工程分类
更多>>![]() |
|
![]() |
|
![]() |
|
![]() |
|
![]() |
|
![]() |
|
![]() |
|
![]() |
|
![]() |
|
![]() |
|
![]() |
|
![]() |
|
![]() |
|
![]() |
|
![]() |
|
![]() |
|
![]() |
|
![]() |
|
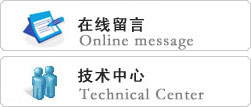
联系人:
电话:0511-88791451
手机:13951280541
邮箱:jfchen@ujs.edu.cn
地址:镇江市学府路80号
最新文章
您的位置:网站首页 > 最新文章熔制铅玻璃的电熔窑
1.铅晶质玻璃的熔制
采用火焰加热的池窑熔制铅玻璃,这种工艺的一个主要缺点在于熔制过程中氧化铅的挥发,其挥发量比在电熔窑中熔制时增加10%。多年来,铅晶质玻璃是在单坩埚窑、多坩埚窑或日池窑中熔制的。上世纪六十年代以来,使用了单元窑、马蹄焰池窑,玻璃产量、质量有了很大提高。用坩埚窑熔化玻璃时,很难消除粘土坩埚引起的耐火材料结石。日池窑因玻璃液面波动,冲刷耐火材料也引起比较严重的耐火材料结石和条纹。换热式连续熔化的池窑,其缺点是熔化过程中氧化铅的挥发量大,玻璃易分层还原;玻璃对耐火材料的侵蚀比较严重,容易引起条纹以及空气污染。这种池窑一般用天然气或城市煤气作燃料。如果用重油,会污染玻璃。
1959年以前建成了第一座电加热坩埚窑,采用SiC或MoSi2加热元件(前者水平安装,后者垂直安装)。其功率消耗是相当高的。后者曾用过电辅助加热的日池窑。然而,上述电熔方法并不能克服氧化铅的严重挥发、耐火材料对玻璃的污染比较严重以及环境污染等主要缺陷。
2.铅晶质玻璃电熔窑的现状及发展前景
由于铅晶质玻璃易挥发、分层、还原等特性,因而在池窑熔化中对温度、气氛、窑压、对流等工艺参数非常敏感。通过实践及对各种燃料、窑型的综合分析,英国、瑞典、捷克及西德各国都一致认为全电熔窑是最为合理的,也是比较经济的。
近十几年来许多国家对于全电熔窑进行了研究,取得了重大突破。现在世界上已有不少电熔窑,它的优越性越来越为人们所注意。
前苏联及东欧国家大力发展电熔晶质玻璃技术。前苏联上世纪七十年代初进行工业性试验,七四年推广。在基辅、古雪夫、列宁格勒、乌克兰、明斯克等艺术玻璃厂采用,获得了良好的技术经济效益。
电熔窑在正常操作中,当熔化池玻璃液中的电极附近温度为1370℃时,熔化池上部空间仅120℃左右。这是因为在玻璃液的表面有几公分厚的配合料冷料层,消除了氧化铅的挥发(一般火焰熔化池窑中氧化铅的挥发高达10%),使窑内玻璃组成均匀稳定,同时使粉料成本降低、环境污染减少,总之,电熔窑耗电量虽然较大,却节约了大量氧化铅,因而电熔窑还是经济合算的。
3.铅晶质玻璃全电熔窑内电极的选用
目前在铅晶质玻璃全电熔窑上使用的电极有两种,一种是氧化锡电极,特点是抗还原能力差,适用于氧化性玻璃;另一种是钼电极,特点是抗氧化能力差,适用于还原性玻璃。氧化锡电极非常适用于熔制铅玻璃。在熔制铅玻璃的电熔窑中,如果使用钼电极,会在不同程度上受到氧化,并且玻璃中的氧化铅被还原,生成金属铅沉到熔化池底,这样不仅使玻璃中氧化铅的含量减少造成浪费,严重时还会使氧化铅含量达不到中铅标准而使整批产品不合格,同时,沉到池底的金属铅还会严重侵蚀耐火材料,使窑炉寿命缩短。
例1 日产7吨铅晶质玻璃的电熔窑 某晶质玻璃厂使用电熔窑来熔化铅晶质玻璃。在使用耐火材料和二氧化锡电极方面积累了一定的使用经验。生产能力为7吨/天。 如图9.3.1所示,电熔窑由AZS —33电熔锆刚玉砖砌筑,深1700mm,面积为2.21m2,熔化池有两排电极。熔化池以流液洞和垂直上升道与工作池相连。上面一排电极由四组(每组为200×200×100mm的三个电极)组成,下面一排电极由四组(每组两个电极)组成。 电熔窑的熔化率最高可达3T/m2·d,单位耗电量1.05—1.07Kw·h/Kg玻璃。 两排电极的电流负荷分别是:上排1200—1250A,电压170—180V;下排600—650A,电压110—120V。 电熔窑在整个使用期间由五班吹制工进行操作。玻璃液的利用系数达到0.4。对电熔窑进行热工测量,沿熔化池高度方向玻璃液温度的分布如图9.3.2所示。在装有两排电极的电熔窑内,形成四个电能分布区域。其中两个热区上下分布(与两排电极相对应),另外两个热区由电流相互作用产生,处于两排电极间池壁附近。 经过一个窑期的运行,发现: 1.耐火材料侵蚀严重 (1)在熔化池池壁电熔锆刚玉砖中形成纵向及横向的裂缝。直接靠近电极的AZS—33电熔锆刚玉砖遭到极严重的侵蚀,它们的共同点是:形成深达160mm的气孔、沟槽和窟洞,它们往往是高温(高达1450℃)作用所致。熔化池底排砖流液洞、加料口和流液洞上壁砖的情况良好。由硅砖砌筑的拱顶和吊平碹的表面都有一层网状细裂缝,有耐火材料碎片。 (2)熔化池砖体的横向接缝处和电极附近有8—10mm厚的片状物的剥落(见图9.3.2.1)。由于这一区域的高温综合作用,玻璃液中碱性组分的强烈扩散集中在耐火材料表面层,以及玻璃液强对流的腐蚀作用。在电极附近的耐火材料试样中清晰地观察到耐火砖呈薄层状侵蚀这一特点。 (3)由于耐火材料表层有电流通过,释放出焦耳热。局部温度过高,是电熔窑中形成两股对流的原因。两股对流由电极侧壁上升,在电熔窑中部下降。炉壁周围玻璃液的高温及流动速度使耐火材料受到强烈的腐蚀。结果在玻璃液中周期性地出现耐火材料结石。 (4)耐火材料表层能量的释放加速了玻璃相的形成和碱性离子向耐火材料深处的扩散速度。经过研究分析,电熔窑熔化池壁表层(10mm深处)中K2O含量增加到6%。随着表层碱性组分的增加,其电导性也随之增强,因而引起温度的进一步升高,致使从耐火材料上剥落厚度为8—10mm的片状物,而在个别情况下还会引起整组电极变形。 (5)上述原因导致了电熔窑熔化池的电熔砖的腐蚀,使用14个月的之后因事故而停产。 2.电极的侵蚀 电极特别是上排电极不均衡的侵蚀除高温和强对流对电极有侵蚀作用外,由于电极与电极、电极与引电极接触处电阻的任意和无规则的变化所产生的高的电流负荷使电极上的电流密度达1.5—2A/cm2,超出标准电流密度2—3倍。如此大的电流密度使氧化锡电极的侵蚀速度加快了0.5—1倍。 3.对玻璃电熔窑工作情况的分析及耐火材料、电极侵蚀机理和特性的研究,证明了在熔窑的结构上存在严重的误差,这些误差在池窑冷修时考虑到了,并得到了改进 (1)熔化池池壁厚度减少到200mm。电极区域的耐火材料用大功率冷却装置加以冷却,其效果是要提高耐火材料附近和高温区靠近池壁玻璃液层的电阻,这就使得耐火材料的电导性降低,碱性离子迁移程度减小,耐火材料热机械性能稳定,除此以外消除了剥落现象和板状侵蚀。 (2)为改善电极工作条件,在它们的排列上避免了相互作用。各组电极使用单相供电极大地减少它们之间相互作用的部分能量,消除了局部过热,因而也减小了对流的流速。每个电极能单独操作。 (3)电熔窑碹顶使用粘土砖。 (4)优质的玻璃液和电熔窑工况令人满意,证实了结构设计的正确性。该电熔窑能生产吹制和压制玻璃制品。熔化率为2.5T/m2·d的情况下,玻璃液的利用系数为0.55—0.6。由于减小了熔化池侧壁的厚度以及对池壁进行冷却,耗电略有增高,约为1.25—1.3Kw·h/Kg玻璃,各电极上的电流密度为0.6A/cm2,分布均匀。 例2 用钼电极熔制铅晶质玻璃电熔窑 1986年某厂从Sorg公司引进一座铅晶质玻璃全电熔窑,该电熔窑的熔化池呈六角形,电极分布在三面池墙上,按△接法或Y接法与三相变压器连接。其优点是允许三相有均衡的负荷。电熔窑横截面电流分布比较均匀。有利于配合料均匀熔化。熔化池与澄清池面积基本相同。熔化池装有三层直径48mm的钼电极。设计熔化能力5.4~6.6T/d。 该电熔窑容量大,玻璃液在熔化池逗留时间较长。熔化率为2.6T/m2·d,单耗为1.12kW·h/kg玻璃。该电熔窑的熔化量具有较大的潜力。其“翻转限”仅比****熔化量低20%。 在熔制铅玻璃时,由于钼和氧化铅等发生氧化—还原反应,使钼电极受到腐蚀。所以应适当降低电流密度,以减少钼电极损耗,相应减少铅损失,提高玻璃质量,延长窑炉寿命。 例3 日产1.3T铅晶质玻璃的电熔窑 某电熔窑运行7个月后的工艺参数见表9.3.1。 表9.3.1 某电熔窑运行7个月运转后的工艺参数 出料量T/ 1.3 熔化池面积m2 0.6 电压V 105-110 熔化池深mm 950 电流A 550-570 熔化率T/d.m2 2.1 电功率Kw 58-60 流液洞尺寸mm 300X250 电流密度A/cm2 0.7 耗电量Kwh/Kg玻璃 1.2 PbO的挥发% 0.7—1.0 例4 日产3T的铅晶质玻璃电熔窑 该电熔窑熔化面积为1.5m2、深1m、矩形,熔化池通过流液洞与面积为1.76m2的园形工作池相连接。在熔化池的侧墙上安装了一排氧化锡电极组—每组由三个电极组成。 考虑到氧化锡电极的性能,烤窑时间为七天。使用能够在较高剩余空气系数(a=1.25~1.3)时工作的、保证熔化池和工作池中氧化气氛的喷咀。在电极上涂氧化铝和液体玻璃的保护涂层。玻璃料于1350℃开始熔化。当电极被玻璃液复盖住之后,按每小时25Kw输入电功率,同时减少煤气的耗量。当额定功率达到130Kw时,停止供气。 为了提供电熔窑最适宜的工艺参数,在三种出料量的情况下进行了实验数据见表9.3.2。当生产率为2.5T/d时,最适宜的输入功率为115~120 Kw,电能的消耗率为1.09~1.1 Kw·h/Kg玻璃。为了获得均匀的玻璃液,采用机械搅拌和煤气喷咀保持温度制度的稳定。使用直径为500mm的陶瓷叶8桨搅拌玻璃液,浸入深度200mm,旋转速度9~11转/分。制成了花瓶、水果盘和高脚制品。玻璃液的利用系数为40%(工厂通常的指标为38%)。 该电熔窑运行了24个月。使用情况表明:电熔窑降低了窑炉的基建和冷修费用、配合料组分挥发减少三分之一以上、保证了玻璃化学组成的稳定以及玻璃液的高度均匀性。 表9.3.2 电熔窑生产 能力(T/d) 输入功率 (Kw) NO1 2 95 NO2 2.5 115~120 NO3 3 140 1-接通上排电极电源时 2-切断上排电极电源时 图9.3.3 温度沿熔化池高度的分布曲线 例5日产9T的铅晶质玻璃电熔窑 该窑面积3m2、深1.8m。熔化池通过流液洞和垂直上升道与深0.5m、面积为3.67mm2的工作池连接。设有六只挑料口,可供6组吹制工使用。 电极组水平布置成三排:上排由5组组成,(每两个电极组成一组的有两组;每三个电极组成一组的有三组),中排由每两个电极为一组的五组组成;下排由每一个电极为一组的四组组成。在垂直上升道中,为加热玻璃液安装了两个电极。 测量了上排与中排,中排与下排电极之间各点以及沿垂直中心的温度,此时温度在玻璃液中的分布示于图9.3.3。玻璃液的利用系数为41%。 1.生产过程中出现的问题 在铅晶质玻璃的熔化过程中可以看到配合料层厚度的减少和冷顶局部过热的问题。沿着熔化池深度方向测量玻璃液温度的结果证明,温度的****值接近冷顶配合料层,这是形成冷顶局部过热的原因。 依靠加大窑炉的出料量的方法不能消除这种过热现象,这是由于上排电极到配合料表面的距离为350mm,由216Kw功率通过上排电极输入,在这个区域出现了局部过热的最高温度区,这种过热首先导致了较高的电能消耗。 切断上排电极电源,功率分布在中排和下排电极之间。这样能够使电熔窑的工作制度稳定,降低了电能消耗,将****温度区移到中排电极。 保证配合料层最适宜的厚度是电熔窑正常工作的重要的和必须的条件。这种配合料层不仅保证熔化表面很好的隔热,而且是凝聚配合料中易挥发组分的介质。 2.电熔窑的改进 电熔窑经过一年的运转,对电熔窑的结构进行了一系列改进。改进后的电熔窑的结构如图9.3.4,熔化池的尺寸和电极的布置有别于以前的电熔窑。深度1.65m,熔化池的面积为2.21m2。氧化锡电极布置成两排。电熔窑使用了一年左右,仍处于良好的状态中。 实验用、工业实验用和工业用电熔窑运转的比较分析(见表9.3.3)可以做出下列结论:熔制铅晶质玻璃的工业电熔窑可保证玻璃液的高度均匀性,可以成型高质量的高级艺术吹制制品;它能极大降低挥发而造成的损失,且可节约价值昂贵的稀缺材料(铅丹、硼酸等)。 表9.3.3 参数 电熔窑 实验用 工业实验用 工业用 出料量(T/d) 2.5 9 7-7.5 熔化池面积(m2) 1.5 3 2.21 成型池面积(m2) 1.76 3.67 3.67 熔化池深度(m) 1 1.8 1.65 配合料层厚度(m) 0.1 0.2 0.25 熔化率(T/m2.d) 1.66 3 3.15-3.37 电极数量 18 58 44 能耗(Kwh/Kg玻璃) 1.1 1.1 0.93 输入 功率 (Kw) 上排电极 216 200 中排电极 115-120 80 下排电极 35 70 玻璃液的利用系数 40 41 43 工作窗口的数量 2 6 6 搅 拌 器 直径(mm) 500 600 600 旋转速度(转/分) 9-11 25-28 25-28 数量 1 1 1 例6 用棒状氧化锡电极电熔窑 电熔窑生产含PbO18—24%的玻璃。电熔窑的详细情况示于图9.3.5。电熔窑的熔化池和工作池采用直径18.5mm长200mm的棒状氧化锡电极 (图9.3.5),熔化池和工作池之间由流液洞连接,烤窑的温度由三根硅碳棒加热,电功率通过变压器供给,每组硅碳棒加热的电压可在很大范围内调节,熔化池二个棒状电极从侧面插入窑内,另两个电极由窑底插入,在工作池只使用底部插入的电极,由于熔化池采用水平安装的电极,其表面比较小,电流密度比较大,引起电极周围温度升高,电极附近能量的集中使玻璃液产生对流,这种对流由电极两侧上升到表面,从而给流向流液洞的液流造成了障碍。电熔窑的熔化情况如表9.3.4。 表9.3.4电熔窑的熔化情况 项目 棒状氧化锡电极的电熔窑 氧化铅的含量 18% 熔化温度℃ 1420-1425 作业温度℃ 1270 电流密度A/cm2 1.1 熔化率Kg/m2.d 2000 产量Kg/h 8 运行时间(天) 20 例7用块状氧化锡电极的电熔窑 采用200×200×110mm的块状电极,由侧面插入到熔化池,进行深层玻璃的熔化,而工作池用棒状电极。 电熔窑分为熔化池与工作池,由流液洞连接,熔化池呈长方形,工作池以一定的角度向上倾斜(见图9.3.6),硅碳棒安装在窑上部,以便窑炉烤窑时使用,这种型式的窑气泡上升的速度比玻璃液的流动要快。 玻璃的深层熔化是在70—100mm厚的加料层下面进行的,上面料层的温度为240℃,玻璃液中的最高温度区是在电极的深处,在电熔窑中,玻璃的熔制过程是从表面至底部垂直进行的,所以这种窑内玻璃是在恒定的温度下熔制,电熔窑的熔化情况示于表9.3.5。二氧化锡电极的损耗是极小的,看不到机械磨损,电极使用30天后仍然可以继续使用,在这种电熔窑内熔制的玻璃很均匀但有少量气泡,电熔窑熔制玻璃的特点示于表9.3.6。 从表9.3.6可知,玻璃比用火焰窑熔制时有较高的折射率,并不考虑氧化铅的挥发,可以得出如下的的结论:用二氧化锡作电极,在电熔窑中熔制铅玻璃是可行的。 表9.3.5电熔窑的熔化情况 项目 块状氧化锡电极的电熔窑 氧化铅的含量 24% 熔化温度℃ 1350-1360 作业温度℃ 1230-1240 电流密度A/cm2 0.55 熔化率Kg/m2.d 800 产量Kg/h 2.5 运行时间(天) 30 表9.3.6 火焰窑与电熔窑熔制铅晶质玻璃时的比较 项目 电熔窑 火焰窑 玻璃组成中氧化铅的含量% 1.99 14.5 熔制时氧化铅的挥发量% 0.06 19.5 可见光透过率% 92-95 86-88 密度g/cm3 2.85 2.7 折射率 1.56 1.53 例8 日产1~3T铅晶质玻璃的电熔窑 电熔窑的熔化效率和玻璃液的质量在很大程度上取决于熔化池的深度和电极上部边缘到料毯的距离,一般熔化池的深度在1m左右。 电熔窑结构如图9.3.7所示。由熔化池、工作池、流液洞组成。熔化池侧面装9块SnO2块状电极,两面共18块。工作池共两块。电极尺寸为195×195×95mm。每块电极之间要很好地绝缘,以保证电流在电极上均匀分配,延长电极寿命。日产1.3T和3T铅晶质玻璃的电熔窑熔化池垂直方向温度分布如图9.3.8和图9.3.9所示。1—3T/d电熔窑的技术指标如表9.3.7。 表9.3.7 技术指标 1.3T 3T 熔化 池 面积m2 0.6 1.2 池深m 0.8 1.05 工作 池 面积m2 0.39 0.48 池深m 0.8 1.05 流液洞尺寸m 0.3×0.25 0.3×0.25 熔化温度℃ 1405 1405 熔化率T/m2.d 2.0 2.5 电功率Kw 60 140 电压V 105-110 120-130 电能消耗 Kwh/Kg 1.2 1.1 电极的电流密度 A/cm2 0.7 0.64 例9 日产12吨铅晶质玻璃的电熔窑 电熔窑的结构如图9.3.10所示,有熔化池、流液洞、六个挑料口对称地分布在熔化池两边。这样玻璃液由熔化池同时向两个方向流出,减少了熔化池的温度梯度,使熔化过程保持平衡稳定。设两个溢料口,其作用是当挑料停止时保证电熔窑运行稳定,玻璃液可自动经两边溢料口溢出。 在熔化池的侧墙上安装24块SnO2电极,12块并联组成一组电极。工作池的每个挑料口用挡砖隔开,并在每个挑料口里安装一对电极,以便直接加热玻璃液。这样不仅能够建立局部的温度制度,保证在同一时间里加工不同重量和形状的制品,而且可促进玻璃液的对流,得到不用搅拌的均匀的玻璃液。 主要技术参数如表9.3.8 生产能力 T/d 12 熔化池面积m2 4.3 工作池面积m2 2.6 挑料口数个 8 容积T 22 出料率T/m2·d 2.8 工作池玻璃液表面温度℃ 1020—1100 电极数个 70 功率Kw 310 电流A 1460 电压V 212 玻璃液电耗Kwh/kg 0.62 熔化池热效率 78% 例10 熔化钡晶质玻璃的电熔窑 1. 钡晶质玻璃的化学组成(重量%) SiO257、 Al2O31.8、 BaO19.5、 Na2O3.5、 K2O16、 ZnO2.2。 2.钡晶质玻璃的料方(重量%) 石英砂57.0、 氧化铝1.8、 碳酸钡25.0、 碳酸钠2.56、 硝酸钠5.46、 硝酸钾12.9、 硝酸铵2.0、 碳酸钾14.6、 锌白2.2、 Sb2O3 0.3、 As2O3 0.3、 钴0.0001、硒0.0028。 3.电熔窑主要技术参数如表9.3.9 表9.3.9 生产能力 T/d 5 熔化率 T/d·m2 1.27 容积 T 18 熔化池面积 m2 3.92 总功率 Kw 300—350 电流 A 1500—1600 电压 V 210—230 能耗: Kwh/kg 1.43—1.68 手工工作池面积 m2 0.9 机械作业工作池面积 m2 0.6 熔化池热效率 48—57% 电熔窑结构如图9.3.11所示,有矩形熔化池、流液洞、垂直上升道、两个挑料池。两个挑料池设三个挑料口供手工成型、挑料池和小型供料机相连接。溢料口设在工作池的尾部,在压机停车时玻璃液经溢料口溢出。 熔化池装有200×200×100mm砖形电极12块,工作池,流液洞使用了棒状SnO2电极。 例11 熔制铅晶质玻璃的三相电熔窑 单相玻璃电熔窑中熔制铅晶质玻璃,结构简单、使用可靠。与三相电熔窑不同,单相电熔窑不需要复杂的控制系统。但功率超过100Kw时便会破坏企业供电系统中相位平衡。 熔制铅晶质玻璃的深型三相电熔窑,生产能力为1—1.2T/d,该铅晶质玻璃的组成(重量%)如下:58.3SiO2; 24.5PbO; 14.7K2O; 1 B2O3; 0.8 ZnO; 0.66Al2O3; 0.036Fe2O3。 电熔窑结构如图9.3.12,由流液洞连接熔化池和工作池。为使玻璃液从电熔窑中完全的排出,在熔化池底部设有放料孔,正常工作时用砖和冷却装置堵住。电熔窑的池壁由AZS-33砖砌筑,上部结构由硅砖砌筑。应用玄武岩纤维保温。电熔窑底部用厚500毫米的保温砖保温。 采用尺寸为200×200×100mm的氧化锡电极对玻璃液供电加热。在电熔窑的熔化池有四对电极(每相两对),在流液洞和工作部各设一对。电极的固定冷却装置的结构如图9.3.13。氧化锡电极按装在电熔窑体内的深度为5mm,用水玻璃和经粉碎的晶质玻璃粉作为电极的保护层。 电熔窑由TC—160/0.5A型三相变压器(图9.3.14)供电。变压器的副边线圈形成单独的三个单相电源,其电压向量相对移动120°。电熔窑熔化池电极由两个线圈(a-x)、(b-y)供电,而流液洞和工作池电极由第三个线圈(c-z)供电。由MY1、MY2和单相升压变压器T1、T2组成的升压变压器平稳地调整熔化池电极上的电压。 熔化池中得到热均匀的玻璃液,无须装置机械搅拌器。玻璃液温度沿电熔窑熔化池深度分布的曲线列于图9.3.15。电熔窑的技术特性见表9.3.10。电熔窑池深为1.8m,面积3m2,熔化率达3T/m2·d。熔化玻璃的总功率只有320—340Kw。 电熔窑所用耐火材料为烧结锆刚玉砖;主要用在熔化池、工作池和流液洞。其它部位用一般耐火材料。 表9.3.10 1 生产能力 T/d 1—1.2 2 熔化池 面积 m2 0.5 深度 m 0.9 3 工作池 面积 m2 0.36 深度 m 0.56 4 液 流 洞 宽 m 0.3 长 m 0.2 深 m 0.5 5 面积熔化率 T/m2d 2~2.4 6 体积熔化率 T/m3d 2.23~2.67 7 能耗 Kwh/Kg 1.2~1.4 8 电压 V 100~125 9 电流 A 270~290 10 电极的电流密度 A/cm2 0.65~0.75 11 一个水套的热量损失 Kw 1.3 12 功率 Kw 55~60.7
1.窑炉的结构 某厂一座日产12T铅玻璃电熔窑。引进的冷炉顶电熔窑主要用来生产电光源和电子工业用的高铅玻璃。熔化率大于1.8T/m2d,出料量为6~10T。扩建后****出料量可达12T。电熔窑采用全保温,能耗为1100KWh/T玻璃,热效率可达60%以上。其结构如图9.3.16所示。 熔化池的尺寸为2150×3200×700mm(长×宽×深), 澄清池的尺寸为2150×1850×955mm(长×宽×深)。在熔化池与澄清池之间的台阶上装有12对主电极。澄清池底部,设有3对启动电极,热装碎玻璃时起辅助加热作用,正常生产时一般不用。池底中央有一凹池,安装有放料装置,可以定期放出脏料。 整个电熔窑所用的电极均为氧化锡电极(有带水冷的特殊“银接头”),它可把电流迅速带到氧化锡电极的具有良好导电性的部位,从而降低了系统的电阻,这种电极的寿命两年。 与玻璃液接触的耐火材料为西普公司的ER1681和ER1711电熔锆刚玉砖。保温层有硅线石衬背砖和轻质保温砖。在熔化池池墙拐角处和液面线附近的横接缝处,都能直接观察到电熔砖,此缝也是膨胀缝。 电熔窑的上部空间位于熔化池之上,由吊平碹 、炉门和窑墙围成。位于一侧的炉门,在烤窑和应急时,可通过手轮来升降,以调节上部空间的开度,形成一个封闭的或半封闭的空间。正常生产时,炉门全部提起,为M63加料机(如图7.2.3)提供运行空间和人工操作空间,同时也为除尘提供方便。炉门中央的加料门,为特制的螺旋加料机(如图7.2.2)热装碎玻璃用。 炉门上设有观察孔,主要用于烤窑期间观察火焰情况和增设燃烧器。在与炉门相交的一侧墙上也设有观察孔,也是测定氧含量的取气孔。在与炉门相交的另一侧墙上,设有燃烧器孔和烟囱。烟囱上也设有观察孔,观察窑内情况。 烤窑时,窑压可通过烟囱顶部的两块挡板调节。正常生产时,烟囱作排出废气用。上升道上也设有小孔,烤窑时安装小型燃烧器用。正常生产时,用来观察玻璃液面与对面孔里的液面探针运动情况。 烤窑时,在碹顶中间、熔化池池墙上、流液洞、上升道、料道下层前部、中部和后部及上层前部和后部、池底凹池处10个部位设有10个测温点对温度进行监控。升温曲线所要求的温度是碹顶和熔化池应达到的温度,同时要兼顾其它各点的温度。烤窑结束时,将拆掉凹池处的临时测温点,用9个测温点进行生产控制。 上升道和流液洞也设有电极,用来调节玻璃液的温度。 电熔窑电源用单相二线,整个截面上电流密度均匀、系统较简单。对电熔窑的流液洞、上升道和料道,另外用辅助变压器供电。 结合我国的实际情况。备有备用发电机,考虑电网停电时,保证向流液洞、上升道和料道供电即可。向电熔窑供电的主电源,不设备用电源。允许短时停电。但此时电极接头的冷却水不可断。断水使接头的银杆炸裂,进而使电极损坏剧烈。 电熔窑配备了下列仪表和调节装置:玻璃液面指示和加料自动控制;电熔窑主要部位的温度指示和记录;玻璃液电阻值的指示和记录;电极电压指示与调节;报警系统(含视、听信号);安全装置;其它指示仪表。 M63加料机的加料臂可缓慢进退,同时在横向均匀布料;输送带采用耐热不锈钢带,震动加料;必要时,加料臂可快速从窑中撤出。该加料机不仅满足工艺要求,而且能长期安全运转。 2.复合式电加热料道 料道用复合式电加热,玻璃液面以下用氧化锡电极加热,料道尺寸为4000×406×143mm(长×宽×深),通过垂直上升道和流液洞与澄清池相连。上层用硅碳棒进行辐射加热,对玻璃液面上的耐火材料起保温作用。 3.改进意见 电熔窑是先进的,但是仍存在一些问题需要商量改进: (1)关于窑型:电熔窑结构简单。主电极仅有一层,电压只能同时升降;,应改为多层电极,电压分别调节,可使熔制工艺更合理。电熔窑的截面改为多角形更合适。这样可避免拐角处布料不均,以及拐角处的粉料与中心处的粉料的热历史的差异,并且有利于三相平衡供电。流液洞:改为向上倾斜式更合理。 (2)关于寿命: 由于采用了无缩孔的优质AZS砖,并注意配套使用,电熔窑耐火材料的寿命已达5—6年。但是,电极的寿命仅有2.5—3年。电熔窑运行二年半后,需要换电极,毕竟麻烦。因此,对电极的材质、接头继续改进是必要的。 (3)关于控制:利用微机对电熔窑的主要参数巡回检测和自动控制,可进一步提高控制水平,使操作****化。
此页网址为:
相关文章