输入一定的能量,使碎玻璃迅速熔化。当玻璃液升至上层电极位置时,插入上层电极通电。
6.电熔窑功率消耗
电熔窑调整正常后进行电工参数的测定,试验时出料量分别为300Kg/d、500 Kg/d、850 Kg/d,玻璃质量在检验后,气泡情况差别不大。电熔窑的熔化率和单耗见表9.2.5。
表9.2.5 0.5 m 2电熔窑熔化率及单耗
出料量(t/d) |
300 |
500 |
850 |
熔化率(t/m2.d) |
0.6 |
1 |
1.7 |
电熔窑功率(Kw) |
105-115 |
105-115 |
105-115 |
Kwh/Kg玻璃(包括料道) |
8.4-9.2 |
5.1-5.5 |
3.0-3.3 |
7.电熔窑炉温的测定
在电熔窑正常操作时,采用2 m长带刚玉保护套的铂铑热电偶插在熔化池中心,由上而下逐点进行玻璃液温度的测定,结果见图9.2.6。由图中可看出,熔化池热点处于上层和下层电极中间;出料量大(每天出料量850Kg),则热点向下移,上层玻璃液温度降低。
电熔窑出料量在0.5t/d时,形成热炉顶,其空间温度一般为1100℃到1300℃。在电熔窑相同的功率下,出料量增至0.85t/d时,形成冷炉顶,其空间温度一般在400~500℃之间。在每30分钟 一次的人工加料周期中,温度变化情况见图9.2.7。
冷炉顶形成后,熔炉上部温度低,热损失减少配合料中挥发物损失量亦相应减少。
8.玻璃熔制质量
该电熔窑在尚未采用可控硅恒流控制以及料液面自动控制的情况下,所得玻璃的质量大都保持在气泡200个/公斤玻璃的较好水平。气泡数量检验结果见图9.2.8。
9.经过热工测定、热平衡计算,该电熔窑的热效率为25%,炉壁加热散热占46.3%,冷却水热损失18.7%。电耗为2.752Kcal/Kg玻璃( 3.2Kwh/Kg玻璃)。
例3 日产3吨灯泡玻璃的全电熔窑炉
日产3吨全电熔窑运行正常,熔化率3T/d·m2,当加料量和出料量达平衡时,熔化池能形成冷炉顶。熔化每公斤玻璃耗电1.4度。玻璃的膨胀系数能与灯芯玻璃相匹配,白度高,玻璃光泽好,明亮。该电熔窑的熔化面积1.0M2 , 澄清温度1400~1420℃(在四支电极中心位置),并形成冷炉顶(最低270℃),经两个月小型电熔窑运行实验证实,玻璃的熔化质量良好,玻璃液对钼电极的侵蚀不明显。
1.玻璃的基础配方见表1.1.4第NO15号,玻璃的电阻率—温度曲线见图1.1.17第NO15号曲线。熔化温度根据沃尔富(B.M.VOLF)熔化温度经验常数τ的计算约为1380~1400℃。玻璃澄清温度根据高温粘度(旋转法)测定结果(表9.2.6)绘制的粘度—温度曲线,外推法取得澄清温度(logη=2),约为1450℃。
2.澄清剂添加的范围:组合澄清剂采用CeO2、NaNO3、Sb2O3、NaCl。与原火焰窑生产配方比较,取消了白砒与MnO2。组合澄清剂的组成:氧化铈0.1~0.3,三氧化二锑(0.1~0.3%),硝酸钠2.07~2.77%, NaCl 1.88~3.76%。电熔窑配方与国外熔化钠钙硅玻璃允许用量(Sb2O3 0.4%,NaCl 0.1%,NaNO3 0.27%) 比较,NaCl与NaNO3均偏高,从取样检验结果(含有气泡,条纹,结石的废品率为5~15%)表明,澄清效果良好。比火焰窑成品率提高10~15%。
3.配合料制备及配合料均匀度的影响:每付料以100公斤计算,原料按照配方称量后倒入圆筒混料机,机械混合20分钟。每付料取样,用滴定方法测定配合料均匀度(90~98%)。
配合料的均匀度最低90%,最高98.51%,无规则波动。对澄清效果无直接规律性的影响。但对于玻璃组成的均匀性与稳定性有一定的影响。配合料均匀度的不稳定,是造成熔化玻璃组成不稳定一个因素。
表9.2.6
粘度(logh) |
4.1 |
3.63 |
3.14 |
2.90 |
2.65 |
2.44 |
温度(℃) |
1019 |
1092 |
1181 |
1234 |
1292 |
1350 |
表9.2.7
电阻率(W.cm) |
9.09 |
7.30 |
6.67 |
5.65 |
5.181 |
温度(℃) |
1150 |
1200 |
1250 |
1300 |
1350 |
4.熔化池温度分布对玻璃熔化的影响
电熔窑人工加料。粉料与熟料比例各为50%。熟料在炉前称量与粉料混合,用铁锹投入炉内。加料均匀散开。间隔30分钟一次。换料到位后分三个阶段进行试验。每个阶段的出料量与电工参数列入表9.2.7。熔化池温度的分布与电极之间玻璃液中电力线的分布一致,因此电极周围温度最高。热电偶浸入玻璃液内只有10cm,并非实际的最高温度,因此只作参考温度。在熔化过程中以控制功率为主,并在稳压情况调节电流。
工作池出料方式以放料为主,仅少量人工吹泡壳取样。各阶段工作池内温度控制在1050℃。
表9.2.7
试验周期 |
天数 |
日出料量 (Kg) |
熔化池功率 (KVA) |
耗电量 (Kwh/Kg玻璃) |
第一阶段 |
20 |
400 |
91.87 |
5.51 |
第二阶段 |
5 |
800 |
86.56 |
2.59 |
第三阶段 |
7 |
1200 |
90.30 |
1.81 |
玻璃取样结果表明,第3阶段(1.2t/d)玻璃的熔化********(成品率90~95%).。熔化池炉温纵深方向实测结果,最高温度达到1418℃,第2阶段为1386℃。同时随着冷炉顶的形成,减少玻璃液面散热,使高温区域上移,并且使高温区拉长,使玻璃熔融体有更长时间进行澄清。
图9.2.9 全电熔窑熔化池纵深方向温度分布(四支电极中心点)
5.全电熔窑工艺技术参数
⑴换料到位后,每个阶段在熔化池(于四支电极的中心)用铂铑热电偶测定池内纵向温度分布,池深—温度曲线示于图9.2.9。曲线1—出料量528kg/24h(热炉顶);曲线2—出料量1050kg/24h;曲线3—出料量1584kg/24h(全冷炉顶)
⑵不同出料量时,工作池玻璃液内温度与空间温度变化曲线示于图9.2.10。1-熔化池空间温度;2-工作池空间温度;3-工作池内温度。
⑶换料到位后,每天取样(工作池) 测定玻璃化学组成中主要成分(SiO2 , Na2O%),结果列入表9.2.8。
⑷ 不同试验周期中,由工作池人工挑料吹泡(灯泡壳),每天20只,按企业标准检验(合格率%),其结果列入表9.2.9。
⑸ 通过测定玻璃中钼含量判断钼电极损耗。于试验周期内,熔化玻璃液19.6t ,最后取样测定结果为0.02% Mo。电极材料总的耗量大约3.92Kg,熔化池两对电极,平均每支电极损耗为0.98Kg。如将工作池电极计算在内,则每支平均损耗为0.65Kg。
表9.2.8 各阶段玻璃取样分析结果
日期 |
SiO2 |
Al2O3 |
B2O3 |
CaO |
MgO |
Na2O |
K2O |
10.22 |
73.12 |
1.44 |
0.86 |
5.0 |
2.84 |
14.77 |
1.17 |
10.29 |
73.92 |
14.84 | |||||
10.31 |
73.36 |
15.62 | |||||
11.1 |
73.24 |
1.28 |
1.0 |
4.71 |
3.17 |
15.80 |
表9.2.9
编号 |
合格数 |
合格率% |
编号 |
合格数 |
合格率% |
10.18 |
9 |
45 |
10.31 |
19 |
95 |
10.19 |
13 |
66.5 |
11.1 |
19 |
95 |
10.25 |
14 |
73.3 |
11.2 |
19 |
95 |
10.27 |
15 |
75 |
11.3 |
17 |
85 |
10.28 |
17 |
85 |
11.5 |
17 |
85 |
例4 日产6吨灯泡玻璃的电熔窑
1.电熔窑的结构设计及窑炉的砌筑
该电熔窑采用六角型的窑型,熔化面积2.6m2,池深1.8m,日产量6.5吨左右。窑炉内衬全部采用AZS36号电熔锆刚玉砖,电极砖和流液洞砖则采用AZS 41号电熔锆刚玉砖。池壁保温层的厚度为452 mm, 在池壁内衬与保温层之间用10mm厚的锆质捣打料捣实。池底保温层的厚度为65×8 mm, 保温砖之间砌有粘土砖胁条用来承重,上面铺上10mm厚锆质捣打料,然后铺上高岭土大砖, 高岭土大砖之间加锁砖。胸墙内壁用粘土砖砌筑 ,外侧池壁保温层的厚度为113×4 mm.炉顶采用吊平碹结构, 吊平碹采用优质粘土砖。
2.电熔窑的电极布置、结构和冷却方式
该电熔窑布置了两层钼电极,下层每一面配有一支电极(总共三支电极)下层电极的直径为50mm, 电极插入窑内200 mm。 上层每一面配有两支电极(总共六支电极),上层电极的直径为80mm, 电极插入窑内250 mm,电极后部车有母螺纹,便于连接新的钼棒。钼电极采用直接水冷方式进行冷却, 配有循环水泵(水池)、自来水供水、冷却水塔三套独立的供水系统。
上升道和料道(含料盆)电极的结构是复合式电极,与玻璃液接触的部分是钼棒,引电部分是耐热钢,不进行任何的强制冷却。
3.电熔窑的供电、控制、电工参数及耗电量
采用的是三相磁性调压器平衡供电,上升道和料道采用两台单相磁性调压器供电。控制系统采用的是恒温恒流控制。
下层电极供电变压器设计功率为100KVA,该变压器的次级端有六个头,可以根据实际运行情况采用三角形接法或星形接法,两种接法的输出电压相差1.732倍(相应的输出电流也相差1.732倍)。这样可以节省投资费用,提高功率因素。实际的运行电压50V, 运行电流500A. 实际运行功率大概在50KVA.
上层电极采用315KVA的变压器供电,变压器的次级端同样有六个头.实际的运行电压70V, 运行电流2000A. 实际运行功率大概在240KVA.
上升道采用40KVA单相磁性调压器供电,该变压器的次级端有六个抽头,可以根据实际运行情况改变抽头,也是为了节省投资费用,提高功率因素.实际的运行电压50V, 运行电流100A. 实际运行功率大概在5KVA.
料道采用20KVV单相磁性调压器供电,该变压器的次级端同样有六个抽头,实际的运行电压50V, 运行电流100A. 实际运行功率大概在5KVA.
实际运行的总功率300KVA,日耗电量7200度,熔化每公斤玻璃液的耗电量大概1。1度。
4.电熔窑的投资
100KVA三相磁性调压器(油浸)的价格37000元,315KVA三相磁性调压器(油浸)的价格95000元,40KVA单相磁性调压器(油浸)的价格18000元,20KVA单相磁性调压器(油浸)的价格10500元。 四台磁性调压器控制柜的价格8000元×4。 总费用19.25万元( 另外配有一只315KVA三相磁性调压器和一台磁性调压器控制柜)。所以实际总费用29.55万元。 钼电极的价格为500元/公斤,总重量400公斤, 总费用20万元。电熔锆刚玉砖(全致密的电熔锆刚玉砖总共10吨)、保温砖、粘土砖、高岭土大砖的总费用23万元。电缆线(含铜排)、配电柜的费用20万元。其它费用20万元。该窑炉的总造价在110万元左右。
5.电熔窑的烤窑及运行情况
电熔窑于2000年2月16日采用液化气烤窑,2月24日开始放料,经过14天的调试,3月8日已生产出合格的泡壳,泡壳已投放南非市场,电熔窑的运行状况良好。取得了良好的效益。
6.成型设备
成型设备采用的是十八头吹泡机。
7.电熔窑的烤窑和调试过程中遇到问题及其对策
烤窑过程中,当温度升到1000℃的时候,由于线路故障整个工业区停电检修(一般情况下工业区不停电),六小时之后恢复供电。停电期间将所有喷火孔、烟囱出口堵上,恢复供电之后慢慢加温至1000℃。
调试过程中,当滴玻璃液并进行吹泡机热调的时候,吹泡机的万向节出现了故障,一时又找不到供货的商店,所以决定将电熔窑降温至900℃进行保温,三天后万向节修好,将电熔窑升温至1390℃至正常出料。
此页网址为:
相关文章