工程分类
更多>>![]() |
|
![]() |
|
![]() |
|
![]() |
|
![]() |
|
![]() |
|
![]() |
|
![]() |
|
![]() |
|
![]() |
|
![]() |
|
![]() |
|
![]() |
|
![]() |
|
![]() |
|
![]() |
|
![]() |
|
![]() |
|
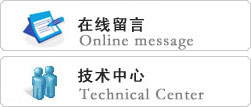
联系人:
电话:0511-88791451
手机:13951280541
邮箱:jfchen@ujs.edu.cn
地址:镇江市学府路80号
最新文章
您的位置:网站首页 > 最新文章熔制氟乳浊玻璃的电熔窑
乳白玻璃一般都含有大量极易挥发的组分,如氟化物等。在常规火焰加热的熔窑中,当火焰掠过玻璃液表面时,就会有相当数量的挥发性成分被带走,经过烟道,升入烟囱跑掉,既损失了大量的宝贵原料,又造成了空气污染。同时,由于挥发损失,使得表层玻璃在成分上变得与其下面的深层玻璃差异很大,结果造成了玻璃成分的不均匀。当采用全电熔工艺时,热量是在配合料下面释放出来的,各配合料组分产生的气体要通过配合料层向上逸出。由于配合料温度较低,各挥发分的气体就会凝聚在冷的配合料中,而不会挥发掉,从而使通过流液洞流出的玻璃液能与投入熔窑的配合料在成分上基本保持一致,而使产品的化学成分稳定。另一方面,由于减少了挥发,节约了宝贵的原料,从而使原料成本降低。在常规燃料火焰加热的情况下,配合料中氟化物有大约40%因挥发而损失掉。而采用全电熔时,氟化物的挥发量仅为2%。
例1 日产300Kg玻璃马赛克的电熔窑
玻璃马赛克熔体是含有大量未熔砂粒与气泡的不完全熔融的玻璃液,其熔体性能与一般玻璃液有着显著的差异。
根据马赛克的生产特点和电熔窑的操作要求,设计一座日熔化量300Kg的模拟电熔窑。主要参数如下:①电熔窑装机功率15kW;②料道装机功率8kW;③最高熔化温度1350℃;④最高出料温度1200℃;⑤熔化池面积0.138m2,池深460mm。
该试验窑的运行,获得了较为理想的电熔玻璃马赛克样品,下面分六个方面进行总结。
1.玻璃马赛克熔体在电熔窑中的流动性
试验结果表明,当料道空间维持在适当的温度时,半熔融态的玻璃马赛克熔体可以形成连续自然流股,不致在料道口堵塞;熔化池向料道供料的能力则主要取决于两处的液位差,在电熔窑设计中这是保证连续供料的一个关键结构尺寸。
2.玻璃马赛克熔体的电熔性能
经过与特定白色玻璃液的比较试验得知,当参比温度(非实际温度)1000℃时,白色玻璃的相对电阻大致为0.36,而白色玻璃马赛克的相对电阻大致为0.60(见图9.5.1)。经测算得出,在选择适当的结构设计方案后,可使玻璃马赛克全电熔池窑的正常工作电压低于150V,经过上升道和料道后的流程降压,在出料端的对地电位可控制在30V以下,进行可靠的接地处理后是相当安全的。另一方面,由于相对电阻较高,较小的熔化池和电极就可以送入较大的功率,这正好与玻璃马赛克熔化周期短,熔化能量需要集中的特点相一致。
3.玻璃马赛克的电熔窑的温度制度
试验结果表明,当采用冷顶加热方式时,电熔玻璃马赛克的熔制温度只需要在1200℃左右,料毯的表面温度只有100℃左右,基本上消除了氟化物的挥发。
4.生产玻璃马赛克电熔窑的熔化率
该窑平均每小时出料量18.50Kg(面积熔化率3.2T/m2·d)。扣除因变压器输出功率不足造成欠产的因素,平均每小时出料量19.72Kg(面积熔化率3.4T/m2·d)。试验取得的****出料量为23.6Kg/h(面积熔化率5.15T/m2·d)。
5.生产玻璃马赛克电熔窑的单位能耗
该窑采用了冷顶电熔和无水冷电极保护技术,电熔窑的熔化热效率为75%。当电熔窑出料量为18.50Kg/h,单位电耗0.65kW·h/Kg玻璃液。当出料量为19.72Kg/h,单位电耗0.61kW·h/.Kg玻璃液。
6. 电熔工艺对玻璃马赛克砂感的影响
由于电熔窑中能量密度高,熔化强度高,熔化历程短,细小的砂粒会迅速熔掉。因此,要保证产品具有良好的砂感,原料的粒度需尽可能稳定一致。试验结果表明:当石英砂、长石等矿物原料的粒度为40~70目时,砂感最好;当粒度大多数在100目以下时,砂感不明显;当粒度在20目以上时,会影响外观质量。另外,熔制温度与出料量的匹配调节也是一个技术关键,这一问题比火焰熔窑更为突出。当熔化温度偏高或出料量过低时都会显著地影响砂感。因此,作业制度稳定合理至关重要。
例2 日产7吨氟化物玻璃的电熔窑
该窑采取冷顶垂直熔化,窑体多层保温、干式水冷电极保护、玻璃液直接测温、集成电路可控硅自动控温,年产30万平方米玻璃马赛克。有关情况总结如下。
电熔窑采用地上结构,熔窑****高度5m,熔窑主体高3.5m。厂房基础未加固,适当加固了窑底钢结构。
如图9.5.2电熔窑采用六角形结构,熔化面积2m2,池深1200mm。熔化池全部采用国产的AZS耐火材料,池底采用AZS贴面和捣打料,整个窑体采用了全封闭式保温,底部保温层厚900mm,池壁保温层厚600mm,外壳为钢板,以减少窑体的热散失。设计窑龄10~12个月。
电熔窑熔化池采取冷顶加料,配合料层复盖在高温玻璃液面。料道采用滴料式供料,并设有流量调节装置。
电极采取三角形布置,选用钼电极。采用无水冷电极保护,保护部位更加可靠,运行一个窑期(11个月)仍基本完好,可继续使用一个窑期。
电熔窑主电极采用三相供电,电源平衡,不影响电网供电质量,有利于电源变压器功率因数的提高。电熔窑的装机功率250kW,电熔窑的控温系统采用先变流后调控的方案,消除可控硅与感性负载配合使用产生的高次谐波,避免对电网和可控硅的电流冲击,提高变压器的工作效率。
控制系统全部采用集成电路,整个控制线路集中于一块线路板上,可靠性高,一旦出现故障,整板更换,不影响生产。整个系统具有软启动功能,无启动冲击电流,可连续平稳调压,手动给定自动恒流,还具有过流声光报警,自动过流保护,温度自动调节,显示记录。
玻璃液直接测温,经过特殊保护处理的热电偶可灵敏地反映窑内温度变化,而不受电熔作业的电干扰。
投产一年多,设备运行正常,成品率达到85%以上,单位熔化电耗约0.7kW·h/Kg玻璃液,****熔化量可接近9T,最低单位熔化电耗仅0.54kW·h/Kg玻璃液。
该窑的技术特点:
(1)熔制气氛稳定、产品色差小 电熔窑中的气氛不受大气和火焰的影响,这为彩色制品的熔制提供了极为方便的条件。一般火焰窑生产红色系列产品时往往色泽多变、色差大、难以稳定,成品率较低,而电熔工艺生产时,一次投料即可稳定生产、色差很小。
(2)占地面积小,土建要求低 该技术中全电熔池窑的占地面积视生产规模不同为8~16m2,而且设备重量轻,高度低,厂房只需一层结构(主车间高6m)即可,并且基础不需特殊处理。
(3)一次投资省,冷修费用低 全电熔池窑冷修时,只需要更换池窑内衬和电极,冷修施工只需6~10天,冷修费用只占生产成本5%以下。
(4)生产规模灵活、适应面宽 对于玻璃马赛克这个多色彩品种的产品来说,小规模电熔窑可有效地解决频繁换色带来的问题。
(5)建设周期短,经济效益显著 全电熔池窑生产线的设备材料齐全后,30~40天即可完成设备安装和烤窑调试工作。一般自现场考察确定方案后90~120天即可投产。以该窑年30万m2的玻璃马赛克全电熔池窑生产线为例,其设备投资为65万元,可创年利税95万元,设备投资回收期为8.2个月。
例3 日产4-6T氟乳浊玻璃的电熔窑
图9.5.3为日产4~6吨氟乳浊玻璃的电熔窑示意图。使用园形板状钼电极,电极的冷却采用压缩空气喷水降温方式,熔化池的形状为六角型,用钼电极三相交流加热。窑内最高温度达1450℃,一天的耗电量约为7200Kwh,平均每公斤玻璃1.8Kwh。可节省40%的氟化物原料。熔化池温度分布如表9.5.1所示。加入冰晶石为乳浊剂,电熔窑和坩埚窑比较其挥发量的结果如表9.5.2。
表9.5.1
距表面的深度(cm) |
10 |
15 |
20 |
25 |
30 |
35 |
底部 |
中心带的温度(℃) |
920 |
1200 |
1440 |
1440 |
1420 |
1400 |
1300 |
表9.5.2
炉 型 |
F-含量 |
氟挥 发量 | |
计算值 |
熔化后 | ||
电熔窑 |
2.65 |
2.44 |
7.9 |
电熔窑 |
2.5 |
2.24 |
7.6 |
坩埚炉 |
3,4 |
2.85 |
16.1 |
坩埚炉 |
3.4 |
3.09 |
9.3 |
电熔窑挥发了7~8%,而坩埚窑大致在9~16%之间。因此,电熔窑挥发量少,质量稳定。通常火焰窑氟化物的损失为40%,而电熔窑只损失2%。
例4 日产3T氟乳浊玻璃的电熔窑
某厂运用了电熔工艺熔制氟乳白玻璃,生产能力为3T/d,有三排电极。电熔窑熔制了用硫化镉着色的有色玻璃和乳白的氟玻璃。玻璃的配方(重量%)见表9.5.3
表9.5.3
种类 配方 |
Si2O |
Na2O |
K2O |
Al2O3 |
CaO |
F- |
CdS* |
C4H6O6* |
黄乳浊玻璃 |
64.8 |
15.3 |
5.9 |
1.9 |
7.9 |
4.2 |
1 |
0.5 |
乳白玻璃 |
66.8 |
15.3 |
2.9 |
4.8 |
5.9 |
4.3 |
0.5 |
*—在100%的配合料中另外添加。
在生产黄玻璃管后,再熔制乳白玻璃。换料时Al2O3由0%调到3%;ZnO由0%调到6%,换料过程中玻璃具有不均匀的特点,在退火时开裂,乳浊度也不均匀,成形时炸裂增加。在玻璃板的表面看到有以前玻璃成份的条纹。从条纹分布判断,这种玻璃沿着供料道底部移动,从而说明在窑的底层存在停滞区。熔化乳白玻璃时要考虑保持冷料层的****厚度(10cm),在表9.5.4中列出熔制的工艺参数。
表9.5.4
玻璃种类 |
生产能力(T/D) |
电耗(Kwh/Kg玻璃) |
各层电极功率(Kw) |
上层、下层电极的负荷比 |
窑炉的热效率 | ||
上层 |
下层 | ||||||
玻 管 |
带粗结晶的 |
1.62 |
1.13 |
23 |
54 |
1:2 |
61.9 |
质量好的 |
1.62 |
1.57 |
13 |
102 |
1:9 |
44.4 | |
优质乳浊装饰玻璃 |
2.81 |
1.16 |
28 |
92 |
1:3 |
60.1 |
除了在玻璃板和玻璃管的表面带有黄色斑纹之外,还同时观察到在表面有粗糙的结晶,个别为球形,****尺寸1~2mm,其数量在玻璃成份改动后大量增加,可以认为是料道内玻璃的析晶,这是由于熔融体冷却低于液相线温度而造成的。分析从料道不同点上所取试样,玻璃液的析晶在流液洞出口处已经出现,随着熔体流到料道而渐渐加强。全息X射线和电子显微镜分析,除NaF和CaF2析晶外,在结晶的玻璃里还出现方石英晶体,这表明玻璃液在低温区停滞过长。
1.寻找解决析晶的方法
为了消除析晶过程,料道温度从900℃提高到950℃,此外在工作池的深处装有粘土质的搅拌器,但并没有收到明显的效果,玻璃析晶仍然存在。
熔制乳白玻璃实践表明,玻璃中引入氧化铝可降低熔体失透的倾向。用氧化锌代替氧化钙可减少粗大的析晶。为此在基本组分中引入Al2O3和ZnO去取代CaO。
2.使用密度分析和电子显微镜的方法找原因
调整玻璃配方提高了玻璃白度,但在连续生产十天之后,又观察到玻璃结晶。其原因可能是不合理的熔化制度,导致玻璃液在熔化池停滞区析晶和不规则的玻璃液对流析晶。
对料毯下50mm的深层玻璃试样密度的测定表明:最小的密度为2.4925~2.4930g/cm3,处在带粉料的熔融体上层。这是由于局部存在没有熔化好的配合料和气体杂质所至。****密度的玻璃为2.4961~2.4963g/cm3,在深度为15~20cm的中层。靠近池底65cm的深层玻璃的密度则又降低到2.4942g/cm3。
玻璃试样的电子显微镜表明:上层的熔融体除均匀的玻璃相以外,还含有没有熔化的配合料粒子和良好的针状外形的微晶,这显然是玻璃失透的结果。
玻璃液下15~40mm深处有较好的混浊特性。这层玻璃结构为不同尺寸的偏析微粒组成。底层玻璃液有不均匀的特征。这里也有析晶,还包含有微析晶杂质。
电子显微镜对同一个垂直方向上不同液深的试样分析表明,其上层和底层玻璃在结构上有明显的相似。这表明:上层带有残余的未化好的玻璃液沿纵向池壁进入了底部,影响成形的区域。
3.解决方法:改变电极的负荷比
为了合理地调节对流和改善熔制,电熔的功率由77Kw增加到115Kw,并且由下层电极引入102Kw。上层电极功率选择13Kw(见表9.5.4),主要考虑保持一定冷料层厚度(不大于8cm)。这样的功率分布能够变成深层熔制,改善从下层上升的玻璃液流。它阻碍了冷的玻璃液较快的向池底流动,从而增加玻璃液的熔制时间。
沿窑炉轴向离料毯50mm处的深层玻璃液温度测定表明,功率分配变化引起料毯下10~40cm深处的熔体温度提高100—200℃(图9.5.4)。
熔制制度改变后一天,产品析晶完全消失,玻璃试样的化学分析表明,氟的总挥发损失为引入量的4.5~5%。
当窑炉的生产能力由1.6T/d增加到2.5T/d时,电流也需跟着改变,由于配合料层过厚和排气困难,上层电极的功率由13kW增加到23kW。
电极的负荷比,在选择热工制度上起到重要的作用,如在第一排和第二排电极送入的功率比为1∶2,单耗为1.13Kw/Kg玻璃时,得到的玻璃质量并不好。几乎在同样的电耗下(1.16Kw/Kg玻璃),负荷比例改为1∶3时,就熔制出好的玻璃。停炉时,电极从热的玻璃液中拔出并进行了称量,在窑中心安装的电极损耗****,因为中间电极的电流密度远大于边部电极的电流密度,靠流液洞的上层电极又比加投料一测的损耗要大,靠加料口的下层电极的侵蚀大致一样。
虽然上层熔体温度不高,负荷较低,但上层电极的钼总损耗要大于下层,这显然可以解释为它们与配合料很近。
表9.5.5列出所有12根电极的损耗资料,每熔制1Kg的玻璃液平均为0.24g。
表9.5.5
窑炉中电极的位置 |
电极直径mm |
****电流A |
电流密度A/cm2 |
每根电极的损耗Kg |
电极的损耗Kg/Kg玻璃 | |
上层 |
靠流液洞 |
38 |
1100 |
1.50 |
8.4 |
0.033 |
中间 |
45 |
2050 |
2.31 |
12.4 |
0.080 | |
靠加料口 |
38 |
450 |
1.30 |
4.6 |
0.029 | |
下层 |
靠流液洞 |
38 |
600 |
0.82 |
3.1 |
0.020 |
中间 |
45 |
1450 |
1.64 |
9.4 |
0.060 | |
靠加料口 |
38 |
850 |
1.17 |
3.0 |
0.019 |
例5 日产0.5-1.5T乳白玻璃的电熔窑
1.乳白玻璃的玻璃成分
电熔窑熔化乳白玻璃的化学成分有五种,分别列于表9.5.6。从表9.5.6中可以看出,五个配方的Na2O和K2O含量差别很大,这对生产出来的乳白玻璃的导电性能产生较大的影响,同时也将限制钼电极电流强度的增加,因此通过钼电极的电流强度不得超过0.7A/cm2。
表9.5.6. 五家工厂的乳白玻璃成分
配方编号 |
玻璃中重量百分比% | ||||||
SiO2 |
CaO |
Na2O |
K2O |
Al2O3 |
ZnO |
F- | |
NO1 |
67.0 |
7.6 |
9.5 |
7.5 |
4.0 |
2.0 |
5.0 |
NO2 |
67.3 |
7.5 |
11.0 |
4.0 |
5.2 |
5.0 | |
NO3 |
67.2 |
4.1 |
12.0 |
5.0 |
4.5 |
2.0 |
5.0 |
NO4 |
67.5 |
5.5 |
11.5 |
4.0 |
4.5 |
2.0 |
5.0 |
NO5 |
67.5 |
5.0 |
13.4 |
3.0 |
6.0 |
5.0 |
2.电熔窑的结构
熔化乳白玻璃的小型电熔窑的日熔化量0.5T到1.5T。日出料量不同的电熔窑的结构基本相同(见图9.5.5),所不同的是日出料量0.5T的电熔窑有两对钼电极,日出料量1T和1.5T的电熔窑分别有三对和四对钼电极,其它各部尺寸相应扩大。该电熔窑有一个熔化池和一个澄清池,中间有流液洞相连。熔化池内安装钼电极的位置很重要,既要保证熔化池配合料完全熔化又不影响玻璃液的流动。
3.钼电极的电流密度
小型电熔窑熔化乳白玻璃,钼电极电流密度的变化范围是0.5~1.20A/cm2。电流密度超过1.2A/cm2时,就会在乳白玻璃制品中出现黄褐色条纹和黄色或咖啡色气泡。放射光谱分析表明:这些黄褐色条纹是由于在乳白玻璃中含有大量的铁和钼造成的。此外,还发现了带有金属光泽的金属小球体,进行化学分析表明,在这些金属小球体内含有大量的MoO3、MoS和其它化合物。在乳白玻璃的黄褐色气泡内凝聚着黄色或咖啡色沉积物。对上述这些化合物和沉积物的综合显微偏振光分析和X光分析表明,这里沉积着MoO、MoS、NaF、CaF2、SrF2。综上所述,乳白玻璃产生上述废品的原因是因为玻璃液与钼电极相互作用造成的。
钼电极在乳白玻璃液中侵蚀加速的原因是由于玻璃液中含有硫化物(平均含0.3%SO3)和铁(约0.06%Fe2O3)。钼电极在电熔窑内处于还原性气氛中,那么形成铁和钼的硫化物的可能性大大增加。为了避免上述情况发生,有必要在玻璃成分中引入2%的氧化锌以替代氧化锶,另外再加入少量的硝酸钾以增加0.5%的氧化钾。要严格地把钼电极的电流密度控制在1.1A/cm2以下,这样就防止出现上述废品。
4.各种电熔窑的工艺技术参数
各种型号熔化乳白玻璃电熔窑的工艺参数和电工技术参数列于表9.5.7。
表9.5.7 几种乳白玻璃电熔窑的工艺技术参数
玻璃配方编号 |
窑炉生产能力 T/d |
钼电极的功率 Kw |
熔化温度℃ |
100Kg玻璃冰晶 石的用量(Kg) |
玻璃中氟 的含量% | ||
火焰窑 |
电熔窑 |
火焰窑 |
电熔窑 | ||||
NO1 |
1.2 |
79.0 |
1340 |
28.0 |
10.1 |
4.6 |
4.8 |
NO2 |
1.5 |
54.3 |
1340 |
16.0 |
11.2 |
5.0 |
4.6 |
NO3 |
0.7 |
46.4 |
1310 |
26.0 |
10.1 |
4.5 |
4.7 |
NO4 |
0.5 |
40.1 |
1330 |
15.5 |
10.1 |
4.5 |
4.7 |
NO5 |
0.5 |
40.4 |
1320 |
10.1 |
4.8 |
某玻璃厂起初建造了一座出料量1.5T/d的电熔窑,但实际产量都是0.7T/d。后来在配合料中增加了一些冰晶石,玻璃中氟的残余量在4.6%左右。由于每隔10分钟往熔化池的表面加一次料,所以氟化物的挥发增加了,玻璃液中钼电极的电功率也增大了。鉴于玻璃液在流液洞和澄清池滞留的时间过长,因而出现了结晶,造成了该厂生产的乳白玻璃出现废品。此后该厂进行冷修改造,将电熔窑缩小使日生产能力降低为0.5T/d,从而消除了上述析晶缺陷。
砌筑电熔窑池壁的耐火材料是电铸莫来石砖或锆刚玉33#。砌筑电熔窑上部结构的耐火材料是硅砖。钼电极的电流密度在0.7A/cm2以下,用上述耐火材料砌筑的电熔窑和钼电极可使用一年半到两年不用更换。
5.电熔窑熔化乳白玻璃的特点
(1)电熔窑熔化乳白玻璃的优点之一就是各种生产工艺参数稳定性很高。某玻璃厂一周内生产的乳白玻璃样品中经化验氧化钠含量保持在11.3±0.1%,氧化钾含量保持在4.0±0.03%,氟含量保持在4.84-±0.06%,因此这个厂实际上杜绝了由于上述线膨胀系数和透光性的差别而产生的废品,双层乳白玻璃灯具的产品合格率大大提高了。
(2)与使用气体火焰窑相比,采用电熔窑熔化乳白玻璃冰晶石的消耗量降低了1~2倍,向周围大气排放出的各种烟气量降低10~15倍,窑炉的有效使用系数提高40~52%。
(3)此外用电熔窑生产的乳白玻璃的质量大大高于采用气体火焰窑生产的乳白玻璃。
例6 日产1.5T乳白玻璃的电熔窑
乳白玻璃可以通过引入氟化物、磷酸盐和高折射氧化物等方式来获得。考虑到电熔窑的特点和原料来源,选择氟化物为乳浊剂。为了保证制品具有一定的白度,乳浊剂的含量(以F-计算)以4~5%为宜。乳浊剂用量过低时,玻璃半透明、白度偏低;用量过高时,玻璃的白度并无明显增大,反而易出现析晶,严重时会使制品表面变得粗糙。一般氟乳白玻璃多是由氟硅酸钠引入氟化物的。为了减少氟化物的挥发和促进乳浊,在玻璃成分中引入了较高含量的Al2O3,其理由是:在熔制过程中,如无Al2O3存在时,氟硅酸钠会产生气态的SiF4。其反应如下:Na2SiF6=2NaF+SiF4↑。当引入Al2O3时,氟硅酸钠与氧化铝结合生成稳定的氟铝化合物,其反应如下:2Na2SiF6+Al2O3+Na2O→2Na3AlF6+2SiO2
由于氟化物的挥发是随熔化温度提高而急剧增大的,因此,一般乳浊玻璃的R2O含量都较高,以降低熔化温度,减少氟化物的挥发。为了促进乳浊,改善析晶能力,提高制品光泽,引入一定量的K2O。考虑到电熔对玻璃液电阻的需求和成形工艺的要求,白色玻璃中R2O的含量约为18~19%。
该电熔窑的生产以碎玻璃为主要原料。有以下优点:(1)由于原料中没有难熔的硅质原料,可以在较低温度下熔制。这就大大降低了氟化物的挥发,减少了环境污染。(2)由于熔制温度低,大大减轻了玻璃液对电极及耐火材料的侵蚀,有利于延长电极和耐火材料的寿命。(3)由于碎玻璃中已含有大量的碱金属氧化物,可以大大减少原料中的碱耗,有利于降低原料成本。(4)由于熔化温度低,熔化耗热量少,熔窑热散失减少,有利于降低能耗。
有人认为,碎玻璃的用量,以配合料的25~30%较好,熔化钠钙硅酸盐玻璃时,碎玻璃用量超过50%时,会降低玻璃质量,使玻璃发脆,并难以澄清。
也有人认为,只要补充足够的易挥发氧化物,保持玻璃成分稳定,并使玻璃充分均化,则大量使用碎玻璃时,钠钙硅酸盐玻璃的机械强度也不会降低。同时,只要控制好合适的碎玻璃粒度,并增加适当的澄清剂,也会得到较好的澄清效果。
该电熔窑碎玻璃在原料中的含量高达70~90%,并没有对生产过程和产品质量产生任何不利影响。表9.5.8给出若干废玻璃的化学成分。
表9.5.8 各种废玻璃的化学组成
序号 |
名称 |
SiO2 |
Al2O3 |
Fe2O3 |
Ca0 |
mgO |
R2O |
其它 |
1 |
引上平板玻璃 |
72.09 |
2.32 |
0.19 |
6.34 |
4.01 |
14.43 |
|
2 |
压延平板玻璃 |
71.79 |
1.84 |
0.13 |
10.44 |
1.74 |
13.88 |
|
3 |
浮法平板玻璃 |
71.91 |
1.48 |
0.22 |
8.10 |
2.97 |
14.08 |
|
4 |
白酒瓶玻璃 |
71.5 |
3.0 |
0.06 |
7.5 |
2.0 |
15.0 |
|
5 |
罐头瓶玻璃 |
69.0 |
4.5 |
0.27 |
9.0 |
2.5 |
15.0 |
BaO0.6 |
6 |
氟乳白玻璃 |
71.20 |
7.30 |
4.80 |
14.20 |
F-4.2 |
为了保证产品质量和生产工艺稳定;废玻璃均应加工成粉状,对于每批进厂的废玻璃粉均应进行化学成分分析和水分测定。
碎玻璃的粒度小于0.25mm和粒度为2~20mm时,两者对熔化均有良好的效果。碎玻璃的熔化速度主要取决于碎玻璃物料的导热性能和碎玻璃颗粒的熔化速度。一般说来,碎玻璃颗粒的熔化速度和粒度成线性关系,而碎玻璃物料的导热性能又正比于其堆积密度。当碎玻璃颗粒小于0.25mm时,颗粒本身的质量很小,较小的热量就足以使其迅速熔化,形成导热性能较好的玻璃液。而0.25~2.0mm范围内的碎玻璃颗粒,颗粒的熔化速度虽然较快,但是完全熔化还需一定的时间。由于该粒度的物料堆积密度较低,包含的气体较多,当颗粒表面熔化后,容易互相粘结,形成包裹大量气体的泡沫烧结层,使导热性能变得更差,从而影响熔化速度。当碎玻璃颗粒在2~20mm时,虽然颗粒本身的熔化速度较慢,但物料的堆积密度较高,导热性能较好,因此综合熔化速度较快。为了使废玻璃能与辅助原料充分混合,保证色调均匀,利于快速熔化,避免出现澄清困难,将颗粒控制在0.25~0.10mm之间。
由于普通玻璃常用的澄清剂As2O3和Na2SO4在高温下氧化能力很强,能使钼电极氧化,特别是Na2SO4在高温下分解出O2和SO2的混合体,与钼反应生成MoO3和MoS4,对钼电极的侵蚀严重。因此选择硝酸盐作为澄清剂,其主要优点是:(1)硝酸盐熔点低,分解温度低,在配合料的烧结过程中就能与废玻璃的表面作用,因此对废玻璃的澄清效果明显。(2)硝酸盐的引入,可促使Fe2+向Fe3+转化,有利于乳白色废玻璃的脱色。(3)硝酸盐的分解反应是在配合料—玻璃液的交界面进行的。因此放出的氧气只是集聚在玻璃液上部,对钼电极的侵蚀作用小。以普通平板玻璃为主要原料,白色玻璃中引入了76%。部分Al2O3由长石引入,纯碱补充了部分Na2O,澄清剂为硝酸钾和硝酸钠。
表9.5.9 乳白玻璃形成过程理论耗热计算表
项目 |
白色玻璃Kcal/Kg |
加热玻璃到熔化温度的耗热 |
330.05 |
加热去气产物到熔化温度的耗热 |
44.00 |
生成硅酸盐的耗热 |
7.75 |
形成玻璃的耗热 |
23.67 |
蒸发水分的耗热 |
15.87 |
原料带走的热量 |
-4.17 |
合计 |
417.17 |
全电熔工艺带来了明显的节能效果。实际生产应用中平均日出料量1.5吨,乳白玻璃中碎玻璃含量为76%,熔化温度为1150℃(玻璃液温度),计算得出黑白玻璃形成过程理论耗热如表9.5.9所示。
经换算可以得出,乳白色玻璃理论耗电0.488Kwh/Kg,根据实际生产测定的结果,每公斤乳白色玻璃平均耗电约0.75Kwh,所以电熔窑的热效率大致为64%。
此页网址为:
相关文章