工程分类
更多>>![]() |
|
![]() |
|
![]() |
|
![]() |
|
![]() |
|
![]() |
|
![]() |
|
![]() |
|
![]() |
|
![]() |
|
![]() |
|
![]() |
|
![]() |
|
![]() |
|
![]() |
|
![]() |
|
![]() |
|
![]() |
|
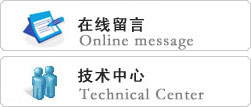
联系人:
电话:0511-88791451
手机:13951280541
邮箱:jfchen@ujs.edu.cn
地址:镇江市学府路80号
最新文章
您的位置:网站首页 > 最新文章熔制硼硅酸盐玻璃的电熔窑
硼硅酸盐玻璃在传统的火焰池窑熔制过程中,常常会遇到硼的挥发逸散损失的问题。硼的挥发不仅使玻璃液不均匀,恶化玻璃质量,而且还白白地损失了价格昂贵的硼原料。因此,国外对减少硼的挥发问题进行了长期研究。迄今为止,硼的挥发率在10~15%,如果采用无水硼砂或硼酐作原料,可以降低到5~10%。
国外,自从厚料层垂直深层全电熔窑出现后,给高硼硅玻璃的熔化带来了新方法,大幅度降低了硼的挥发。英国、美国、西德、日本、捷克和前苏联等国家都相继采用这种方法使硼的挥发率降低到1~2%。美国已有18座日产为100~150T全电熔窑生产玻璃棉,前苏联生产派来克斯玻璃和高硼电真空玻璃也采用了全电熔窑。日本和前苏联还研究了生产无碱E玻璃的全电熔窑,规模较小的拉丝池窑和球窑也投入了生产。
我国硼硅玻璃的生产基本上采用火焰窑。在高硼硅玻璃系统中,玻璃质量达不到理想程度。特别是熔制高硼玻璃系统的高硅氧玻璃球生产中问题更多,硼的挥发率高达74%,碱的损耗率高达143%,球质远远不如目前的中碱和无碱球,成本较高。对硼硅酸盐玻璃的全电熔工艺研究,早在上个世纪七十年代初研究了无碱E玻璃(含B2O310%)的全生料层的电熔工艺,在日产1T的小型电熔窑中,硼的挥发量为10%左右,熔制的玻璃质量较好。对于硼硅玻璃厚料层电熔工艺尚未研究。
1.减少硼挥发的机理
硼硅玻璃的配合料投入火焰池窑后,首先是火焰和高温高速气流掠过配合料的表面层,将比重较轻的组分和硼酸、纯碱等物质裹入到烟气中,从小炉口排出,造成了硼和碱的物理损耗;接着配合料在加热过程中的脱水期,硼容易从配合料中挥发;当形成玻璃后的澄清均化阶段,由于高温炉气对玻璃的作用,硼以碱和碱土金属的硼硅酸盐形式,从玻璃熔体表面上蒸发出来,这就构成了物理—化学形态的硼酐挥发损失。绝大多数硼的烧损,是发生在200~500℃配合料脱水期、即游离态的硼挥发率最高,而在熔融的玻璃液中、成结合状态硼的挥发率较小。
全电熔厚料层垂直深层电熔工艺,熔化池表面复盖冷的配合料,配合料在复盖层下加热,从加热到玻璃形成的四个阶段,都在同一个地点,不同的时间和不同的垂直高度上完成。因此,它可以基本避免在火焰池窑中所造成硼挥发的存在条件。其机理是:
⑴ 配合料层表面工作状态平稳。全电熔厚料层熔制玻璃时,由于配合料是很好的绝热材料,料层的表面温度可低达200℃以下,而且料层表面没有任何火焰和高温高速气流的冲击,处于平稳状态,基本上可以避免“飞料”的硼酐物理损耗。
⑵ 冷炉顶可以回收硼的挥发物。厚料层的料层厚度一般在100~200mm,表面温度在200℃以下,因此又可称“冷炉顶”。从一幅典型的熔制高硼硅玻璃的冷炉顶图9.4.1中,可以看到配合料表面0~40mm这一层,温度稳定在120℃,仅水份在蒸发,可称为冷配合料层。深度在40~80mm,温度从120℃提高到250℃,硼酸开始分解,称为热配合料层,深度在80~110mm的温度变化最剧烈,从250℃上升到1000℃,完成了硼硅酸盐的反应过程,称为硼硅酸盐反应带,也可称轻质层。再下一层则是含有大量气泡和带有未熔化好砂粒的熔融玻璃,称为玻璃的熔融过程,也可称半熔层。在这层下面就是玻璃的澄清和均化区域。硼硅酸盐配合料从表面的料层到轻质层,经过温度从120~1000℃的热过程,必然会发生硼酸和硼砂在脱水期中的硼酐挥发,挥发物由下向上逸出时,遇到冷的表面配合料层凝结起来,便产生硼的回凝现象,而在反应过程中所产生的CO2和NOx气体很容易穿过疏松的配合料层逸出。因此,硼的挥发物可以在这里几乎被回收。应用这个原理,同样可以回收其它含有氟、铅和硒玻璃的挥发性物质。由此也很容易解释薄料层全电熔熔制工艺中硼的挥发率较高(10%左右)的原因。
⑶澄清和均化在垂直深层方向中进行。在垂直深层电熔窑中,在工作流的作用下,玻璃液从半熔层垂直向下运动,流向流液洞(见图9.4.1),而玻璃中的气泡依靠斯托克斯的原理由下向上运动,向液面排出,完成了澄清和均化过程。这个过程与水平式火焰池窑熔制有较大的区别,它好象在垂直管道中进行,没有与空气相接触的自由表面,因此不可能产生硼从玻璃结合态中挥发的问题。
从上述的熔化机理,可清楚地看到,由于硼的烧损减少到极小的程度,玻璃成份波动小、稳定,这是获得优质硼硅酸盐玻璃的重要工艺条件之一。
2.厚料层垂直深层电熔技术
如果厚料层操作不当,不但得不到好的玻璃质量,反而会在玻璃中产生结石和条纹,使玻璃质量变坏。要达到稳定作业,厚料层电熔的基本工艺技术,大致如下:
⑴ 严格控制料层厚度,厚料层全电熔窑,料层的厚度是一项十分重要的工艺参数,正常操作的料层厚度在100~200mm。太厚的料层使其深部造成更多的冷配合料,熔融玻璃液面温度降低,玻璃熔化不好。同时由于料层的绝热作用,深部的配合料温度升高,软化生料,形成一个半硬壳层,可能伸长到与四周池壁搭接,形成料拱。气泡聚集在料拱下排不出去,玻璃液面很快下降,造成脱空现象,严重时发生料玻璃液流空的事故。为了防止料拱现象和使玻璃中气泡能顺利排出,配合料不能完全复盖熔化表面。按Sorg公司在VSM的全电熔窑的经验,配合料复盖的面积占液面90%,留出10%面积的光面。熔制普通白玻璃,光面留在六角形的六个角上。熔制乳白玻璃光面留在中心。对矩形的电熔窑,在池壁四周留出75~150mm的距离。如果料层太薄,配合料表面温度很快上升,料层的保温作用和硼的回凝现象消失、达不到厚料层熔制工艺的目的。另外,加料必须是均匀铺盖在玻璃液面上。如果局部地方形成料堆,最后将使料堆下沉,热的玻璃液包住冷的生抖,在玻璃中容易产生结石、气泡等缺陷。
(2)保正常条件下的电—热平衡,当改变熔窑出料量时,若电工参数没有及时调整,很快打破了原来工作状态的电—热平衡条件,而转入不稳定状态,窑内温度分布曲线和玻璃液的运动轨迹都会发生改变。若加大出料量而输入功率不变时,玻璃液面温度下降,热点下沉,在窑内出现“过冷”现象,迫使玻璃液面下降,料层变厚,大量的配合料下沉,生料来不及熔化。反之,出料量变小时,玻璃液面温度升高。热点上移,在窑内出现过热现象,使生料熔化速度加快,料层变薄,液面提高,引起耐火材料和电极加速侵蚀。因此当改变出料量时,输入功率与出料量要匹配好,应尽量保持熔制工艺条件的电—热平衡。
(3)建立合理的熔制温度曲线和稳定的玻璃液流,窑内玻璃液的温度差异是产生玻璃液对流的原因,在厚料层垂直深层电熔工艺中,如温度场不合理,表面层(半熔层)未熔化好的玻璃液常有少量垂直对流进入工作流使熔化好的玻璃液变坏。在半熔层中玻璃液的小对流将未熔化好的原料托浮起来,固定半熔层和冷料层的位置。当半熔的玻璃进入最高温度区的加热区时,玻璃熔融过程就结束了,即进入玻璃的澄清均化区域,在这个区域内不要产生强烈的垂直对流,使所有玻璃都经过了相同的热过程熔制出均匀度高的玻璃。因此在最高温度带的温度分布曲线要平坦,不要发生大的温差。根据这一原理设计的电熔窑的温度分布曲线,有助于获得热均匀性好的玻璃。
(4)要有足够的玻璃液深度,全电熔窑熔化硼硅玻璃,熔化率要比火焰窑高2-3倍,这样高的熔化率,又要在垂直深层方向上完成玻璃的澄清和均化,必须有一个足够的深度,满足玻璃在窑内的停留时间,池深与熔窑的生产能力和熔化率等因素有关,一般液深在900mm以上。例如高硼硅玻璃6m2电熔窑中,池深1.38m,在15-20 m2的VSM电熔窑中,池深2.2m。
3.高硼硅玻璃熔化特点及使用电熔的优越性
高硼硅仪器玻璃在科学实验和日常生活中有着广泛的用途,其制品有:各种烧器、量器、各种实验室用分析食品及各种玻璃化工管道。在科研教学单位的实验室、工矿企业及太阳能综合利用设备上都可以见到用高硼硅仪器玻璃制做的各种产品。由于高硼硅仪器玻璃产品用途的特殊性,决定了这种玻璃必须具备有良好的热稳性和化稳性,根据这些要求,经过几十年的探索,目前国内外高硼硅仪器玻璃的化学组成基本上如下表9.4.1所列。
表9.4.1 国内外高硼硅仪器玻璃的化学成分及热膨胀系数α
牌号 |
国别 |
化学成份 |
热膨胀系数a 0-300 ℃ | |||||
SiO2 |
B2O3 |
Al2O3 |
CaO |
K2O |
Na2O | |||
派来克斯PYREX-7740 |
美国 |
80.5 |
12.6 |
2.1 |
0.1 |
4.5 |
32×10-7/℃ | |
杜朗DuRuN-50 |
西德 |
80.5 |
12.5 |
2.5 |
0.5 |
4.0 |
32×10-7/℃ | |
西马克斯SIMAX |
捷克 |
81 |
12.6 |
2.0 |
0.1 |
4.0 |
32×10-7/℃ | |
派来克斯PYREX |
法国 |
80.5 |
13 |
2.25 |
0.1 |
1.15 |
3.15 |
32×10-7/℃ |
北京特硬料BT-TY(GG-17) |
中国 |
80.7 |
12.5 |
2.2 |
0.6 |
4.0 |
32×10-7/℃ |
从表9.4.1中可以看出,这种玻璃有一个共同点:都含有超过80%的SiO2和超过10%的B2O3。高含量的SiO2和低含量的Na2O使玻璃结构中的硅氧四面体多以大型四面体的形式存在,四面体间多以硅氧键的形式相连接。而且,12%~13%含量的B2O3又可以使结构中被Na2O切断的网络一大部分又以B—O三角体结构连接起来。这样,就使得高硼硅仪器玻璃的粘度很大(见表9.4.2)
表9.4.2 高硼硅仪器玻璃和普通钠钙硅玻璃粘度参考点对比
参考点 种类 |
操作点 103帕.秒 |
软化点 106.6帕.秒 |
退火点 1012帕.秒 |
应变点 1013.5帕.秒 |
高硼硅仪器玻璃 |
1252 |
821 |
560 |
510 |
普通钠钙硅玻璃 |
1005 |
696 |
514 |
473 |
由于熔化速度的快慢是和配合料中的石英颗粒的熔解速度直接关联的,而熔体的粘度大则减慢了SiO2从石英颗粒表面向周围的扩散运动。于是,为降低熔体的粘度,只有提高温度,这就是高硼硅仪器玻璃熔化的第一个特点:熔化温度高(粘度在10ρa·s时其温度>1680℃)。但就目前窑炉大碹材料来看,要使其熔化温度达到1700℃以上是不实际的。因此,只能延长熔化时间。根据计算,PyREx玻璃的熔化速度常数高达7.9而且热能消耗很高(12000KCal/Kg玻璃)。国内这种玻璃的熔化率只有0.2~0.3T/M2·D左右。高硼硅仪器玻璃的高粘度还会引起另一个问题:即熔化过程中的玻璃液分层问题。由于普通火焰加热池窑的下层没有热源,随着池深增加,温度越来越低。这样,下层玻璃液的流动性也就越来越差,使成分中比重较大的Al2O3等组分容易下沉,形成含Al2O3量高的变质层。当温度、液流变化时,容易被裹入玻璃液流形成条纹等缺陷。另外,由于SiO2的含量很高,在温度较低的区域,还易出现析晶,从而形成结石。B2O3的挥发是高硼硅仪器玻璃熔制过程中的又一特点,B2O3挥发使玻璃液表层形成一层富硅玻璃,不但影响到玻璃的化学组成,而且B2O3的挥发量随温度的升高而增加,这对于高硼硅仪器玻璃需要高温熔制无疑是不利的。当操作条件发生变化时,这层富硅玻璃如被带入成型流,就会在产品中产生条纹、结石等缺陷。
(1)由于以上这些特点,构成了高硼硅仪器玻璃的难熔性。所以,至今为止,国内大多数厂家都还局限于小型火焰池窑和坩埚窑进行熔化供给人工吹制成型的小批量生产,能耗大,成品率低,工人劳动强度大。而机械化、自动化的大批量生产则基本上还没有出现。为了满足市场需求,提高我国的熔化技术水平,国内玻璃界一直在试图解决这一难题。
(2)想熔化出高质量的高硼硅仪器玻璃,一个重要的途径就是提高玻璃液的温度,但是考虑到火焰空间耐火材料的承受能力,单纯依靠火焰加热难于将玻璃液加热到1650℃以上,国外对这种玻璃的熔制已普遍采用了电助熔和全电熔两种熔化方式
(3)布置于池底的电极通电后,处于熔融状态的玻璃液为一导体,具有一定的电阻值:R=log
(R是玻璃液电阻—Ω K是玻璃液的电阻率—Ω·cm L是玻璃液深度—cm。S是电极间距—cm D是电极直径—cm)。根据电阻的热效应原理,两电极间的玻璃液就会发热。同时,由于电极端部的边缘效应,电极端部附近的玻璃液温度最高,根据两年多来的运行经验,此处温度甚至可达1700℃以上。由于比重的差别,在电极附近就形成了如图所示的玻璃液流,池深方向各层的玻璃都充分参加了这一流动,从而消除了高硼硅玻璃分层所带来的问题。另外,电极端部在玻璃液中的“放热”现象及由此而产生的玻璃液流提高了底层玻璃液的温度,加快了石英颗粒的溶解速度,促进了玻璃的澄清和均化。
我国熔制硼硅酸盐玻璃的电熔窑大多为小型窑,冷顶电熔窑与火焰窑相比具有节能、提高质量、降低成本等显著的优越性。
(1)小型电熔窑有较好的经济性,以日产2.0吨的高硼硅玻璃球窑为例,从燃料和硼挥发两顶进行比较如表9.4.3
表9.4.3
生产方式 项目 |
火焰窑 |
热顶电熔窑 |
冷顶电熔窑 |
硼挥发% |
18 |
10 |
3 |
窑的热效率% |
6.5 |
40 |
60 |
(2)玻璃质量好,在火焰池窑中由于窑温、窑压、气氛和产量等工艺条件发生变化,都要引起硼的挥发率的变化,使玻璃不均匀。同时火焰窑和热顶电熔窑,硼的挥发严重腐蚀了上部结构,不但缩短了窑炉的寿命,而且碹滴落入玻璃窑内,影响了玻璃质量。冷顶电熔窑完全可以避免上述弊病,获得高质量的玻璃。
熔制硼硅酸盐玻璃的电熔窑实例如下:
例1 日产1.5T高硼硅玻璃的电熔窑 某厂一座日产1.5T的高硼硅酸盐耐热玻璃的电熔窑,情况如下: 1.玻璃的组成与性能 (1)玻璃的组成见表1.1.6中序号15,电阻率温度曲线见图1.2.10中序号15 (2)澄清剂 使用CeO2和NaCl为澄清剂。 (3)膨胀系数(0—300℃)39×10-7 (4)软化点 770℃ 2.电熔窑的结构 电熔窑采用正方形,由熔化池和工作池组成,用流液洞连接,结构均为几何对称。整个玻璃液面均由配合料覆盖,其空间温度100~200℃,覆盖层厚度一般为4~40cm。主要的热能由玻璃液深处供给,达到1500~1600℃。图9.4.2为硼硅酸盐玻璃的全电熔窑。 3.电极的选择 ⑴该窑炉使用高纯钼棒作为电极,其规格为φ50×1200mm,比重为10.1g/cm3。其化学不纯物(ppm)为:C 20~50 Si 5 W 21 Fe 10 Al 1 O2 7.9 Ni 0.5。 ⑵ 电极电流密度 J=0.309A/cm2。 ⑶在电极的使用中,根据电流和电压的变化,随时对电极进行调整。实际生产中,电流是恒值,根据电压的变化来调整电极尺寸。在调整时原则上是每月将电极向玻璃液内顶入50mm。 4.电极的水冷保护 ⑴该设计采用采用密封式水套。经过二十个月的运行,设计的电极水套是成功的,运行 可靠,操作方便。表9.4.4 为电极水套吸热所耗功率。每支电极水套的吸热量为2~4Kw/h。 表9.4.4 电极水套吸热量 部位 电极冷却带走的热量 Kw/h 冷却水量 l/h 熔化池 2.7-2.85 100-120 上升道 2.2-2.35 100-120 ⑵在水冷系统中,为了节约用水,采用如图3.8.1所示循环水冷系统。每支电极用水量为2~12L3/min,水质达到锅炉用水标准1.5d。
电熔窑采用单相隔离变压器供电,可控硅恒温、恒流恒压控制一次侧电压,基本上能达到功率控制稳定。其电气原理见图9.4.3。电熔窑操作时,升温、降温速度快,调节灵敏。
该厂电熔窑密封不良,又是采用敞开式间隙加料,炉内温度波动大,经过几年的实践证明,还是采用恒流控制的方式好。熔化高硼硅酸盐玻璃,每对电极经测算输入功率是78KVA,即电流600A,电压130V。当打开加料口加料时,炉内玻璃液温度下降,在反馈电阻的作用下,自动的改变恒流仪输出脉冲的频率,使可控硅的导通角改变,无级调压。使加在电极上的电压由130V自动上升到142V,以保证输入电流不变,从而达到玻璃液升温的要求。相反,如因某种原因造成长时间未加料,此时玻璃液的温度升高,电阻降低,恒流仪在反馈电阻的作用下,会自动改变输出脉冲的频率,改变可控硅的导通角,无级调压使输入电压降低,从而满足熔制工艺的温度要求。
6.变压器的设计选型
变压器的容量为160—250KVA,初级电压为380V,次级电压为180V—140V。电熔窑运行电压、电流及用欧姆定律算出的各种温度状态下玻璃液的电阻见表9.4.5。
表9.4.5 玻璃液电阻、电压、电流、温度的关系
玻璃液温度 |
电极电压 |
电流 |
玻璃液的电阻 |
1200℃ |
260V |
300A |
0.87Ω |
1300℃ |
195 V |
400 A |
0.49Ω |
1400℃ |
173 V |
450 A |
0.38Ω |
1500℃ |
142 V |
550 A |
0.26Ω |
1550℃ |
130 V |
600 A |
0.21Ω |
7.电熔窑耐火材料的选用
除流液洞和电极砖采用进口的ER1711电熔锆刚玉砖外、其它部位采用国产ZrO2含量33%的电熔锆刚玉砖。经一年多的使用,除发现流液洞砖侵蚀严重外,电极砖和池墙、池底砖侵蚀极微,上部火焰空间和炉盖的硅砖侵蚀不严重。加料处采用的是白泡石砖,由于烘炉不慎出现炸裂,使该处砖侵蚀严重。
8.热工测量和技术经济指标
表9.4.6 电熔窑的技术经济指标.玻璃液电阻、电压、电流、温度的关系。对电熔窑进行了热平衡计算,其结果示于表9.4.7。
表9.4.6
熔 化 池 |
熔化池面积 m2 |
1 |
熔化池深度 m |
1.2 | |
熔化率 T/m2.d |
1.2-1.4 | |
熔化池输入功率 Kw |
140-150 | |
熔化玻璃单耗 Kwh/Kg璃液 |
2.6-2.8 | |
熔化池空间温度 ℃ |
1180-1200 | |
熔化池玻璃液温度 ℃ |
1500 | |
工 作 池 |
工作池面积 m2 |
1 |
工作池输入功率 Kw |
60-64 | |
工作池单耗 Kwh/Kg璃液 |
1.3-1.5 | |
工作池燃料消耗 m3/d(天然气) |
211 | |
工作池空间温度℃ |
1220 |
表9.4.7
热量收入 |
100% | |
热量支出 |
熔化热效率 |
20.97% |
水冷却套热损失 |
13.07% | |
其它热损失 |
65.96% |
9.电熔窑的技术经济效益
⑴热效率高,节约能源。熔制硼硅酸盐玻璃时的热效率可达21%;而一般情况,这种小型熔炉以燃料加热时,其热效率仅为10~15%。
⑵减少挥发。以燃料加热熔制硼硅酸盐玻璃时,硼的挥发量达10~15%、而在电熔窑中仅为1%。
⑶ 熔制工艺稳定,控制简便可靠、调节灵敏、玻璃液质量好。全电熔玻璃熔窑,只要控制好进出料量、电压、电流等工艺参数,就可以控制到****熔制工艺状态。几年的实践证明,全电熔窑自动控制系统非常灵敏,稳定可靠。如需要提高熔化温度,只需调节恒流仪的给定值,几分钟之内,熔化温度就会达到所要求的温度。由于工艺参数稳定,从而使玻璃液的质量、产品的成品率都有了很大的提高。
⑷建炉周期短,占地少,无烟囱和蓄热室。该电熔窑结构简单,砌炉仅用10天,烤窑仅用6天。
⑸公害少,有利于环境保护。电熔窑噪声小,环境温度低,废气排放量少,每年可减少10。512T的废气排放量。
⑹全电熔窑与一般池窑技术经济指标对比
表9.4.8为硼硅酸盐玻璃电熔窑同天然气加热熔炉的对比。由表9.4.4可见,全电熔的熔化率可提高2~5倍,节能40%以上。
表9.4.8 技术经济指标对比(1)
项目 |
天然气池窑 |
电熔窑 |
对比结果 |
制品 |
95料 |
95料 |
|
熔化率 Kg/m2.d |
250 |
1140 |
提高350.5% |
能源消耗 标煤T/Kg玻璃 |
2.7 |
1.41 |
降低47.7% |
万元产值消耗 T/万元 |
12.68 |
6.02 |
降低52.34% |
T煤创税 元/标T煤 |
217.2 |
682.99 |
提高214.22% |
例2 日产150Kg高硅氧玻璃的电熔窑
高硅氧纤维的基础玻璃组成中,硼含量超过20%,属高硼硅酸盐玻璃系统。火焰窑中Na2O和B2O3的挥发量分别高达143%和76%,因此配合料中Na2O、B2O3的引入量分别为基础成份中的2.43倍和1.76倍。高硼玻璃(一般含B2O315%以上) 在高温下均有所谓的“硼反常”现象。
1.小型电熔窑的试验情况
(1)火焰窑、电熔窑熔化中Na2O和B2O3的挥发量及原料成本比较。用以熔制高硅氧玻璃的日产150公斤的小型电熔窑,与火焰窑进行对比。B2O3的挥发量仅为10%,Na2O为4%,因此生产每T玻璃的原料成本,仅硼酸一项可降低约40%。数据列于表9.4.9。
表9.4.9
窑型 |
B2O3含量% |
熔化每T玻璃的 原料成本(元/T) | ||
基础配方 |
实际引入量 |
挥发量 | ||
火焰窑 |
25.00 |
44.00 |
76.00 |
1985.60 |
电熔窑 |
25.00 |
27.50 |
10.00 |
1178.20 |
(2)电熔窑砖材选择。在小型电熔窑试验前,曾选用锆英石、石英砖、白泡石、锆刚玉及刚玉砖共五种砖材。分别置于1250℃、1320℃、1380℃和1430℃的高硅氧玻璃液中做静态侵蚀试验。结果认为锆刚玉砖最不耐侵蚀,且侵蚀产物浑浊,呈黑灰色。刚玉砖也较差,也有浑浊现象。锆英石虽然抗蚀性能好,但价格昂贵,其大型砖来源困难,也不宜选用。参考静态侵蚀试验结果,选用了石英砖和白泡石砌筑日产150公斤的小型电熔窑,底砖用一半石英砖与一半白泡石砖拼接,两侧与两端也分别用这二种砖对称砌筑,窑炉运行一个月零五天后,结果如表9.4.10。
表9.4.10
砖材 |
侵蚀速度(mm/月) |
砖材价格 | ||
熔化池最高温度点 |
三相界面处 |
流液洞处 | ||
石英砖 |
2.86 |
1.71 |
0.86 |
8420.00 |
白泡石 |
0.43 |
1.29 |
微量 |
100.00 |
由表9.4.10可见,二种砖材在三相界面处侵蚀速度相差不多,但在熔化池的最高温度点和流液洞处,白泡石比石英砖的抗蚀性要强得多。从经济上考虑,二者价格相差悬殊,选用白泡石能大大降低筑炉成本。
(3)火焰窑、电熔窑熔制的高硼料质量鉴定—拉丝作业测定。火焰窑、电熔窑熔制的高硼玻璃料,分别置于同品种纱的坩埚中(相当于标准坩埚)进行拉丝作业测定以直观地判断熔制质量。采用的漏咀孔径分别为1.6mm和1.4mm二种规格的200孔坩埚各一台,进行拉丝工艺测定。证明电熔高硼玻璃球的质量较火焰窑生产的球好得多,既降低拉丝成本,又大大提高劳动生产率。
(4)电熔窑的成本估计。一般地说,电熔窑的电力比火焰窑的燃料价格贵,但是由于火焰窑存在以下一些重大的不合理因素,因此球的成本相当高,价格昂贵,每T玻璃球成本价达5000元。①火焰窑的成型部采用12根硅碳棒加热,每天耗电5~6Kwh,且硅碳棒需经常更换;② 换热器采用进口不锈钢管,仅这项材料消耗费用约5万元;③ 窑体用石英砖砌筑,单价为白泡石的八十倍;④火焰窑面积熔化率低(仅0.175T/m2·d)提高了球的成本;⑤火焰窑的原料单耗达1985.60元/T玻璃,比电熔窑多800多元。根据以上各项对比分析,电熔窑生产的高硅氧球,其成本比火焰窑降低约20~25%左右。
2.采取的几项技术措施
(1)石英砂的颗粒度与含铁量的控制。上面提到由于高硼料易挥发份含量高,宜采用“速熔”,不宜让玻璃液在窑内长时间停留。在配合料方面,降低石英砂的颗粒度。分别取60目和120目的石英砂作原料,各配置200g配合料分别投入铂坩埚中熔融,以粉料全部加完的时间为“零”起算,每隔15分钟取样观察,对比结果如表9.4.11。由此可见,用120目细砂,它的成丝和砂粒基本消失,所花时间都比用60目粗砂快约一小时左右。由于砂子颗粒度小,引入的铁含量也随之略为提高,能控制在0.2%以下,并对产品性能没有不良影响,相反对拉丝性能反而有利,因此确定熔化高硼玻璃的石英粉细度应控制在120目左右。玻璃中铁含量范围为小于0.2%。
表9.4.11
种类 |
成丝所用时间(分) |
砂粒消失所用时间(分) |
120目细砂 |
35 |
110 |
60目细砂 |
95 |
170 |
(2)配合料的混合。小型电熔窑试验采用干法混料,在窑的后期将配合料加水做成料团投入窑内作对比,测定其硼含量如表9.4.12。根据测定结果,配合料含水率高,水蒸汽延迟挥发性硼酸的分解,因而增大了B2O3的损失,因此配合料尽量不含水或者水分控制在5%左右为好。
表9.4.12
日期 |
加料方 式 |
玻璃配方 % | ||||
SiO2 |
Al2O3 |
Fe2O3 |
CaO/MgO |
B2O3 | ||
10.22 |
干粉 |
66.22 |
1.09 |
0.18 |
0.38 |
23.42 |
10.25 |
料团 |
66.33 |
1.09 |
0.17 |
0.38 |
23.23 |
10.28 |
料团 |
66.78 |
1.05 |
0.14 |
0.32 |
23.05 |
(3)熔制温度控制适当。在小型电熔窑试验中,做过改变熔制温度的试验,经对应的拉丝试验表明,高硼料的熔制温度一般控制在1450℃以下为宜,温度过高,耐火材料侵蚀严重,拉丝断头率将明显升高。
(4)合理确定电熔窑的面积熔化率。一般说来,熔窑的面积熔化率取得低一些,对玻璃液的熔化和澄清是有利的。但对高硼料来说,玻璃液在窑中停留超过一定的时间,反而不利,既增大成分波动,又影响质量。在小型电熔窑试验中曾做过加大出料量的试验(相应提高电功率),使面积熔化率先后达0.7、 0.91和1.1以上。并将熔制的料块分别置于100孔坩埚中进行拉丝试验。从拉丝效果来看,面积熔化率低于0.9T/m2·d以下,料块质量均能满足拉丝要求,面积熔化率高于1.1T/m2·d,质量明显下降,影响拉丝。由此可见,在电熔窑中适当地提高面积熔化率,不会使玻璃球质量变坏,相反,面积熔化率过高或过低均会影响熔制质量。
属高硼硅玻璃的高硅氧球,采用白泡石砌筑的电熔窑熔制,从其玻璃的熔制特性与要求出发,严格控制原料的颗粒度、配合料的水分及合理控制其熔制工艺参数,熔制出的玻璃球质量比火焰窑生产的球质量大大提高,基本上能满足拉丝工艺的要求。改变以往拉丝环节作业很不稳定的局面,断头率减少约70%,飞丝率减少16~35%,产量至少能提高50%,拉丝率可提高到84%。
例3 日产1.4~1.8T硼硅玻璃的电熔窑
图9.4.4为玻璃电熔窑的纵剖面图,该电熔窑用于生产手工成型的玻璃C48—2制品和颗粒产品,玻璃液的日产量为1.4~1.8T。炉子由熔化池、澄清池、流液洞、工作池、垂直上升道组成。
熔化池装有二排四对无水冷板状钼电极和带有钼套管的热电偶。流液洞的隔墙中装有钼板(垂直固定在隔墙中)。流液洞的这种结构既可防止盖板砖腐蚀产物进入到玻璃液的生产流中,又可防止窑炉在运转时由于隔墙损坏未熔化好的玻璃液从熔化池进入工作池。
工作池设有溢料口,用于保持玻璃液面的稳定。与自动加料机结合确保电熔窑物料的平衡。熔化池、澄清池使用AZS41,流液洞使用熔融石英砖,上部结构使用AZS33作为窑炉砌体的耐火材料。
窑炉采用三相电源供电、自动控制。下面的两对电极与一个单相变压器连接,而上面的每对电极与单独的单相变压器连接。
相邻电极对边缘之间的距离是对置电极对之间距离的0.25倍。根据玻璃成分和窑炉的工作状况,可以改变电极对与变压器的连接方法。加料机可自动控制,也可手工操作。
电熔窑的技术性能,见表9.4.13
表9.4.13
出料量 |
T/d |
1.4~1.8 |
熔化池面积 |
m2 |
0.96 |
玻璃液的最高温度 |
℃ |
1540 |
玻璃液的熔化率 |
T/ m2.d |
1.46~1.88 |
玻璃单耗 |
Kw·h |
1.5 |
工作池的温度 |
℃ |
1280~1320 |
挑出有条纹废品 |
% |
30~35 |
手工成型的合格率 |
% |
36~45 |
颗粒产品的合格率 |
% |
95~98 |
硼酸的挥发损失 |
% |
不超过1 |
在熔化池池中玻璃液最高温度 1560~1580℃时,决定电熔窑使用寿命是池墙砖的使用期限(图9.4.5)。
表9.4.14中列举用于生产C48—2玻璃压制品的电熔窑用不同耐火材料时玻璃电熔窑的使用寿命。
上述结构的玻璃电熔窑使用了12个月,保证手工成型C48—2玻璃合格品率稳定。用玻璃电熔窑也可以组织生产手工成型C52—1玻璃制品。
表9.4.14
耐火 材料 |
电熔窑的寿命(月) | |
保温 |
不保温 | |
AZS33 |
8 |
|
AZS41 |
11 |
16 |
例4 熔化无碱铝硼硅酸盐玻璃的小型电熔窑
该电熔窑熔化无碱铝硼硅酸盐玻璃(成分C48—5)。熔化池的尺寸为500mm×500mm×500mm,配有一对板状钼电极,板状钼电极之间的距离d=400 mm。电熔窑的一些运行参数见表1.0.4.15
指标 |
实验参数 | ||||
实验1 |
实验2 |
实验3 |
实验4 |
实验5 | |
冷料毯的温度(℃) |
400-500 |
120 |
100 |
100 |
120 |
电熔窑的熔化率(T/m2.d) |
0.64 |
0.85 |
1.07 |
1.25 |
1.2 |
玻璃中的气泡数(个/公斤) |
8-12 |
8-12 |
30-40 |
多 |
5-6 |
冷料毯下沿至1485℃面上的距离(mm) |
100 |
46 |
10 |
120 |
30 |
在900-1485℃范围内温度梯度(℃/mm) |
5.8 |
12.6 |
8.3 |
4.8 |
19.3 |
冷料毯下沿至电极上沿的距离(h1 mm) |
80 |
46 |
30 |
15 |
40 |
h1/电极间距d |
0.2 |
0.115 |
0.75 |
0.0375 |
0.1 |
熔化池最高温度(℃) |
1485±5 |
1485±5 |
1485±5 |
1485±5 |
1535±5 |
熔化池运行功率(Kw) |
48 |
48 |
48 |
48 |
52 |
1.电熔窑的运行结果
⑴在实验4观察到未熔石英微粒。这是由于实验4中,窑炉出料量大于允许值(在一定电功率条件下),最高温度向熔化池深层位移所致。
⑵由于熔化率的提高超过了一定值,玻璃液中气泡数目增加了。这是由于随着玻璃液流速度的加快,玻璃液在熔化池高温区的逗留时间缩短的缘故。因此,要使电熔窑的熔化率达到较高的值,务必增加电熔窑高温区的高度,以使玻璃液流在电熔窑内的逗留足够时间,使玻璃液完全澄清。
2.沿熔化池池深的温度分布
沿熔化池池深的温度分布见图9.4.6。其它电熔窑的一些运行参数见表9.4.16。
表9.4.16
玻璃 品种 |
出料 量(T) |
体积熔化 率(T/m3d) |
高温区的 深度(m) |
玻璃液在高温区 的留时间(小时) |
C52-1 |
0.65 |
2.6 |
0.85 |
18.0 |
C52-1 |
5.6 |
1.8 |
0.6 |
18.5 |
C48-5 |
1.8 |
0.57 |
0.2 |
19.4 |
C48-5 |
2.6 |
0.83 |
0.3 |
20.2 |
C89-2 |
0.5 |
1.19 |
0.4 |
18.7 |
C89-2 |
7 |
2.26 |
0.75 |
18.5 |
例5 日产25T和40T的高硼硅玻璃的电熔窑
高粘度难熔的硼硅酸盐玻璃(C52—1、C40—1、派勒克斯)制品的机械化成型得到了广泛的应用。由于对玻璃液的电阻、耐火材料在电熔窑中的使用,电极的****分布,结构设计等多方面的研究,高硼硅酸盐玻璃的电熔窑已得到广泛的应用。
但生产过程中常产生下列现象:(1) 当窑炉产量稳定、电气参数和操作温度不变时,玻璃液的粘度产生波动。(2)尽管玻璃液是在非常高的温度下熔制的,但在制品中出现未熔化的石英颗粒。(3) 在成品中经常存在灰泡和小气泡。
为确定产生上述现象的原因,研究了在熔化池只有一排板状电极的冷炉顶的两座单相电熔窑的运行情况。
电熔窑用于熔制难熔的硼硅酸盐玻璃C40—1,用机器生产气体放电灯的外壳。电熔窑的特性列于表9.4.17,电熔窑(No2)的结构见图9.4.7。两座电熔窑熔化池池墙不进行保温。
上述现象取决于在电熔窑中形成的玻璃液流的特性。通过玻璃液的电流的大小取决于温度和熔体的电阻率ρ。难熔玻璃熔体具有高的电阻率,尤其是在低温条件下,因此熔体具有高的自调能力。这样,电熔时会引起熔化池玻璃液加热不均。
1.玻璃液流的研究
为研究玻璃液流采取了如下方法。将石英杆、石英管放入玻璃液中,根据倾斜角度判断液流的方向和速度,熔化池内玻璃液液流的情景如图9.4.7所示。说明在玻璃液中存在温度和粘度不相同的区域。
温度最高的玻璃液位于电熔窑的中心和电极的附近。流液洞对面、流液洞上方的玻璃液具有较低的温度(图9.4.8)。温度最高与温度最低区域的表面玻璃液粘度之差等于0.6。
因此,熔化池形成了若干个温度区和粘度区,在1000mm深处为如图9.4.9所示。从而导致配合料和碎玻璃混合料不同的熔化速度。
表9.4.17
序 号 |
指标 |
电熔窑 | |
NO1 |
NO2 | ||
1 |
板状电极对数 |
4 |
6 |
2 |
熔化池的尺寸(长、宽、高)m |
2.2×2.2×1.6 |
3.6×2.2×1.6 |
3 |
熔化池面积 m2 |
7.04 |
11.52 |
4. |
整个窑炉的面积 m2 |
7.34 |
12.0 |
5 |
熔化池的容量 吨 |
25.0 |
40.0 |
6 |
整个窑炉的容量 吨 |
26.0 |
43.0 |
7 |
熔化率 吨/ m2. |
1.7 |
1.4 |
8 |
电熔窑的电功率 Kw |
800 |
1410 |
9 |
能耗 Kw.h/Kg玻璃 |
1.6 |
2.1 |
10 |
电极的电流密度 A/cm2 |
0.177 |
0.2 |
2.电熔窑中产生制品缺陷的原因
(1)温度制度的波动, 在电熔窑中心和电极附近,熔化速度高于流液洞池壁和流液洞对面的熔化速度。这是所有大容量和高生产能力电熔窑(板状电极)都有的现象,它要求严格遵守熔制工艺。在熔化池的个别地方,稍为偏离所规定的温度和粘度,均会导致玻璃液粘度的波动和制品中方石英颗粒缺陷。
(2)产生制品缺陷的另一原因是高温下玻璃液与电熔锆刚玉耐火材料互相作用形成。化学不均匀的玻璃液从池壁、池底进入到生产流中,这种玻璃液中ZrO2和Al2O3的密度要比玻璃成分中高0.1~0.3g/cm3。
(3)微量铁可能连同碎玻璃一起装入电熔窑中,铁熔化后使整个池底均匀地盖上一层薄膜,渗入到砖缝中,改变了电场的分布。此时,在具有一排电极的电熔窑中表现明显的弱温区消失或者移向最底部,取消了液流的再次循环,造成电熔窑熔化池底层玻璃液的过热。
(4)采用具有一排电极的电熔窑,玻璃熔化速度、玻璃液在窑炉内的滞留时间、窑炉的出料量必须相适应。若违反这个原则,难熔玻璃的熔化速度和在熔化区的滞留时间可能是不足,或者是过长。在前一种情况下,冷料层过厚,温度场和低温区移向底部,未澄清的、具有不同粘度的玻璃液进入生产流中,从而导致其成型性能的变化。在后一种情况下,温度场向上移动,冷料层实际上没有形成。投入的碎玻璃首先与纯碱反应,结果纯碱不是与配合料形成熔融物。玻璃液中气体产生高分压,使气泡生长并迅速上升。在玻璃液面上产生厚20~30mm粘稠的玻璃液的表层,气体聚集在它的下面并溶解在玻璃液中。此时气体以灰泡和小气泡形式进入到生产流中。被溶解的气体的成分列入表9.4.18中。
表9.4.18
电熔窑 |
气体成分%(体积) |
气体数量 ml/100g玻璃 | |||
CO2 |
CO+N2 |
H2 |
H2O | ||
NO1 |
2.70 |
18.90 |
17.00 |
61.40 |
0.617 |
NO2 |
2.44 |
19.65 |
14.03 |
63.88 |
0.721 |
(5)产生渣壳的原因,当玻壳成型时,C40—1玻璃粘度对数等于3.5—3.7。而当粘度对数为2时,灰泡和气泡已无能力从硼硅酸盐玻璃中消除。与火焰窑比较,玻璃液中气体含量较高,说明高粘度难熔玻璃电熔时在表层下面形成较高的压力。
表皮层的形成可在粉料与碎玻璃熔体的界面上。产生这种情况的原因是由于加入的配合料湿度较高、熔体的边界层过冷、结合水从硼酸和碳酸钾中除去、以及加入了湿的大颗粒碎玻璃的结果。这种碎玻璃不能与配合料迅速起反应,在软化时形成表皮壳。因此必须重视配合料的制备。并且使熔制的最高温度区接近于玻璃液表面(见图9.4.8中的曲线3),流液洞池壁保温对于区域3(图9.4.9)的温度均衡,并使其接近区域2的温度会产生有益的影响。这可以使玻璃液工作流中灰泡和气泡数量减少。
为了证实灰泡和气泡形成原因,在点3(图9.4.7)从深度处取样。把直径30mm的长石英管放入玻璃液最底部。将石英管保持若干时间,然后将石英管的上部用塞子塞上,从熔体中迅速取出并置于纯净的金属垫板上。冷却后利用放大镜沿试样的全长观察石英管中的玻璃。
硬渣壳的玻璃液中取出的试样气泡数量要比以配合料和碎玻璃复盖的玻璃液中的气泡多。这说明,在表面上具有硬渣壳的玻璃液中,溶解和保留了更多的气体。
(6)在难熔玻璃的熔制过程中,不允许玻璃液在进入供料机过程中和在供料机中二次加热玻璃液。否则会导致二次灰泡和气泡的产生。
用于熔制C40—1玻璃的电熔窑的****熔化率为1.6~1.8T/d.m2。在设计熔制高粘度的难熔玻璃所采用的电熔窑时,必须考虑到它们的总产量、单位产量、玻璃液的熔化速度、高温区的滞留时间,必须预料到电熔窑(各个区)电工参数的调整。流液洞壁应进行保温。为避免硬渣壳在玻璃液面上形成,碎玻璃必须粉碎、干燥与与配合料混合均匀。电熔窑应由氧化法生产的电熔锆刚玉耐火材料砌筑。
例6 生产派来克斯硬质玻璃的电熔窑
用小型火焰窑熔制硬质玻璃是困难的,不易获得质量好的玻璃。生产派莱克斯7740、玻璃王32一级品硬质玻璃,无论是在技术上,或是成本上都有问题。用坩埚窑仅限于熔制二级品的膨胀系数46×10-7左右的硬质玻璃。
熔制硬质玻璃的电熔窑,其窑结构如图9.4.10所示,电熔窑采用冷炉顶,使用板状钼电极。在电极附近温度最高,底部约降低150℃。电极的上部,直到冷顶处温度大幅度降低。
日产2吨玻璃的电熔窑,平均每公斤玻璃的耗电量是2.6Kwh,这仅是火焰窑耗热量的四分之一。
就日产2.5~6.0吨玻璃的电熔窑,平均每公斤玻璃的耗电量是2.2~2.7KWh,可获得高质量的玻璃。
表9.4.19为日出料量500Kg的日池窑熔制硬质玻璃的热工测定的数据。输入熔化池和工作池的电力比例是53∶47,几乎相等。散热量约为34%,****的热损失来自于料层表面。采用冷炉顶方式,表面温度低,热损失约为2%。电极冷却水的损失热为7.6%。
表9.4.19日产量500公斤的日池炉熔制硬质玻璃的热工测定的数据
热量收入 |
热量支出 | ||||
部位 |
热量(Kcal/h) |
占的比例% |
部位 |
热量(Kcal/h) |
占的比例% |
熔化池 |
21758 |
53.0 |
池壁损失 |
13988 |
34.1 |
工作池 |
19264 |
47.0 |
工作口 |
5920 |
14.4 |
料毯表面 |
820 |
2.0 | |||
电极冷却水 |
3098 |
7.6 | |||
玻璃熔化热 |
5686 |
13.8 | |||
其它 |
11506 |
28.0 | |||
合计 |
41022 |
100 |
合计 |
41022 |
100 |
此页网址为:
相关文章